Just like a home needs a strong foundation to withstand the test of time, a printed circuit board (PCB) requires a substrate to enhance the quality and durability of the board. Picking the right substrate materials, therefore, is the first step toward making a high-quality PCB. But before we get to the components, let’s take a look at why substrate matters for PCB design.
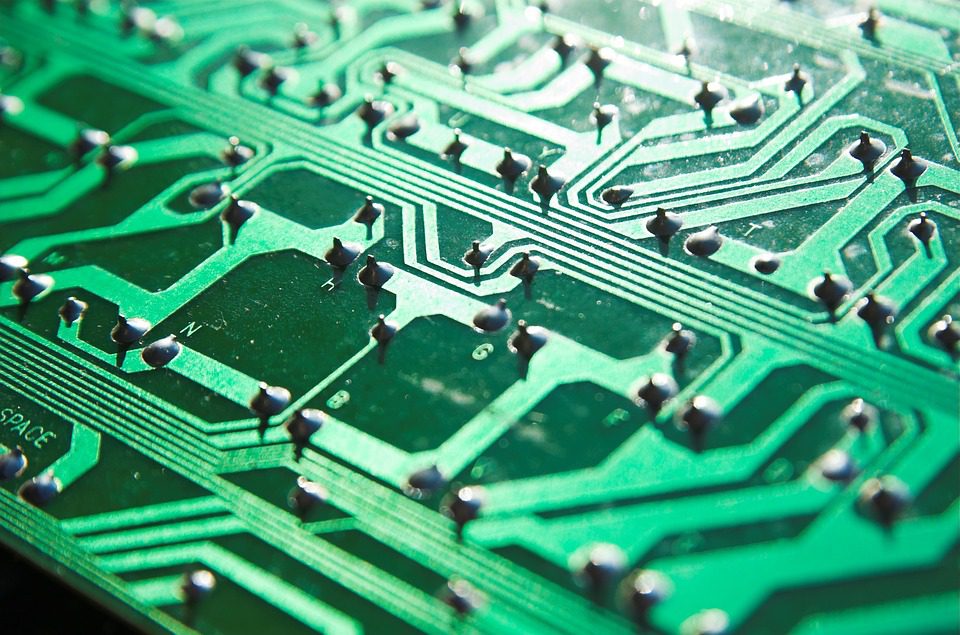
(Pixabay / axonite)
Importance of Substrate
A printed circuit board requires a canvas or platform to keep together all of its other components. This is where a substrate comes in handy. As a non-conductive dielectric material, the substrate is typically selected based upon its ability to withstand heat (Tg) and according to dielectric constant (DK). Substrate materials also act as “PCB insulation materials” that deliver electric insulation between the conductive materials.
The substrate characteristics will determine how the PCB performs in a standard setting. For instance, flexible substrates come with the ability to accommodate additional designs. A rigid substrate may add durability and strength to the PCB. Multilayer designs may have various substrates to separate the multiple layers.
Types of Substrate Materials and Best Use Cases
Most PCBs use the following four materials as their base substrate:
- Flexible: Flexible or soft substrate is specifically used for devices that will need a PCB to be bent at some point without impacting the current’s flow. The flexible substrate is available in materials like polytetrafluoroethylene and advanced polyimide substrate.
- Rigid: This is used by PCB designers who are looking to keep the PCB from twisting or taking any other form.
- Flex-rigid: Yet another choice for your PCB substrate is a mix of rigid and flexible substrate materials. A rigid board layer is attached to a flex-rigid PCB containing various layers of flexible substrates, like polyimide. This type of substrate is often the material of choice for PCBs used in military and aerospace applications as well as medical devices. Flex-rigid substrates also allow a design to be precision built.
- FR-4: This is the most popular PCB substrate available on the market. FR-4 is a “fiberglass-epoxy-laminate” that’s known for its diversity and affordability. It’s also an electrical insulator and offers greater resistance against flames than fiberglass-only PCBs.
Below are the scenarios best suited for each of these substrates:
Flexible substrate – for corrosion-resistance
One benefit to flexible substrates is that they can survive in hazardous environments. Flexible materials can make the PCB corrosion-resistant, shockproof or waterproof – that’s not something that many rigid printed circuit boards can provide. Soft materials, such as plastic form and epoxy, produce coatings around the filler (a glass weave in most instances), providing hardness and strength to the dielectric material.
The flexible base-substrate PEEK also offers a high melting point and resistance to radiation and chemicals. Also, it’s due to these flexible materials that wearables have become a reality; flexible substrate enables printed circuitry to insert into tight areas. Flexible materials also reduce weight, but they tend to be expensive for fabrication.
Rigid substrate – For strength and a strong dielectric
You may not be aware of the fact that rigid substrates have a noteworthy operating temperature. They can cross the 350ºC mark. Also, they have a strong dielectric which is of critical importance. Some of the most renowned rigid substrates are ceramic-based. Two common examples are alumina (Al2O3) and aluminum nitrate. The latter offers high thermal conductivity (i.e., high thermal strength with low expansion).
Rigid substrates are best to use in situations where you want to pursue easy maintenance and repairs. Their clearly marked components make it easy to identify the affected areas. Rigid substrates like Al2O3 also come in handy when the need for strength is critical (like in PCBs being used for medical circuits, LED boards, sensor modules, and high-frequency devices).
Flex-rigid substrate – For Easy Fixation and Lightweight PCBs
Flexible substrates associated with PTFE like RO4000 and RO3000 are often used in the PCB industry because they’re precision built and simple to machine. Another upside of their materials is that they’re lightweight. This enables them to offer space and weight savings of more than 50 percent.
Because of these advantages, flex-rigid materials allow your PCB to be lightweight. Also, they can be used for RF identification tags, automotive sensors, power amplifiers, and even cellular-based antennas.
FR-4 – For creating a complex, multi-layered design
FR’s full form is fire retardant, ensuring that the substrate complies to the UL 94 standard. This substrate is highly resistant to flames because of its richness in bromide (a halogen that’s non-reactive and popular for its flame-abating capabilities). FR-4 is available in numerous sub-grades like high TG, FR-4 Rogers, TG130, and more.
The benefit of using this substrate is that it’s affordable and highly versatile. You’ll also find variants made with sheets of “prepreg.” Prepreg itself is designed with fiberglass matting, which is impregnated via the application of epoxy resin. The high strength-to-weight ratio of RF-4 is responsible for the low-cost designs of printed circuit boards that provide optimal performance at microwave/RF frequencies. Consider using this substrate when your application requires prototyping, multiple layers, or digital circuits of low speeds. However, avoid using RF-4 in high-frequency printed circuit boards.
Conclusion
It’s a known fact that the fundamental abilities of printed circuit boards (PCBs) depend on the set up of the substrate material. Hence, to improve your PCB’s performance, you have to choose the right material to begin with.
If you need help choosing the right substrate or want to outsource the printed circuit board assembly process, contact a respected contract electronic manufacturer.