Conformal coating was once only for mission-critical applications like aviation. Now, small electronics and wearable gadgets use it too. Why? It safeguards their printed circuit board (PCB) against moisture, heat, and environmental contaminants.
There are many kinds of conformal coating. Each one is different and has unique properties, benefits, and characteristics. This article will help you understand how conformal coating works and help you choose the best type for your needs.
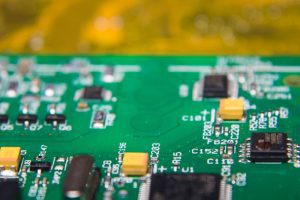
(freepik/Freepik)
What is Conformal Coating?
A conformal coating is essentially a thin layer applied on a PCB. This layer safeguards the board and its components from exposure to air and rust. Think of it as a form-fitting suit that encapsulates the board and shields critical parts. As a result, conformal coating prevents deterioration and enhances the longevity of the board.
Why is this conformal coating so important? Well, when a PCB Manufacturer first makes a circuit board, it usually functions smoothly. But over time, factors like weather and ambient conditions can rapidly degrade its performance. This is where conformal coatings come in. These coatings protect circuit boards from a host of problems, including mold growth, rust, and electrical failures. This enables the PCB to handle more power and accommodate more components.
Types of Conformal Coatings
Now, let’s look at different types of conformal coating.
Acrylic
This coating is easy to remove and quick to dry. It’s good at keeping out moisture and works well in many temperatures. People often use it for marine, consumer electronics, and some medical products.
Pros | Cons |
---|---|
Not too costly | Doesn’t resist chemicals well |
High dielectric strength | |
Easy to fix | |
Sticks well |
Polyurethane
This coating is good against water and chemicals. It also works well in different temperatures. But it can be hard to fix if something goes wrong. It’s often used in aerospace, cars, and medical applications.
Pros | Cons |
Low cost | Hard to resist chemicals |
Works well in many temperatures |
Silicone
This coating works well in a lot of temperatures and humid conditions. It’s good against chemicals, moisture, and salt spray. But it can be costly and hard to fix. It’s often used in aviation, consumer electronics, and energy.
Pros | Cons |
Works well in many temperatures and humid conditions | High cost |
Very flexible | Hard to fix |
Hybrid
These are mixed chemistries, used for specific needs. Electrolube’s SCC3 range is one example. They have a wide temperature range, are easy to apply, and have high chemical resistance. They offer good protection in various environments.
Pros | Cons |
Suitable in many temperatures | May require special removers for rework |
Easy to apply |
UV Cure
These are another type of hybrid coating. They cure quickly under UV light, which is good for high-speed applications. They offer excellent chemical resistance but can be hard to remove and may struggle with thermal changes.
Pros | Cons |
Very fast processing times | Can be hard to remove |
Good protection in various environments | Less flexibility during thermal changes |
2K Coatings
These coatings combine the best of encapsulation resins and conformal coating. They offer high performance and excellent moisture protection. They can be applied thicker than single-part coatings.
Pros | Cons |
High performance | Can be hard to remove |
Excellent moisture protection |
Ways to Apply Conformal Coating
- Manual spraying: This is good if you don’t have a lot of boards or big machines. You use a spray can or spray gun. You might need to cover some parts. The person spraying decides how good it looks.
- Automated spraying: This uses a machine. It moves the boards under a spray head.
- Dipping: This is another good way if you have a lot of boards. You have to cover parts first. Then you dip the board in the coating. You dip both sides. The way you dip changes how the coating looks.
- Selective coating: This uses a smart machine. It can put the coating only where you want it. You don’t have to cover parts you don’t want sprayed. This is good if you have a lot of boards.
- Brushing: This is used mostly for fixing. You put the coating on parts of the board with a brush. It doesn’t cost a lot. But it takes time and it’s not the same every time. This is good if you don’t have a lot of boards.
Important Considerations for Conformal Coating
First, think about how hot your board gets. Some coatings can’t handle too much heat. If your board gets very hot, you may need to change how it cools down or choose a different coating. Some coatings keep in heat, others let it out. You may need to change where parts go or how you cool the board.
Also, consider where your board will be used. Water, tiny bits of dirt, chemicals, and more can hurt your board. The coating can help, but it needs to be the right kind. Also, the coating needs to move with your board. If it’s too stiff, it can hurt parts of the board. You may need to change your board’s design to fix this.
There are many ways to put on the coating. You can dip the board, spray it, brush it, or use vapor. What’s best depends on your board’s size, the parts, how many you have, and your budget. For a few boards, it’s usually best to brush or spray it on. Different board materials need different coatings. Cleaning the board before putting on the coating can help it stick.
Lastly, consider the thickness of the coating. A thin coating might not protect enough, but a thick one might cause problems. Too much change in temperature can make the coating stress the board and break parts. This depends on the coating. Usually, it should be between 25 to 250 micrometers thick.
Conformal coating is a fundamental process in printed circuit board assembly (PCBA) manufacturing. It significantly boosts the durability and reliability of the PCB, offering protection against challenging environments, fluctuating temperatures, and potential contaminants.
With multiple industries pushing for smaller, yet more powerful devices, conformal coatings allow for high-voltage operations without needing extra components. A reliable PCBA manufacturer will prioritize and optimize their conformal coating processes to ensure the long-lasting performance of their clients’ products.