Several metals are used in the production of printed circuit boards (PCBs). Metal-based PCBs are also known as metal core printed circuit boards (MCPCBs) and aluminum core with standard FR4 is the most popular base material. An aluminum PCB has metal-based and copper-clad laminates that make it an excellent conductor. The structure of these PCBs is based on three distinct layers:
- The first layer is the base layer and has a metal substrate, which can be either copper or aluminum.
- The second layer is the dielectric layer, and its thickness can range from 0.003 inches to 0.006 inches.
- The third layer is the circuit layer, and the copper thickness ranges from 1 oz to 10 oz.
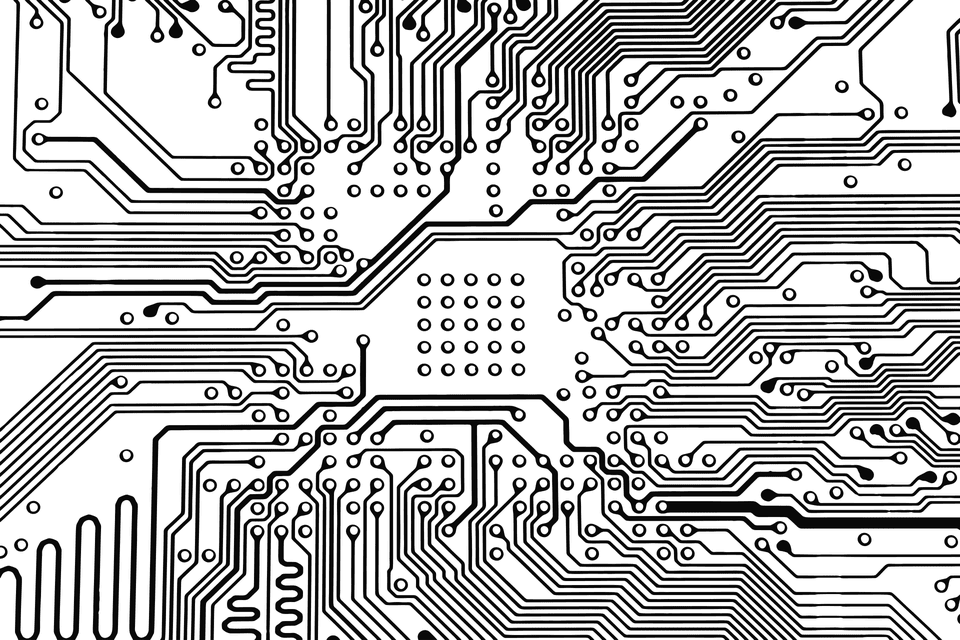
(Pixabay / GDJ)
The manufacturing of aluminum PCBs requires lamination of an electrically insulating dielectric (that’s also thermally conductive) between a copper foil and a metal base. The metal base uses the thin dielectric to draw the heat away from the circuit, whereas the copper foil is fixed into the preferred circuit pattern. That’s basically how these circuit boards are made. Today, aluminum PCBs are the MCPCBs of choice for high tolerance and high-powered applications.
Evolution of Aluminum PCBs
Printed circuit boards have been powering devices since the 1850s. These boards relied on wood and wires to create a circuit. The demand for smaller devices over time, however, called for metal-based boards that were more versatile and could be built to fit and function well in smaller sizes. Device manufacturers, especially those in the LCD industry, prefer aluminum PCBs for various reasons. Read on to learn more.
Advantages of Aluminum PCBs
- Unique and Effective
As a general rule, aluminum PCBS are more conductive than the standard thermal glass PCBs.
The dielectric layer of aluminum PCBs is one of its most distinguishing components. It dissipates the heat away from the device and protects the circuit from blowing up.
- Cheap to Manufacture
Compared to copper, brass or other metals, aluminum is more wallet-friendly. This is why it is the most suitable candidate for building any PCB. The production cost is the main concern for manufacturing companies, and aluminum helps keep costs low. Aluminum is also very durable which allows for fewer mishaps in the manufacturing process. Moreover, aluminum is readily available so you don’t have the high demand-low supply issue driving up prices.
- Highly Durable
Aluminum PCBs are known for being strong and long-lasting. This allows them to lend an extra element of sturdiness to the overall PCB design. You’re unlikely to experience many breakages when using aluminum PCBs in your design. When accidents happen during the manufacturing process, aluminum PCBs handle the pressure well and don’t break like fiberglass or ceramic-base PCBs. They also hold up well in all different climates.
- Heat Radiating
Compared to the basic printed circuit boards, aluminum dissipates a lot of heat. It’s a much more attractive choice than PCBs that are unable to scatter heat effectively. All of that makes aluminum ideal for devices that need a lot of cooling and effective heat dissipation.
- Non-toxic
Climate change and global warming have driven us to innovate solutions that do not inflict damage on our planet. Aluminum is an environmentally-friendly material for PCBs, and it can be easily recycled. In fact, out of many available PCB materials, aluminum is among the best when it comes to protecting the environment and keeping the recycle meter high.
- Lightweight
Ceramic and fiberglass bases are good choices for the PCB base in terms of function; however, they are quite heavy. Aluminum, on the other hand is very light, and the thinness of aluminum usually results in better chips.
- Versatile
Aluminum PCBs are used to make a wide range of products and devices. These products are not just limited to computers but stretch out to many fields. Amplifiers, power supplies, motor controllers, and car components are just a few examples of products created with aluminum PCBs.
A Word on Aluminum PCBs’ Downsides
Like most PCBs out there, aluminum PCBs have shortcomings. First, the manufacturing process of aluminum PCBs is not like other PCBs, so while the costs may be low over time, your initial costs may be higher. Second, aluminum cannot be used to produce double-sided PCBs like other materials out there. Lastly, aluminum PCBs may show slight issues when encountering pressure.
Conclusion
Electrical manufacturers tend to prefer aluminum PCBs for their wide range of applications, and they are frequently chosen for their efficiency over fiberglass-backed printed circuit boards. Key applications of this PCB include traffic lights, automotive lights, LEDs, consumer products, power converters, etc.
If you’re looking for a robust material that efficiently transmits heat from critical areas to minimize damage, aluminum base PCBs may be the perfect option for you. For more information on aluminum PCBs, contact us at EMS solutions. As a leading PCBA manufacturer, we can help you make the best decisions about design and materials for your PCB needs.