When it comes to designing PCBs, extreme heat could result in the loss of money and time if your efforts fail to optimize the heat dissipation and distribution of your board. While conducting a precise mathematical analysis of the thermal component of a printed circuit board is a complicated process, it’s possible to implement some simple measures to manage the thermal resistance of your design.
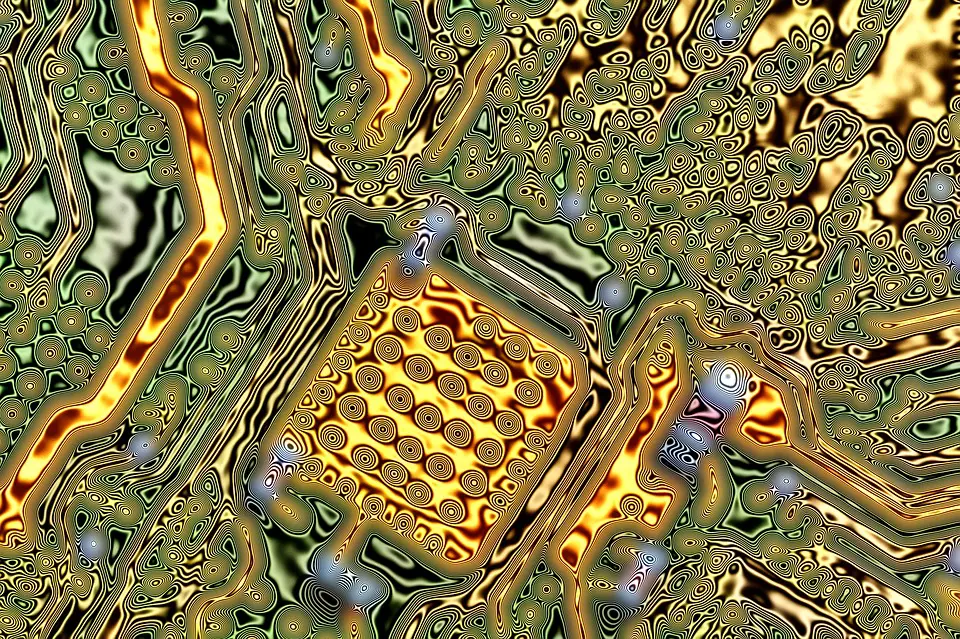
(Pixabay / InspiredImages)
Identifying Heating Issues in a PCB
The easiest way to detect heating issues in a PCB is to look for signs of dry joints, partly burnt or damaged components, arching, etc. Other visible signs may include discolored spots and bulging components on the board. The smell from the PCB can be another indication of heating problems. Moreover, engineers can leverage “IR cameras” to analyze powered boards for excessive heating and detect problems invisible to the naked eye.
In addition to revealing areas with excessive heat, the IR may also help identify defective or counterfeit components whose thermal resistance differs from those of original parts. The cameras can also identify the locations with insufficient solder.
Steps to Removing Heat from Printed Circuit Boards
There are several ways you can increase and manage the thermal resistance of PCBs. Here are some of the most popular methods.
1. Increase dissipation through thermal vias
Thermal vias create a bath for thermal and electrical energy to move from one layer to another on a printed circuit board. You can liberally use vias on surface mounted devices to eliminate heat from high power parts. Thermal vias also enhance the area and mass of the copper, improving heat dissipation from the crucial parts via conduction. As such, putting vias near the source of the heat tends to improve overall performance. In certain applications, the device (like a thermally optimized IC) ensures that the heat is conducted away due to the combined use of a pad and thermal via array.
2. Keep temperature coefficients when selecting materials and components
The extent of thermal resistance for your components and traces depends on the parts and the characteristics of the board materials that you use. Hence, a key step in managing the resistance of your PCB is to choose components with favorable temperature parameters and resistances. For instance, FR-4, which is also the most commonly used PCB design material, is an excellent insulator, which means it has a high thermal resistance. Therefore, it might not be the best option when it comes to relieving high concentrations of heat on your board.
3. Consider using heat pipes
These are ideal for compact devices with restricted space. The pipes offer a cost-effective and reliable way to transfer passive heat. Other advantages of heat pipes include high-quality thermal conductivity, vibration-free operation, minimal maintenance, and silent functioning as they don’t contain any moving part. Typical pipes carry small quantities of acetone, water, ammonia, or nitrogen. The fluids assist in absorbing the heat, after which they produce a vapor that transfers through the pipe. The condenser of the pipe, through which the vapor travels, condenses the element back to its liquid state, and the cycle keeps repeating itself.
4. Keep a good distance between high power components
Components that tend to produce excessive heat should be sparsely installed on your PCB. Being strategic with their placement helps reduce high-temperature environments that are highly likely to malfunction during the board’s assembly reflow. Remember that high power components may leverage heat sinks to push heat away from components and into the surrounding air. It’s recommended that you take the component’s dissipation into account during the heat reflow, where variations of 80°C or more may be generated across the board. And when it comes to power resistors, relatively big components should be selected, and adequate space for heat dissipation should be left for them in the layout of the PCB manufacturing process.
5. Apply thermal assembly technology where relevant
Thermal assembly technology should be used on PCBs to enhance heat transmission. The majority of the heat produced by components such as microprocessors and ICs is transferred to circuit boards via their own leads whose “assembly holes” should be leveraging metal-placing holes. The components can also be placed directly on the board or thermal conduction stick to manage thermal resistance generated by components.
Final Verdict
PCB thermal resistance management depends on various factors including the volume of heat the circuit and components dissipate, the enclosure, the environment and the overall design. When the generation of heat is low, the circuit can function without extra cooling.
The main goal is to keep the thermal resistance manageable so that you can preserve the life and assembly of your boards. Of course, using a PCB resistance calculator or thermal analysis software will enable you to make great layout decisions as part of your PCB prototypes.
To offer thermally optimized circuit boards, temperature should be a major consideration right from the design stage and weighed carefully at every ongoing stage of printed circuit board assembly and quality assurance.