There are a number of challenges facing manufacturers today—particularly in the rapidly-evolving field of electronic chip production. These hurdles include:
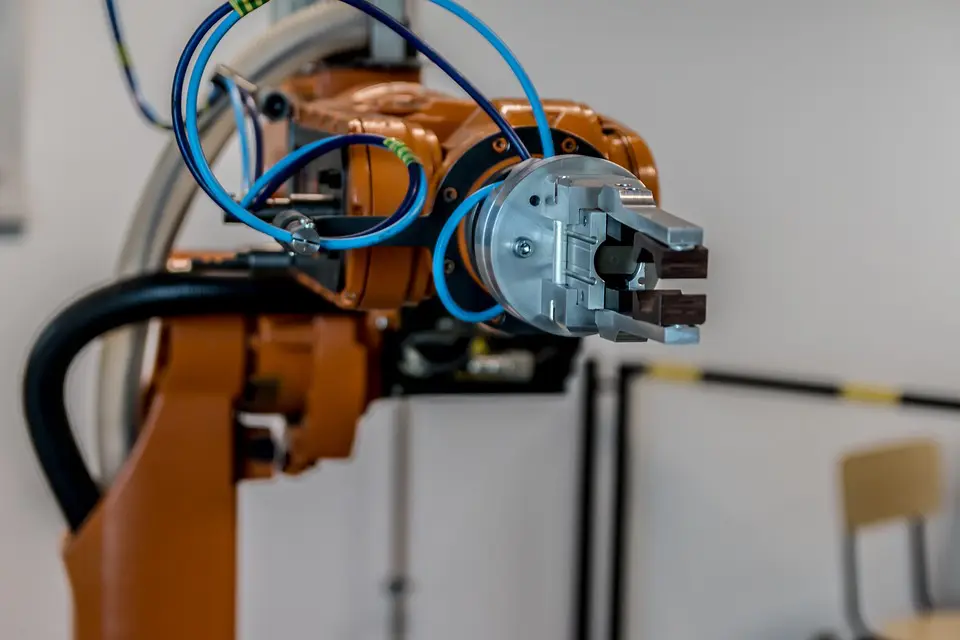
(Pixabay / jarmoluk)
- Finicky consumers. People don’t want one-size-fits-all output. They want personalized products, preferably from small, local production operations rather than behemoths with a global reach. And upping the ante, consumers want these specialized products to be reasonably priced.
- Rising production costs. It used to be that manufacturers could count on countries like China and Mexico for cheap labor and resources, but things have changed. As rates rise in overseas production sites, the manufacturing industry is feeling the burn.
- Labor shortage. The labor force, both for skilled and unskilled labor, is dwindling. Older workers who once filled manufacturing jobs are retiring, and younger workers are not interested in taking over. Immigrants have been able to fill some of these positions, but the government is tightening the screws and limiting the immigrant work force.
And aside from these new challenges, the old ones still exist. Machinery still fails, supplies still get delayed, and workers still get injured.
Thankfully, advances in artificial intelligence are helping to counter a lot of these problems. Studies have shown that three-fourths of major manufacturers are investing in technology, including artificial intelligence, and that it has lead to an 80 percent reduction in production costs, an 80 percent increase in revenue, a 75 percent decrease in errors, and a 95 percent improvement in customer service. Not bad.
Here are just a few of the ways that artificial intelligence is helping electronics chips manufacturing thrive, even in the face of current challenges.
- Adaptive, collaborative robots. It used to be that robots were the exclusive domain of mega-companies with thousands of dollars to spend on single-task robots. Smaller companies are now acquiring the more affordable “cobots,” which work in tandem with humans to learn a broad range of tasks through demonstrations and perform them in much the same way that humans can. The “cobots” work side by side with humans. Their beauty lies in their flexibility. They can be easily retrained, unlike robots of old that required hours of reprogramming at the hands of seasoned experts.
- Twinning. The old model for industrial equipment maintenance was to service it on a set schedule, regardless of its performance or condition. This resulted in a great deal of efficiency and didn’t help with real-time machinery failures. Now, equipment is outfitted with sensors that can predict problems. Companies create virtual duplicates for their machines, designing “digital twins” in the cloud. “Twinning” allows manufacturers to monitor maintenance and address issues before equipment breaks down and factory operations grind to a halt.
General Electric - Predicting production. Manufacturers have long faced the problem of over-producing or under-producing. It has historically been very tough to gauge consumer demand, but artificial intelligence is minimizing this problem. New consumer apps are helping manufacturers better predict their customers’ wants and needs. The Internet of Things, for example, uses devices to detect when people are low on certain supplies (like printer paper or laundry soap) and automatically reorder them. As technology helps manufacturers better understand consumers’ needs and purchasing patterns, there will be less waste on the production floor.
Yes, the current manufacturing climate is fraught with challenges, but the difficulties are breeding quickly-accelerating innovations that are leading to leaner, meaner manufacturing processes. Artificial intelligence and robotics, in tandem with 3-D printing and the Internet of Things, promise a bright future for electronics chip production.