During Printed Circuit Board (PCB) production, several issues can occur to any of the many parts used to build them. When it comes to Surface Mount Technology (SMT), the most frustrating of these issues is the presence of solder balls.
Today, we will explore what causes solder balls and how you can prevent them during SMT manufacturing.
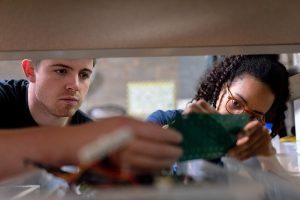
(ThisisEngineering RAEng / unsplash)
What are Solder Balls?
Solder balls are balls of metal alloy that form on the surface of a PCB after completing the soldering process. They constitute one of the biggest problems PCB Assembly manufacturers face.
If solder balls appear, they can affect the overall functionality of the circuit board. Small solder balls are unsightly and can move components slightly off-mark. In the worst cases, bigger solder balls can fall off the surface and deplete the quality of the component joints. Worse still, some balls can roll onto other board parts, leading to shorts and burns.
A few reasons why solder balls occur include:
- Excess humidity in the construction environment
- Dampness or moisture on the PCB
- Too much flux in the solder paste
- Temperature or pressure is too high during the reflow process
- Insufficient wiping and cleaning post-reflow
- Solder paste is insufficiently prepared
Ways to Prevent Solder Balls
With the causes of solder balls in mind, you can apply various techniques and measures during the manufacturing process to prevent them. Some practical steps are:
1. Reduce PCB Moisture
The PCB base material can retain moisture once you set it into production. If the board is moist when you begin applying solder, solder balls will likely occur. By ensuring the board is as free of moisture as possible, the manufacturer can prevent them from occurring.
Store all PCBs in a dry environment, without any nearby sources of moisture. Before production, check over each board for signs of dampness, and dry them off with anti-static cloths. Remember that moisture can bead up in solder pads. Baking the boards at 120 degrees Celsius for four hours before each production cycle will evaporate any excess moisture.
2. Choose the Correct Solder Paste
Substances used to make solder can also produce solder balls. Higher metal content and lower oxidation within the paste reduce the chances for balls to form, as the solder’s viscosity prevents it from collapsing while heated.
You can use flux to help prevent oxidation and ease the cleaning of boards after soldering, but too much will lead to structural collapse. Choose a solder paste that meets the criteria necessary for the board being made, and the chances of solder balls forming will drop considerably.
3. Preheat the PCB
As the reflow system begins, the higher temperature can cause a premature melting and evaporation of the solder in such a way as to cause it to bubble and ball. This results from the drastic difference between the board material and the oven.
To prevent this, preheat the boards so they are closer to the oven’s temperature. This will lessen the degree of change once heating begins inside, allowing the solder to melt evenly without overheating.
4. Don’t Miss the Solder Mask
Solder masks are a thin layer of polymer applied to a circuit’s copper traces, and solder balls can form without them. Ensure that you properly use the solder paste to prevent gaps between the traces and pads, and check that the solder mask is in place.
You can improve this process by using high-quality equipment and also by slowing down the rate at which the boards are preheated. The slower preheat rate allows the solder to spread evenly without leaving spaces for balls to form.
5. Reduce PCB Mounting Stress
The stress put upon the board when it is mounted can stretch or condense the traces and pads. Too much inward pressure and the pads will be pushed closed; too much outward stress and they will be pulled open.
When they’re too open, the solder will be pushed out, and there won’t be enough in them when they’re closed. Make sure that the board is not being stretched or crushed before production, and this incorrect amount of solder will not ball up.
6. Double Check Pad Spacing
If the pads on a board are in the wrong places or too close or far apart, this can lead to solder pooling wrong. If solder balls do form when the pads are incorrectly placed, this increases the chance that they will fall out and cause shorts.
Ensure that all plans have the pads set at the most optimal positions and that each board is printed correctly. So long as they are right going in, there should be no issues with them coming out.
7. Keep an Eye on Stencil Cleaning
After each pass, you should properly clean the excess solder paste or flux off the stencil. If you don’t keep excesses in check, they will be passed on to future boards during the production process. These excesses will bead on the surface or overflow pads and form balls.
It’s good to clean excess oil and solder from the stencil after every round to prevent buildups. Sure, it can be time-consuming, but it’s far better to stop the issue before it aggravates.
Solder balls are the bane of any EMS assembly manufacturer’s line. Their problems are simple, but their causes are too numerous. Fortunately, each stage of the manufacturing process provides a new way to prevent them from occurring.
Scrutinize your production process and see where you can apply the above steps to prevent the creation of solder balls in SMT manufacturing.