Signal distortion is a fact of life when it comes to circuitry. No matter how good the printed circuit board assembly, there are no perfect boards out there that can transmit signals to a T. All we can do is design our boards to the best of our skills with signal integrity in mind. We cannot stop signal degradation, but we can mitigate it.
Today we will look at the most common causes of degradation in printed circuit boards. This knowledge will help us understand how we can work around them and improve the quality of our boards in the future. After all, knowledge is power.
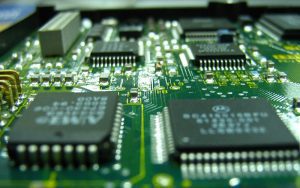
(CristianIS / pixabay)
What is Signal Integrity?
Signal Integrity (SI) measures how well a signal can pass through a board without distortion. As a signal travels from a driver to a receiver, it will encounter factors that will affect it. Crosstalk, ground bounce, jitter, and ringing will cause the signal to weaken or loop back on itself. These distortions can weaken the strength of the output of the board or cause other negative effects such as:
- Too much Electromagnetic Interference (EMI)
- Performance glitches
- Data drop
- Overheating
- Complete device failure
One thing to keep in mind is that SI is only a problem for high-frequency boards. Generally, boards that operate at lower than 50MHz are far less likely to experience issues from poor SI. If you are working with high-speed, high-frequency boards, it should always be a consideration in your designs.
Causes of Degradation in PCBs
Now, let’s look at the various potential causes of degradation in your PCB’s signal. Each one is important to consider in planning your board, though not all will be relevant. It pays to weigh up each cause against the functionality of your board when trying to predict potential issues in design.
● Crosstalk
If two or more traces are set too closely together, this can imbalance the signal. The stronger of the two (or more) pulses will overpower the weaker, causing the weaker signal to take on the characteristics of the stronger. This altered signal will no longer operate as intended. This occurs not just in traces running parallel on a board’s surface but also with traces that run parallel on different board layers. This instance is known as broadside coupling.
● Impedance Mismatch
The faster your signal needs to travel, the more you consider the signal’s impedance as it travels. If these considerations aren’t made, any drastic changes in its travel will lead to reflections. This is essentially when portions of the signal are bounced back from components towards the signal source. These reflections lessen the strength of the original signal while distorting the next waves. Impedance-controlled sensitive traces must be built along the traces of high-speed boards to filter down the signal speed without causing reflection.
● Electromagnetic Interference (EMI)
The higher the transmitted signal’s frequency, the greater the amount of electromagnetic interference it puts out. These issues are made worse when board traces are built longer or wherever the traces meet with a via. A via placed too close to an already high output of EMI can find itself turned into an antenna. The EMI can be further magnified by the return path for the signal, which is why they are typically laid on an adjacent reference plane. This helps to lessen the interference rate by spreading out the emissions more evenly.
● Ground Bounce
The state of the signal constantly changes as it transmits around a PCB. Each time it enters or exits a component, it switches from low to high. In the case of a low voltage level, the low state will bounce too high for the board. When this happens, the board misreads it as a high state rather than a low one. This is known as simultaneous switching noise or ground bounce and often leads to disruption in the operation of the circuit. Typically, ground bounce can be alleviated by including resistors to switch the output signal to help limit its flow correctly.
● Propagation Delay
Regardless of where they go, signals will always take a certain amount of time to reach their receiver. However, the more signals you have traveling through a PCB, the more likely they will arrive at the receiver at different times if not properly managed. Signals can be delayed through several means, such as trace length or the types of components they must travel through. If multiple signals all reach the receiver at different times, this can cause problems with the functionality of the board, known as signal skew. To prevent this, all traceroutes must be planned to be clocked at the correct timings.
● Via or Trace Stubs
Any part of a via or a trace that sticks out from the main body is known as a stub. If these stubs are left unchecked, they will hold a charge from the signal as it passes through. Instead, this charge will not be used in the board’s processes and can be left to build. From there, the signal needs to go somewhere. Usually, the stub will be used as an antenna, releasing EMI that can disrupt the board or others around it. Stubs also can create reflections from the signal buildup.
● Signal Attenuation
Signal attenuation – or loss of strength – can occur for many reasons in a board. A common cause is trace resistances found in the trace materials and the dielectric material dissipation factor, which must be calculated so it can be planned for in board construction. As signal frequency increases, so too will the attenuation involved, so when you are building boards for use with higher-frequency systems, you must keep this in mind. If boards can be built using a lower frequency, this will greatly help negate attenuation, but it can be mitigated by using a good low loss high-speed material for use in traces.
Conclusion
A board is only as strong as the signal that runs through it. While it might be tempting to throw as many components as you can together to form your ideal board, there are a lot of other factors that quickly build up and stand to ruin your hard work. When designing the board with your team or EMS solutions provider, run through this list and compare your features to see whether you might be at risk of signal degradation.