The reliability of solder joints in circuit boards is of utmost importance. The failure of one small solder joint can disrupt an entire PCB. Here are some of the most common reasons for solder joint failure:
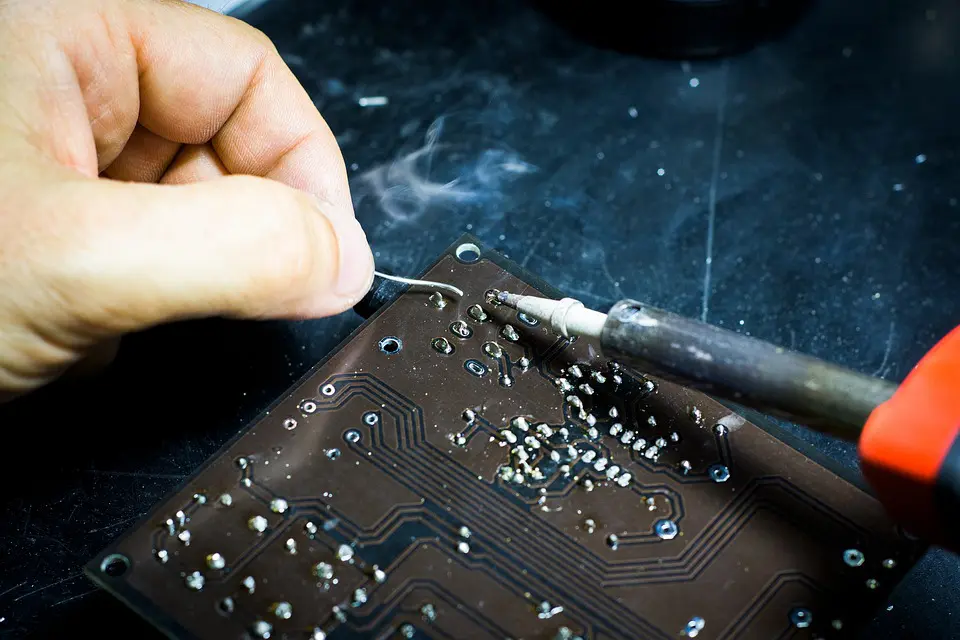
(Pixabay / www-erzetich-com)
1. Poor solder joint design
There are various types of solder joints to choose from when soldering electronic connections. The purpose and location of the solder joint should be taken into consideration when choosing the solder joint type. Applying the wrong solder joint type might cause it to fail later.
Other design features such as component mirroring, board mounting conditions and housing attachments can create constraints and board strains when executed poorly.
2. Poor-quality soldering
Soldering is a process that requires extensive knowledge and skill. Using the wrong equipment, materials or techniques (or using the correct ones improperly) may result in a bad solder joint.
3. Low-quality solder materials
Solder joints that are made with low-quality materials are not as sustainable as those made with higher-quality materials. Material defects will increase stress and might lead to fracturing.
4. Unintended stresses from polymeric materials
Materials used for potting, coating and staking have various thermal and mechanical properties. These properties can have a negative effect on solder joint reliability by creating complex loading conditions. In a dip-coated assembly, for example, the coating will pass underneath ball grid arrays (BGAs) and quad-flat no-leads (QFNs). During thermal cycling, the coating will expand and may result in the component being lifted off the board. This will add tensile stresses to the solder joints.
5. Tensile fracture
Solder joint fractures can occur as a result of short-term stress overloading. This is often observed in units that have been mishandled or misprocessed. Incidents that might lead to tensile fracture include mechanical shock that occurs when the unit is accidentally dropped or when excessive force is used while fitting the unit. In these circumstances, the solder joints are subjected to high shear stresses that may result in them being ripped away from the board.
6. Creep failure
Creep failure refers to failures caused by long-term permanent mechanical loading. This may cause solder joints to deteriorate over time and will eventually lead to failure. The potential for this type of failure is increased in higher temperatures. Creep fractures can also occur in assemblies that were not efficiently supported during soldering. When the board is then forced flat to be screwed into place, excessive stress is applied to the solder joints. This may lead to cracking.
7. Fatigue failure
The application of cyclical stresses may result in fatigue failure. This is primarily caused by temperature deviations or excursions or conflicting temperatures between the CTEs of the solder joints and the application board. This can be caused by switching devices on in warmer temperatures and off in cooler temperatures, direct sunlight exposure, or being moved to a different climate.
8. Corrosion
Tensile fractures and fatigue fractures can accelerate corrosion processes, but there are a variety of other circumstances that could lead to corrosion in solder joints:
Atmospheric or environmental corrosion
This type of corrosion occurs in solder joints that function in the air or are immersed in gases or liquids.
Galvanic corrosion
This refers to corrosion that occurs when unrelated metals that are in contact with one another are exposed to moisture.
Voltage-assisted corrosion
This refers to corrosion that is accelerated by an electric potential applied to or across the solder joint. This type of corrosion can cause byproduct material to build up between metals, resulting in a short-circuit.
9. Solder balls
This is a popular soldering defect that typically occurs with reflow or wave soldering. It shows up as a tiny sphere of solder that attaches itself to a resist, conductor, or laminate surface. The balls could be a byproduct of various factors, like unorganized solder paste printing, rough board design, or poor reflow temperature settings.
10. Inadequate wetting
Solder joints that aren’t completely wetted are weak and may fail to develop a strong connection with the board. Generally, the solder would get 100% wetting with both the pin and pad, leaving no wide spaces or gaps. Inadequate wetting usually results from the designer’s forgetfulness as they may forget to apply heat to the pin and pad. However, it could also be the result of a dirty board. The way to avoid this is to evenly heat the pin and pad and clean the PCB thoroughly.
11. Solder-starved joint
As indicated by its name, a solder-starved joint doesn’t contain enough solder to create a connection. It’s mostly because the lead was inadequately heated, causing a poor electrical connection. However, there’s a slight possibility that this joint may still work. With that said, the joint is going to eventually fail as cracks weaken the joint over time. Adding more solder and reheating the joint is the best way to prevent failure.
Solder joints do and will fail. If you don’t have the bandwidth to deal with soldering issues, you can always work with a reliable PCBA manufacturer that specializes in high-integrity solder joints. Contact us today to learn how EMS Solutions can help you avoid solder joint issues.