Ask anyone with some knowledge of electronics to describe a PCB, and they’ll probably describe it as a green-colored board that serves as the base in electronics. However, solder masks – the active layer of liquid photo image lacquer present on the bottom and top of a PCB – can be a color other than green.
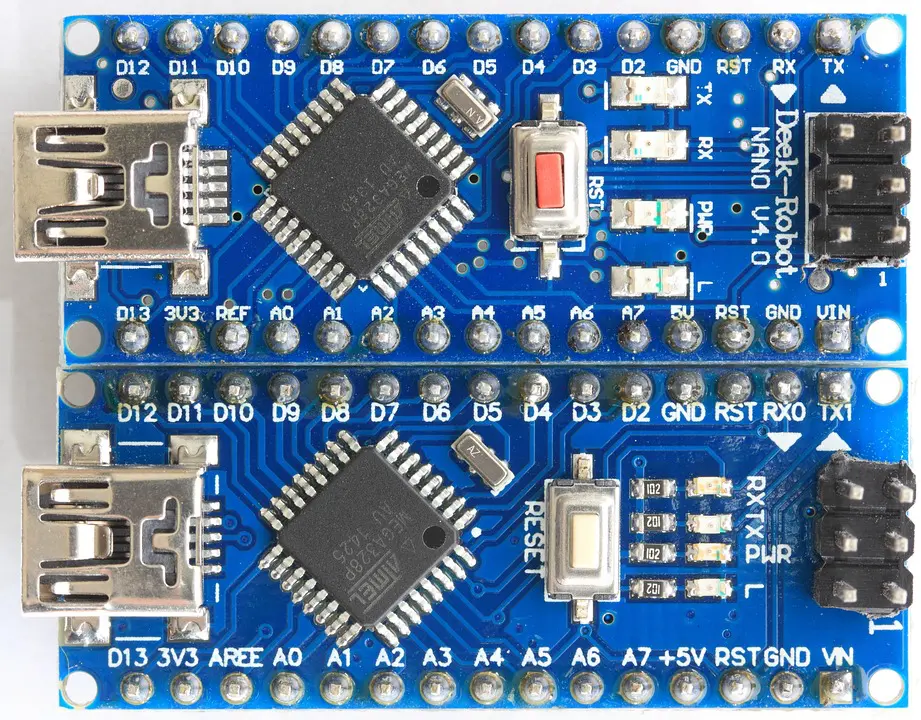
(Pixabay / 2427999)
Solder masks lend security and identity to printed circuit boards, and their color represents the PCB’s finishing color. In recent years, assemblers have been using other colors rather than green to achieve contrast or brightness. Some assemblers also refer to colors of the solder mask as PCB color codes.
Different PCB/Solder Mask Colors and When to Use Each
Solder mask colors do not have any effect or impact on a PCB’s performance. Designers and assemblers use different colors to give a highly visible indicator of revisions and help prevent slip-ups in a mixed assembly project.
The following are the different solder mask colors you can choose:
Green
Green is the most popular solder mask color for PCBs. This particular color is easy on the eyes and delivers high contrast between planes, traces, and the empty space on the board. Green solder masks have the PCB color code #008C4A. Green finishing also reflects less light and offers the right contrast with the white silkscreen. It’s available in different varieties, including matte and glossy variants.
Red
Red solder masks are becoming popular due to the contrast and visibility they offer for traces, planes, and no-copper areas. Red also makes the PCB look bold and compelling. If the board is visible from the outside of a finished product, the red solder mask will bring a sense of freshness compared to stale industry colors. What’s more, red also makes the silkscreen stand out well and allows for easy cleaning of flux residues. Red solder masks have the PCB color code #D0011B.
Blue
Arduino boards contain blue solder masks. Assemblers of these boards use blue against the silkscreen to achieve high contrast. The color also enhances the PCB’s aesthetic appeal. It is even suitable for mounting on liquid crystal displays (LCDs) as it doesn’t produce bright background colors or sharp contrasting edges. However, blue’s contrast is shallow compared to green and red solder masks on a standard circuit board. So if you’re going to use blue, you may need to use magnification to identify manufacturing-related defects. Blue solder masks have the PCB color code #4990E2.
White
With the PCB color code #ECECDF, white solder masks are typically used for LCB applications. They can also make any artwork on the silkscreen layer stand out with high contrast of black printing. However, they have the lowest contrast of all PCBs on a general level – they’re hard to display correctly even under lighting. Cleaning them, too, requires a lot of effort as you need to remove the stains to make the panel look neat. As such, white solder masks are only used on a selective basis.
Black
Black solder masks offer more visibility than the white ones, and while the contrast is minimal, they make it easier to see large components and labeling. Black also looks great on LCD back panels. When black is put on the background, the eyes aren’t distracted by the screen’s details. That said, black solder masks can cause an increase in heat, which can discolor the silkscreen (turning it into light brown during the reflow process). The assembler who opts to use black must place a temperature sensor on the board. The black solder masks are available in matte and gloss finishes, with the former having a slightly better contrast. You can distinguish black PCBs using the color code #000000.
Yellow
Yellow achieves the same contrast between planes, no-copper areas, and traces as green, but its silkscreen doesn’t offer a high contrast with the board. The assembler can address the silkscreen issue through black silk printing, even though it might not bring the desired result. Yellow PCBs are easy to clean when it comes to light-colored residues. If you have certain routes to highlight, consider using a dark yellow solder board to capture attention. Yellow solder masks have the PCB color code #F6A624.
Purple
Purple is the perfect color choice for achieving a good contrast between the planes and traces on the surface. Purple solder masks are typically used for submarine PCBs. However, they’re not the best for displaying white silk printing. If you’re looking for a vibrant color to complement an immersion gold surface, purple might be a good option to consider – though it’s going to cost more than other PCB colors due to its unique and vibrant outlook.
Does the Type of Solder Mask Finish Affect PCB Performance?
In a word: no. Whether your solder mask color is gloss or matte, it won’t make your board function differently. The aesthetic is what should guide your solder color choice. Matte finishes are slightly softer and dull, so they won’t reflect a lot of light directly. They are also more susceptible to scratches than their glossy counterparts. However, they make it easy to identify PCB issues, as they appear darker and are easier to analyze in good lighting.
Glossy finishes tend to be harder but lighter, which helps them reflect more light. However, the PCB details aren’t as often lost in harsher light as in non-gloss finishes. Glossy colors also make the scratches less apparent. But you should steer clear of highly reflective gloss finishes as they can make inspection more challenging.
It’s worth mentioning that both gloss finish and matte finish cost almost the same and are subject to the same production process, so the choice is more about aesthetic than anything else.
You can pick a certain solder mask color from the ones we’ve mentioned in this article. The decision will mostly depend on your application needs. While most contract electronic manufacturers will tell you that the green solder mask is superior in many applications, other PCB colors might be more suitable in specific cases.