The advancement in modern scientific technology has resulted in the shrinking size of electronic components and the widespread use of SMT, or surface mount technology, in electronic products. SMT manufacturing devices are fully automated, highly precise, and operate at high speeds.
As the degree of automation increases, the demands on PCB design also grow. If the PCB design does not meet the requirements of the SMT device, it can affect the efficiency and quality of the manufacturing process or even cause automatic SMT to fail. Poor design of the PCB shape, clamping edge, and panel can also impact manufacturing efficiency, leading to pad defects or failure to complete the manufacturing process.
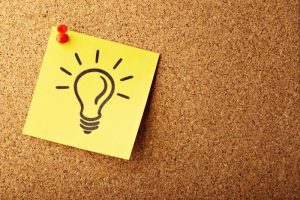
(AbsolutVision/Unsplash)
PCB Design Elements Impacting SMT
Surface mount technology is a cutting-edge method of electronic manufacturing that places and solders components on a designated spot on the PCB. Unlike traditional through-hole technology (THT), SMT is characterized by a higher degree of automation, making it suitable for large-scale automated manufacturing.
Printed circuit board design is a crucial aspect of SMT and a key determinant of the quality of SMT manufacturing. Below, we will examine the elements of PCB design that impact its quality from the perspective of SMT equipment manufacturing.
The requirements for PCB design from SMT devices mainly include:
PCB Size
The design size of the PCB must meet the maximum and minimum size requirements of the printer and chip mounter, which are typically in the range of 50mm x 50mm to 330mm x 250mm (or 410mm x 360mm). If the PCB is too thin, its design size should not be too large, or it may deform due to the reflow temperature. The ideal length-to-width ratio is 4:3 or 3:2.
If the size of the PCB is smaller than the minimum size requirement of the equipment, it must be grouped into panels. The number of panels is determined based on the size and thickness of the PCB.
Pattern
The production of a printed circuit board for automatic SMT starts with loading it onto the production line and ends with unloading the finished board. During the production process, the PCB is conveyed along the device’s path and must be designed to match the path of transmission between devices.
A standard rectangular PCB with a flat pathway clamping edge is ideal for transmission. Sometimes, a right angle is added to the edge to form a chamfer.
However, if the pathway clamping edge isn’t straight, it can cause issues with PCB location and transmission in the device. To correct this, you can fill the open space to make the clamping edge straight or add a crack edge to the PCB.
Clamping Edge
As the printed circuit board is conveyed through the device, components must not be placed along the direction of the clamping edge, or they may be compressed by the device, affecting chip mounting. For example, some components may be located near the lower edge of the PCB. When this happens, the upper and lower edges should not be used as clamping edges. However, if there are no components near the two side edges, those two short edges can be used as clamping edges.
Trace Width
Trace width is an important element that can impact the quality of the SMT process in PCB design. Trace width refers to the width of the conductive lines or tracks on a printed circuit board. The width of the trace determines the amount of current that can flow through it, so it is important to design the trace width appropriately.
To determine the appropriate trace width, several factors must be considered, including the current flow, the thickness of the trace, the material used for the trace, and the temperature requirements. In general, higher current flow requires a wider trace width. The trace width should also be adjusted to accommodate for the thermal expansion and contraction that occurs during the soldering process.
Another important consideration is the spacing between the trace and other components on the PCB. The trace should be spaced far enough from other components to prevent short circuits but close enough to ensure efficient use of space on the PCB.
Via Design
Via design is another important element in PCB design that can impact the quality of the surface mount technology process. A via is a conductive connection between the layers of a multi-layer PCB. Proper design is essential to ensure that the electrical signals are transmitted properly through the circuit board.
Factors to consider in via design include the diameter, aspect ratio, and placement of vias. The diameter should be large enough for adequate current flow, and the aspect ratio should be optimized to ensure proper connection between layers. Place vias near the components they are connecting and space them apart from each other to prevent short circuits and ensure efficient use of space on the circuit board.
By considering these factors, you can ensure that electrical signals are transmitted efficiently and effectively in the SMT process.
Mark
The PCB Mark serves as a key identifier for automatic devices and helps to correct any manufacturing errors. When designing the mark, it is important to consider its shape (preferably a solid circle), size (0.5mm to 3mm, with a solid circle of 1mm diameter being the ideal choice), and surface (even and reflective, like the soldering plane of the PCB pad).
It is important to have a clear background area around the mark and other pads without any silkscreen or solder mask. Poor designs with silkscreen characters or lines near the mark can cause frequent device identification errors and negatively impact manufacturing efficiency.
As you can see, SMT printed circuit board design requires careful consideration of various elements such as trace width, via design, and PCB mark to ensure smooth production in the SMT production line. We hope this post has been helpful to you.
Our company offers SMT manufacturing services, specializing in through-hole and SMT circuit board assembly. Contact us today to learn more.
Infographic
With technological advancement on the rise, electronic components are catching up and taking the opportunity for better quality products and faster delivery time. It is known to many that the demands for PCB design are steadily increasing alongside automation. This can make the manufacturing process faster, but can also risk greater losses with just a few minor errors. That is why it is crucial to learn about the PCB design elements that can affect the SMT manufacturing process.
Video
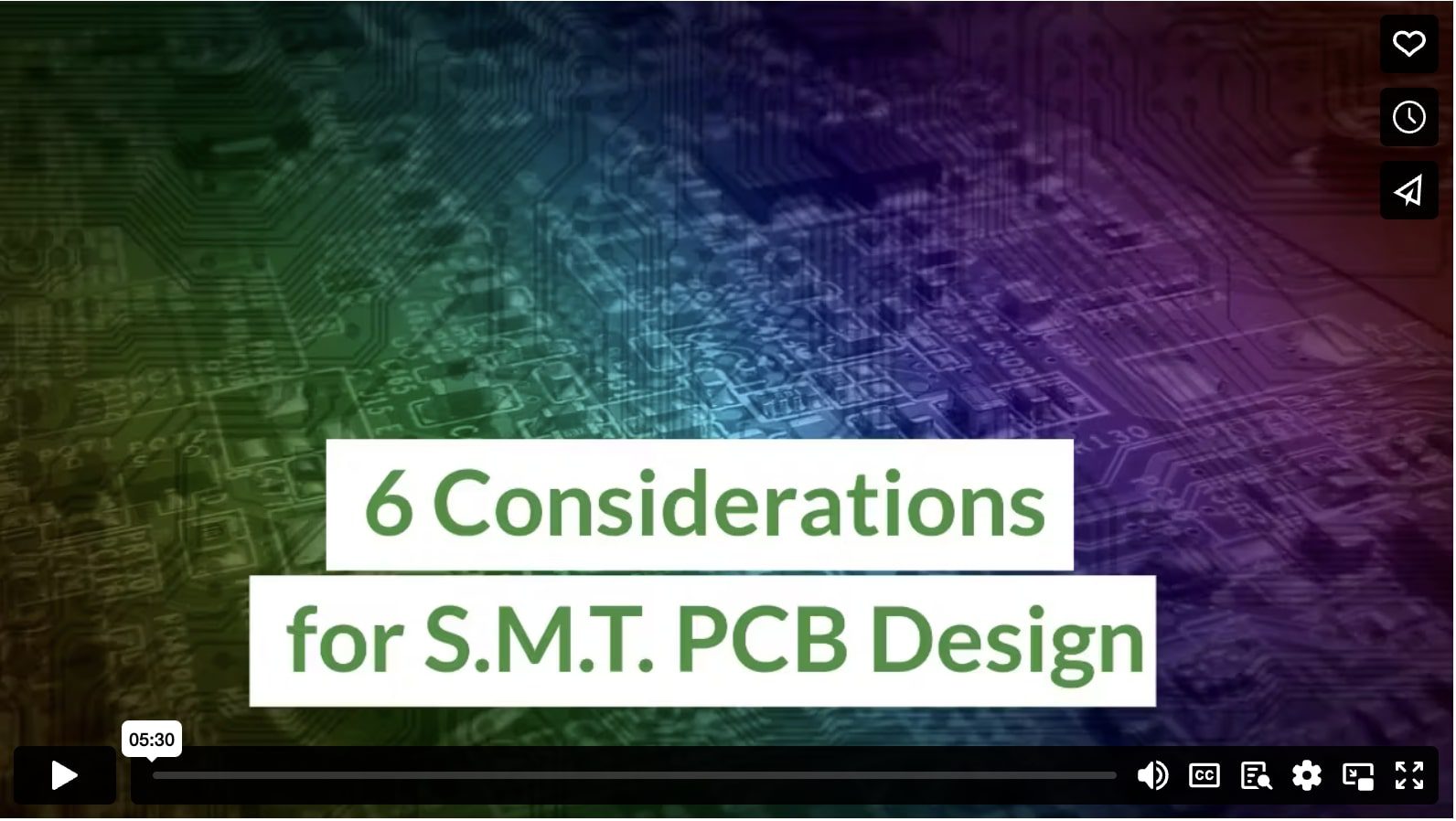