As an experienced PCBA manufacturer, we understand that a lot can go wrong during the PCB copying process, including the deformation of the film. To give an example, the failure of humidity control and temperature will result in negative film deformation. A high temperature of the exposure machine is another reason why films deform. Regardless of the source, the presence of negative film deformation affects the performance and quality of the final PCB copy board.
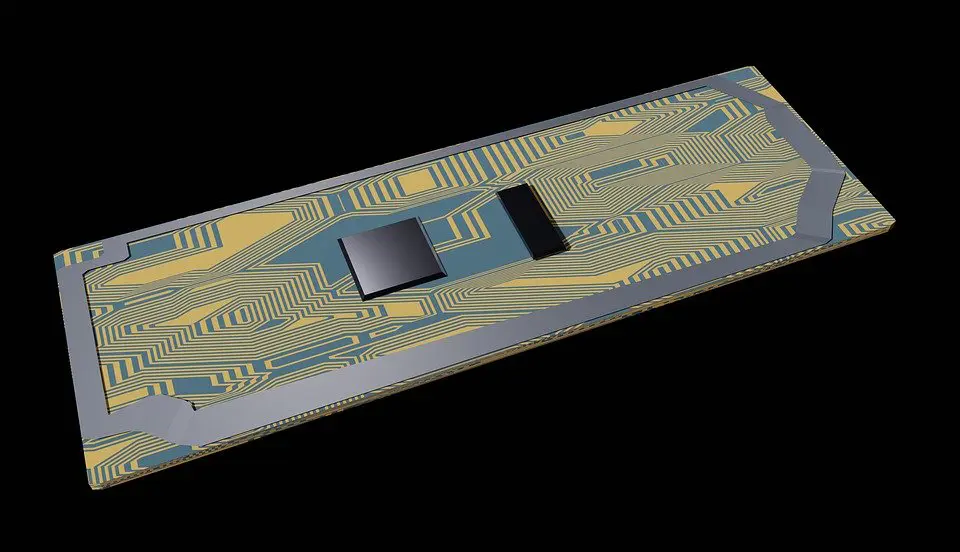
(Pixabay / IMZ36)
Fortunately, there are several ways to address negative film deformation. Here are some of the most popular techniques you can use to ensure the plating cost doesn’t increase due to deformity.
Pad deformity technique
If you have negative films with spacings and line widths above 0.30 mm and less dense graphic lines, then use the pad deformity method. This involves enlarging the holes on the test board into pads so that they overlap the deformed pieces to meet the minimum loop requirements.
Important: Once overlapping copies are created, the disc edges and lines are deformed and hazy, while the pads become elliptical. If there are strict requirements on the appearance of the PCB, use this method with caution.
Hanging technique
If the negative film experiences deformation because of the change in temperature and humidity, take it out from the sealed bag before it is copied. Now hang it in a dry place for 4 to 8 hours under working conditions and let it deform before copying (so that after copying, the chances of deformation are minimum).
Because the application of this method is limited to films affected by the environment, make sure the temperature and humidity of the hanging place are the same as that of the working place. Also, use a ventilated area to prevent the film from getting damaged because of debris or other forms of pollution.
Splicing technique
Do you have a film that’s not dense in line or the deformation of each layer of the film is inconsistent? Well then, the splicing technique may be just right for you. The method also helps to correct the power layer of the multilayer board as well as the film of the solder mask. To execute it, cut the deformed area of the film, re-splice the hole position of the hole place, and then copy. Focus on reducing the damage to the wire when spacing and try not to harm the pad.
Note: The method isn’t suitable for negatives with spacing and line width (< 0.2mm) or those with high wire density.
Change hole position technique
This technique works well when all layers of the film have the same level of the deformation, or when the film has dense wiring. You can execute it by taking the following steps:
- Compare the drilling test plate and the negative film
- Record and measure the width and length of the drilling test plate individually
- Adjust the hole according to the width and length of the deformation on the digital programmer
- Position so that the adjusted test plate is used to address the negative film deformation
The benefit of taking this approach is that it removes the need to perform the tedious job of splicing the negative film while ensuring the accuracy and integrity of the graphic. The drawback is that the correction of unevenly deformed films isn’t effective. Make sure to master the digital programmer’s operation before you attempt the change hole position technique.
Photo method
If you’re dealing with salt silver negatives, you can use the photo technique. It’s the method of choice when you find it inconvenient to re-drill the test plate and the film has the same level of deformation in the width and length directions. It’s also quite simple to execute. You just have to use the camera to zoom out or in on the deformed graphics. In most instance, the risk for film loss is very high. Also, you will need to perform extensive debugging to achieve a solid circuit pattern. Pay attention to the image to prevent it from experiencing deformation.
All of these methods can be used to treat the negative film deformation during PCB copying. However, you should take steps to prevent it from happening because prevention is better than cure. Continually replace the backup film, and make sure the humidity is 55%+/-5% RH while the temperature control is set to 22+ 2℃.