The surface of PCBs is constructed of many types of substances. The most common types are FR-4 glass epoxy, a substrate made with fiberglass, and aluminum. However, a third option is available that should not be overlooked: ceramic.
Using ceramic as a base for PCBs is a relatively new concept in PCB construction. While efforts continue toward organic substrate PCBs increasing in density and precision while shrinking their sizes, ceramic boards are starting to break through as a viable contender.
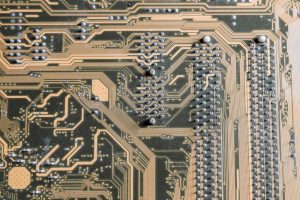
(Tima Miroshnichenko/Pexels)
What is a Ceramic PCB?
As the name implies, a ceramic PCB takes the concept of a standard substrate PCB – surface-mounted components built into a circuit on a substrate base – and replaces the organic substances with ceramics. Ceramics are chosen due to their propensity for handling high degrees of heat with minimal difficulty.
Ceramic is also a fantastic insulator against electrical currents and offers high adhesion strength. However, what makes it stand out is how it can achieve all this at a much thinner composite structure. Its structure makes it highly versatile and resistant while offering much smaller board sizes than organic substrates.
For these reasons, ceramic PCBs are ideal for use in machinery subjected to strong heat and rough outdoor environments. This makes it the number-one choice when building devices such as solar power generators and high-brightness LED lighting.
Types of Ceramic PCBs
Three main ceramics are used in constructing ceramic PCBS: Alumina, Aluminum Nitride, and Beryllium Oxide. Each of these has its benefits and detriments, so let’s look at them:
Alumina (AL2O3)
PCBs that use AL2O3 include a dielectric thermally conductive and electrically insulated material layer between the copper and aluminum layers of the substrate. It offers a greater heat dissipation rate and distribution over the board’s surface area. This makes them ideal for working in high-temperature areas.
The substrate can also be made into four PCB Assembly types: Flexible, Multilayer, Hybrid, and Through-hole. This makes it the most versatile and common ceramic board used today.
Aluminum Nitride (AIN)
Aluminum Nitride boards have the strictest manufacturing rules concerning their production. The pure substrate’s expansion coefficient matches silicon, making it great for extremely high-temperature environments. However, this efficiency is easily overcome with a thin oxide layer on its surface. These layers are enough to reduce the thermal conductivity of the substrate substantially. Therefore, manufacturers must be extremely cautious when producing boards using AIN.
When produced correctly, AIN ceramic boards are perfect for environments with extreme heat levels. It is much less common to find these boards in use. Largely this is due to the higher price per unit that AIN boards demand. The industry is making efforts to reduce this, however.
Beryllium Oxide (BeO)
Like the Alumina and Aluminum Nitride boards, Beryllium Oxide offers an excellent level of thermal conductivity. However, it comes with a caveat. While the other two operate best in high temperatures, BeO substrate boards are best utilized in environments under 300 degrees centigrade. As temperatures rise around the board, the degree of thermal conductivity drops significantly. These boards are also the least common types in use today, as Beryllium Oxide is toxic to humans.
Ceramic vs. Other PCBs
FR-4 and metal-clad PCBs are designed to resist heat, making them far less able to cope under high temperatures. The main draw of ceramic PCBs over other substrates is their higher heat dissipation. Components with ceramic boards are directly installed into the surface without isolation layers. This means that the flow of heat is much more efficient.
At higher ambient operating temperatures, epoxy glass and metal substrates are more susceptible to heat damage or distortion. They can melt, bend, twist, or collapse in extreme environments. Ceramics, by their nature, are much tougher and better equipped to withstand hotter environments.
Another bonus is that ceramic as a material is better resistant to chemical erosion. Ceramics are natural substances that will not erode when exposed to the elements or chemical acids. Boards with ceramic substrates can also be built with higher-density tracing embedded within their surfaces, providing stronger circuits.
The one area that ceramic loses out to other boards is that the higher-resistant AIN boards will cost much more to produce. Regarding extreme environmental toughness, manufacturers must resort to more expensive circuitry. In all other areas, however, ceramic PCBs are about the same price, making them a great option for PCBA EMS manufacturing.
Uses of Ceramic PCBs
Ceramic PCBs have a variety of applications. These include:
Analog/Digital PCBs
Using ceramic PCBs that function at lower temperatures is a great way to make analog and digital PCBs with superior circuit tracing. They appear in many kinds of PCs for their lightweight nature and greater resistance to crosstalk.
Solar Panels
Their tolerance for high temperatures makes them ideal for gathering energy via photovoltaic panels. Resisting the direct heat of sunlight is a must, and the ceramic plates will handle being outdoors for much longer than a standard substrate PCB.
High Power LEDs
Lighter Ceramic PCBs make them ideal for miniaturizing LED lights. This is particularly useful for high-power outdoor lighting because LEDs are notorious for producing 70% of their energy as heat.
PC Memory Modules
DDR SDRAM memory components are typically made using ceramic PCBs. The near-constant use of the circuits means they must be tough enough to withstand high voltage fluctuations. PCs are also known to produce a lot of internal heat, and it would be disastrous for the memory modules to break down due to overheating while being used.
Receiving and Transmission Modules
Radar technology was made possible largely due to ceramic PCBs. High thermal conductivity is necessary for transmission and receiving device boards, especially in multi-layer formats.
Semiconductor Coolers
Traditional PCBs cannot be reduced to a capacity capable of making semiconductor chips. As consumer electronics shrink more each year, semiconductors need to be able to shrink with them. Traditional PCBs cannot look to match the kinds of speeds necessary for smaller devices. Fortunately, ceramic PCBs can provide the superior integration and performance required to meet these demands of miniaturization.
In terms of PCB technological advancement, ceramic is definitely one for the future. Its ability to withstand higher temperatures and minimize issues such as crosstalk makes it the ideal material to focus on. Ultimately, traditional substrate PCBs cannot hold up to the potential of ceramics.