Soldering is as important in the production of a printed circuit board (PCB) as final assembly is in car manufacturing. Wave soldering is a form of soldering used to attach circuits to the boards. Before the introduction of surface mount soldering, nearly all PCBs relied on this method for the placement of electronic essentials. However, other techniques like reflow and selective soldering are more relevant to the fine features present today on PCBs for surface mount components. Still, wave soldering has a place in PCB assembly, so it’s useful to know the process and how the technique compares with modern soldering methods.
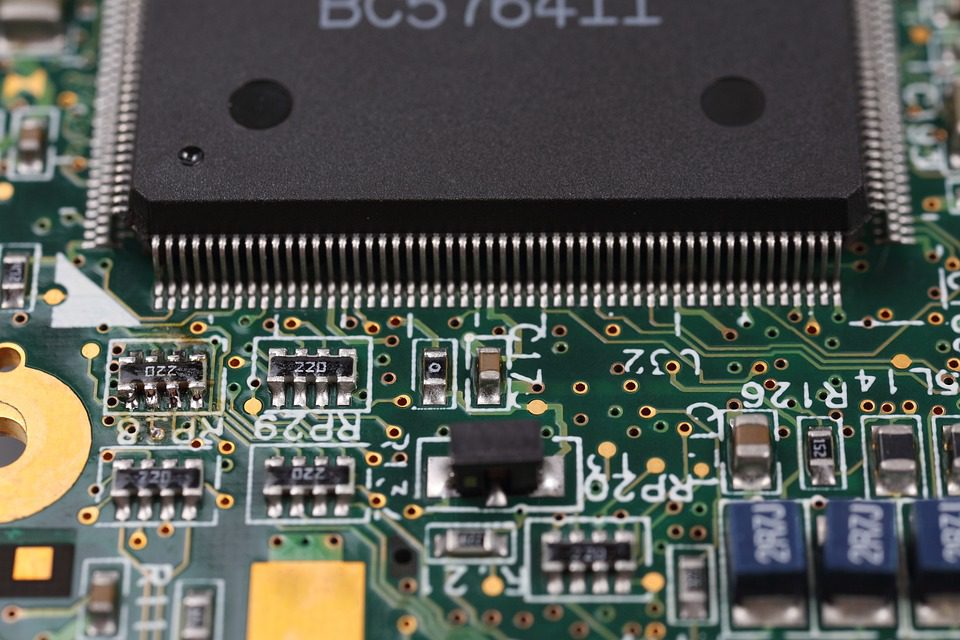
(Pixabay / nanoslavic)
The Wave Soldering Process
You will find many kinds of wave soldering machines on the market but every machine follows the same principle. Wave soldering is essentially an in-line process that requires melting the solder, cleaning it and then placing it on the board. In the first step, the solder in the machine’s tank is heated to an optimal temperature. Consistent temperature helps in heating the solder equally throughout the tank. Next, the heated solder is cleaned to remove oxides from its layers. A process called fluxing is applied to remove oxides and any other unwanted items from the solder. There are two types of fluxing: corrosive and non-corrosive.
After melting and fluxing the solder, the printed circuit board is placed on it with the help of metal clasps. This high-maintenance step helps to prevent unequal distribution of solder across the board and bumps. The last step in the wave soldering process is the final cleanup to remove any oxides that formed during PCB application. Deionized water and solvents help to clean the board of any residues.
Some Myths About Wave Soldering
Any soldering process is prone to error and wave soldering is no different. However, there are some common myths associated with wave soldering and attendant mistakes that should be cleared up.
Myth#1 Defects are caused by bad board design
Assuming that the production defects are caused by design flaws is like putting a veil on other errors. Sometimes, the soldering process is flawed and leads to errors on the board that have nothing to do with design. If there is a design flaw, the best way to fix it is by improving the process according to board type.
Myth#2 Thermal profiling is the key to good wave soldering
Thermal profiles are important, but they portray the complete picture of the process. How the boards pass through the solder and how they are fluxed are processes that matter equally. Without a healthy balance, the process might lead to disaster.
Myth#3 Touch-ups are part of production
Touch-ups are only required when the assembly line causes production failures. Touch-ups and reworks create added cost and labor for the manufacturer. If you have a high defect rate, it is time that you find out its root cause and fix the issue. Otherwise, you will be dishing out a huge sum of money on inspection, floor space, consumables and equipment.
Wave Soldering vs. Reflow Soldering
Reflow soldering is a popular method of attaching surface mount components to a PCB. You can make a solder paste and attach it to the board with the help of heat or you can use a hot air pencil. If you are wondering which of these soldering techniques is more effective, we can help clear it up for you.
Wave soldering is more complicated than reflow soldering because the timing and temperature require careful monitoring. Any mistake in monitoring will produce a flawed or useless PCB. With reflow soldering, you do not need to fret about the temperature or environment. But wave soldering is cheaper and the standard operating procedure for many PCB manufacturers.
Reflow soldering is used more in smaller applications that do not need faster and cheaper sets of PCBs. However, some companies enjoy the best of both worlds by applying wave soldering on one end of a PCB and reflow soldering on the other.
With this explained, let’s compare wave soldering with another method used in PCB soldering.
Wave Soldering vs. Selective Soldering
If neither reflow nor wave soldering are going to work out for your PCB design, you may have to accept a budget hike. This is where selective soldering saves the day when your PCB components are in danger of being destroyed in high temperatures. There are many selective soldering machines on the market based on your particular requirement. Make sure that you choose a site-specific soldering nozzle and assemble preheating for selective soldering.
The good thing about selective soldering is that the machines don’t require a lot of investment upfront. However, there’s a risk of developing solder bridging, solder balling and stringing. But wave soldering is several times more expensive than selective soldering if price is your concern.
When deciding between wave soldering, reflow, and selective soldering, your key considerations should be price, procedure and PCB design. Companies operating in the PCB industry must adopt the appropriate soldering practices to steer clear of production flaws. Wave soldering is applicable to the many PCBs still made with some larger surface mount components and traditional leaded components. These boards are typically manufactured in lower volume and installed on specialized electronics.