Building the average Printed Circuit Board (PCB) is complicated in the best of times. Ensuring an ideal mix of parts, materials, and placements is a skill that requires focus and knowledge. All too often, mistakes get made along the way and missed until it is too late. Parts that don’t fit the design, boards too small to hold everything, and traces too close together will lead to total overhauls in design.
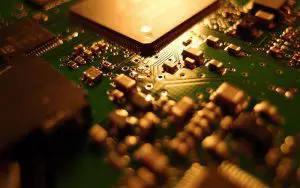
(TBIT / pixabay)
It is for these reasons that Design for Manufacturing was devised. This is a steady and reliable way to help prevent and predict any possible issues that can set a project back.
Today, we’re going to explore DFM, what it is, and why you should employ it in all your future PCB production plans.
What is Design for Manufacturing?
The core concept of Design for Manufacturing (DFM) bridges the gap between the designing and manufacturing teams responsible for building PCBs. Often, once a design is laid out and passed on for building, it is left entirely in the hands of the manufacturer. This means that it is up to the manufacturers when problems arise to figure them out.
As many companies have discovered, this is not an ideal solution. Manufacturers are not always the ideal people to solve these issues, and the process of sending a half-built board to a designer is largely impractical.
This is how DFM changes the game. By utilizing a team of specialists and software, you can design new boards according to several factors. This design is then checked over and compared to many criteria that may eventually appear as an issue down the line, giving the designers a chance to alter the design before it goes into manufacture. With DFM, problems are rectified during the designing phase.
What’s more, DFM software can be programmed to detect potential PCB failures that otherwise won’t be discovered until after the board is assembled. Some errors that can be found with fabrication analysis include:
- Acid Traps
- Insufficient Annular Ring
- Slivers
- Starved Thermals
In essence, DFM software can help you detect any issues that typical CAD systems cannot account for ahead of the manufacturing stage.
What Are the Benefits of DFM?
Ensuring your new boards go through DFM offers several compelling benefits. From PCB assembly to sale, you can expect it to help you in the following ways:
● Fewer Mistakes
With everything planned out far in advance and all contingencies accounted for, you’re less likely to find your project stopped by unexpected issues. Problems with board size, component placement, and material usage are considered during planning, meaning you have the final design in place before you begin building it.
● Design Improvements
DFM doesn’t just apply to new board designs. If you already have a library of designs you have used before, you can run them through the DFM process to find improvements and changes that can make them useable.
● Better Component Selections
Running your designs through these checks during the designing stage allows you to see where you can use better components. If you have been choosing smaller or cheaper parts to fit a tighter design better, DFM may highlight ways to use the parts you want without sacrificing space or other parts.
● Saves Both Time and Money
Avoiding mistakes while designing means fewer mistakes while building. When your manufacturers know they are using the correct parts the first time, they can build much more efficiently. This means you are far less likely to lose time to revising or scrapping failed designs and streamlines the process of building completed plans.
It should also be noted: when you know exactly what parts you need and where to use them, this will also allow you to find ways to save on parts. If you can find alternative components or materials that still fit your specifications, it will reduce your manufacturing costs even further.
The Factors for Design for Manufacturing
When working with a DFM, your production plan is assembled following a simple set of steps. The steps you should consider are:
● Your Manufacturing Plan
What is your board going to be used for? How many boards do you need to produce? What components will you require?
These questions will lay the foundation for your DFM. Plan with every detail and ensure that you have every aspect of the board in mind as you go forward. Knowing what you need and how much of it will save you from the problems of under-ordering components and give you a good idea of your production schedule.
● The PCB Design
When you know exactly what you need, you can plan how the board can be assembled. If your board needs to meet certain requirements, such as size, shape, or components, this is the best time to get everything in order.
Using DFM software can help you determine if certain component layouts will be problematic and allow you to consider alternative orientations. Remember to keep your electronic manufacturing services partner in the loop with this stage to ensure that they can meet your requirements during assembly. They may also have suggestions to help streamline the process.
● The Board’s Environment for Usage
Once you have everything you need in place with your design, it will be time to examine the setup with its eventual environment in mind. Where the board will be installed is a big factor in ensuring that it remains functional during use. If you find that certain parts you have chosen are susceptible to heat damage and the board will be used in high-temperature locations, then now is the time to revisit the materials and components.
● Quality Testing and Compliance
With the design, components, and materials finalized, it is time to determine whether the board will meet safety and quality standards. This can be done in-house or through a certified testing facility at this stage. Either way, knowing ahead of time that your design will pass will save time and money, as any changes can happen before production begins.
Conclusion
Today, boards are used in so many different products and environments that they must always meet high safety and compatibility standards. This means that an effective and streamlined production process is vital for bringing this technology to life. Design for Manufacturing is a fantastic advancement in production that can help you and your company flourish in these busy times.
Video
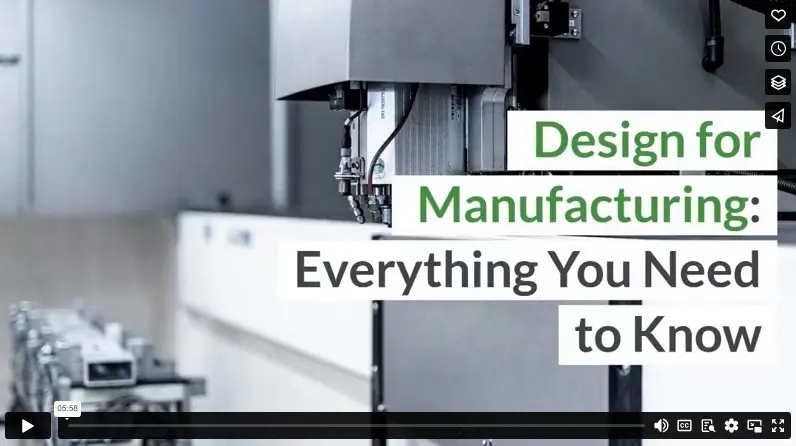