There was a time when electronic products consisted of a small number of components and circuit elements. Estimating production costs was fairly straightforward. After all, the fewer parts and components there are in a product, the less time-consuming and the more accurate cost estimation tends to be.
Today, a circuit board can house many more complex components than the pre-integrated circuit era boards. So it’s no surprise that many entrepreneurs struggle to make accurate cost estimates of a new electronic product.
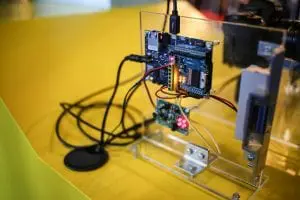
(g-trema / pixabay)
It is generally easier to understand a complex process by breaking it down into stages. Following this principle, this article will break down the costs associated with each stage of a typical electronic manufacturing process.
Development
Prototyping
Estimated cost: $2,000 – $8,000
Electronics constitute the most expensive and complicated aspect of the whole product development process.
Development typically starts with prototyping, a crucial step in its own right. The blank PCB production usually costs one-third of the prototyping costs, while board assembly usually takes the other two-thirds.
Enclosure Costs
Estimated costs: $4 – $1000
Even if your product is 100% electronics, it will still require an enclosure to be fitted into (unless your target market is DIY enthusiasts). The enclosure is the interface for consumers to use your product, so it has to be intuitive, reasonably durable, and sturdy to protect the electronics within.
An enclosure can be as simple as a stock plastic protection for the circuitry within or as complicated as a custom-designed (by 3D printing or CNC machine) enclosure.
Retail/Packaging
Estimated costs: $2000/1,000 pieces – $3000/1,000 pieces
The retail aspect of even the highest quality of products is just as important as any other phase in the development process. New entrepreneurs tend to overlook the importance of packaging, but it is important to realize that an appealing package can often influence consumers to purchase a product.
After all, sales and profits are the ultimate goals of any business. You’ll only be limiting your product’s sales potential by skimping on money for retail/packaging.
Scaling
Certification Costs
Estimated costs: $3,000 – $20,000 (depending on the number of certifications and specifications of product)
All electronic devices, no matter how small, radiate some form of electromagnetic energy. As a result, governments require certifications before you can mass-produce an electronic product in order to ensure your product won’t interfere with RF communication applications already in place in your region.
In the US, all electronic manufacturers have to purchase FCC Certification to market and sell their products. It also serves as a guarantee that your product doesn’t radiate any frequencies that can disturb radio communications.
In addition to the FCC Certification, you will need several other certifications, including UL and RoHS. If you plan to sell your product outside the US, you will need CSA (for Canada) and CE (for Europe).
Manufacturing Setup Costs
We’re now moving into the territory where generic estimations become impossible and are entirely dependent on your particular electronic product’s nature, scale, and specifications. Chief among these is the cost to set up a manufacturing unit.
The major cost of a manufacturing setup consists of injection molds that produce custom plastic pieces. These machines will produce the enclosures for your product, and, in the long run, producing your own enclosures will prove to be far more cost-effective than purchasing ready-made stock enclosures.
The cost of an injection mold varies by factors such as the hardness of the mold’s steel (the harder the steel, the higher the machine’s manufacturing capacity), the number of cavities, and side actions. But this is a long-term investment. An injection molding machine will typically last you 8-12 years.
Landed Manufacturing Costs
This is the phase where you’ve gone past all the prototyping, certifications, and scaling. Reaching this stage is a commendable milestone on its own but also the toughest to pull through.
Put simply, landed manufacturing is the total cost that your electronic product will incur from production to transportation. Once again, it’s difficult to estimate costs without knowing the exact nature of a product, but it helps to understand all the individual costs it covers.
These include manufacturing costs, inventory costs, and transportation/shipment costs. The inventory cost is the cost of your product multiplied by the quantity produced. If you have a good estimate of manufacturing cost on one product item, you can determine inventory costs fairly easily. But it is the manufacturing part of the process that will take up the bulk of your costs:
- Electronic components: It is hard to accurately estimate the cost of electronic components, given the sheer number of components that make up a typical circuit. All the same, a good estimate of this cost is essential for managing your finances well.
- PCB production and assembly: The size and routing layers determine the cost of a blank PCB, while assembly cost is determined by the number of electronic components in the circuit, pin pitch, etc. An electronic manufacturing services company can provide you with a better estimate of the overall costs.
- Injection mold plastic parts: The weight, size, and type of plastic used determines the cost of injection mold plastic parts. Since these factors largely remain invariable, it isn’t easy to control cost in this phase.
- Mechanical parts: The screws, springs, gears, and levers make up the cost of mechanical parts that fit into your final enclosure product.
- Final product assembly: This is where you put everything together to assemble a complete, standalone, functional product.
- Testing: The final product needs testing to ensure it meets all quality specifications.
These are almost all of your manufacturing costs, but there are also miscellaneous costs associated with:
- Scrap rate
- Packaging
- Returns
- Freight
- Duties
Conclusion
Hopefully, you now have some idea of what goes into budgeting to develop a new electronic hardware product. The estimates will vary depending on specific production requirements, but you at least have some benchmarks to compare quotes against. The foundations of successful electronics product development lie in realistic planning, expectations, and budgeting.
Video
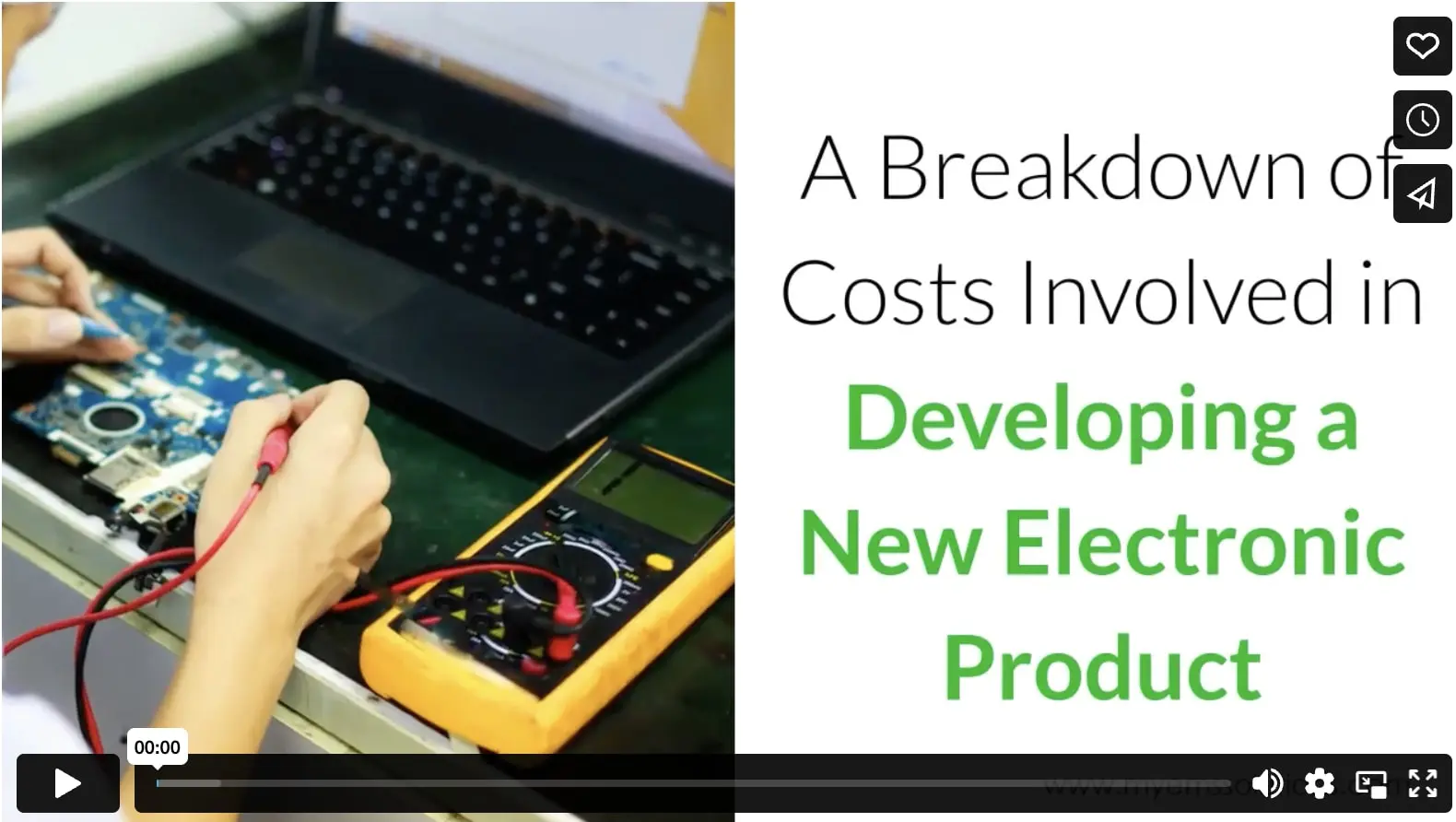