In this day and age, PCBs can be found in various electronic devices such as computers, televisions, digital cameras, and cell phones, to name but a few. Seeing that these devices each serve a different purpose, it goes without saying that there are also different types of PCBs to accommodate different applications. In this article, we’ll discuss the basic types of PCBs along with their assorted characteristics. Let’s get going.
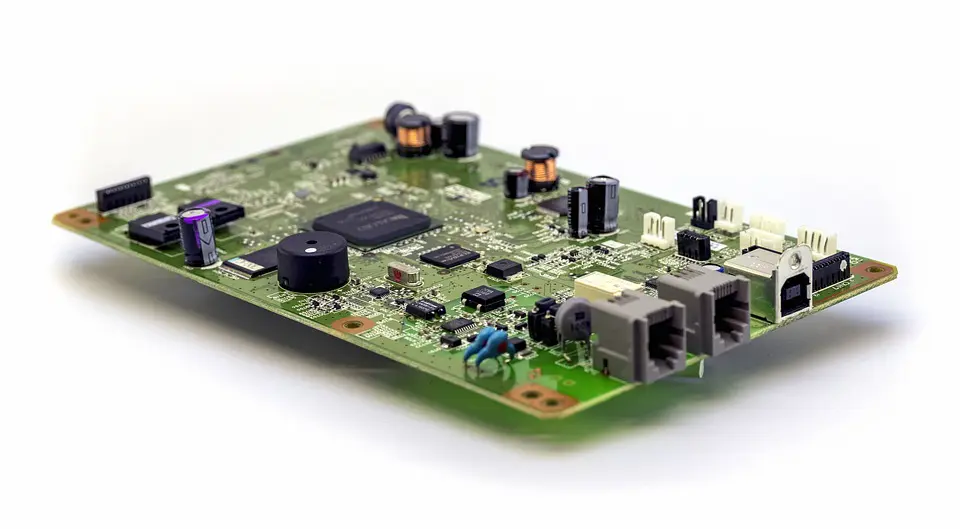
(Pixabay / Panals)
Rigid PCBs
Rigid PCBs are constructed out of flat, solid substrate materials that are resistant to bending, such as fiberglass. This is probably the most commonly used PCB as its inflexibility is useful in applications such as computer motherboards. Though rigid PCBs are usually single-sided, they are also available in double-layer and multi-layer configurations.
Aluminum-backed PCBs
Though very similar to traditional PCBs, aluminum-backed PCBs feature aluminum or copper substrate boards instead of fiberglass. Aluminum is non-toxic and can easily be recycled, making this type of PCB more eco-friendly. Aluminum is also excellent at conducting and transferring heat, which makes it ideal for dissipating heat away from crucial circuit board components and increasing their lifespan. It’s also more durable than its fiberglass and ceramic counterparts, which minimizes damage during the manufacturing, installation, or handling of the PCB.
Flexible PCBs
Some installations, like those found in compact and/or high-performance devices, require more sophisticated PCBs that can flex and move. Examples of such devices are GPS units, smartphones, and tablets. Flexible PCBs are constructed using soft insulating materials such as laminated plastics, which makes them more lightweight than rigid PCBs. They have the ability to bend and twist and can, therefore, be adapted to fit existing casing designs.
This eliminates the need for manufacturers to create specific casings to house the PCBs. Though flexible PCBs may cost a bit more to manufacture, they can reduce the overall production cost of the device as they eliminate the need for other parts such as wire harnesses. As with rigid PCBs, flexible PCBs can also be configured in single-layer, double-layer, or multi-layer formats.
Rigid-flex PCBs
As the name implies, a rigid-flex PCB is a combination of rigid and flexible circuitry. This type of PCB can be manufactured without solder joints, connectors, and contact crimps. It also reduces the number of parts needed for the board design, as well as the overall board size and package weight. Rigid-flex PCBs can be used in a variety of applications that even include medical devices such as pacemakers. They are also very popular in the military and aerospace industries.
Single-layer PCBs
Single-layer PCBs, also referred to as single-sided PCBs, consist of only one layer of base material or substrate. One side of the substrate is covered in a thin layer of conducting metal, which is usually followed by a protective solder mask and silkscreen that mark the different elements and components of the circuit board. All components are then soldered onto one side of the PCB, which makes this an easy, low-cost design. These types of printed circuit boards are typically used for devices that are manufactured in bulk, such as calculators and printers.
Double-layer PCBs
Double-layer PCBs, or double-sided PCBs, also consist of only one layer of base material or substrate. However, in this design, the thin layer of conducting metal is applied to both sides of the substrate. There are two methods of connecting circuits and components on double-layer PCBs. Let’s take a closer look at them:
- Through-hole mounting: In this method, small wires are fed through drilled holes from one side of the board to the other. Each end of the wire is then soldered to the right component. Though this is a very reliable method that ensures strong mechanical bonds between components, it can be more expensive than surface-mounting.
- Surface-mounting: In this method, components are mounted directly onto the surface of the PCB. This method allows PCBs to have a higher circuit-density and to be smaller or more compact. It also eliminates the need for holes, which reduces manufacturing costs.
Multi-layer PCBs
Multi-layer PCBs consist of three or more layers of conductive material. A specialized glue is used to secure them together, and insulation is added to the outer layers to keep excess heat from melting any of the components. These types of PCBs can be designed for more complex applications such as satellite systems and medical equipment.
The quantity of layers generally falls within the range of four to 12 layers, though much larger multi-layer PCBs have been built before. The length of these PCBs varies widely, too. Earlier this year, a UK company by the name of Trackwise successfully manufactured a flexible multi-layer PCB that measures over 85 feet in length. This is believed to be the longest PCB ever produced.
High-frequency PCBs
These are specifically built to deliver signals in the 500MHz to 2GHz frequency range. The special materials needed to manufacture these PCBs can make them rather expensive. High-frequency PCBs are used in more complex applications such as automatic radar systems, RFID tags, and missile guidance systems.
A final word
PCBs are no longer limited to single-layer circuit boards that can be found in domestic desktop computers. The evolution of technology has driven the need for more sophisticated PCB designs to accommodate more complex systems.
Contact My EMS Solutions for help with printed circuit board assembly, test solutions, and design collaboration.