Constructing a printed circuit board (PCB) requires many parts and techniques. The most vital of these parts is arguably solder – a metal alloy used to connect components and wires to create a functional circuit. Thanks to its low melting point and high conductivity, solder serves a dual purpose; to hold each component in place and integrate them into the circuit itself.
Like any Electronic Manufacturing Services (EMS) assembly process, mistakes and errors can occur when soldering. Desoldering pumps exist to fix these errors.
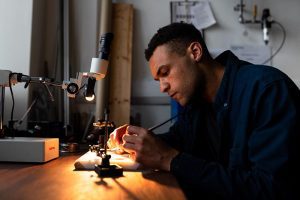
(ThisisEngineering RAEng / unsplash)
What is a Desoldering Pump?
A desoldering pump is a device used to remove solder from connection points. Typically designed to look the same as a regular soldering gun, a desoldering pump is a thin, hand-held device with a trigger used to activate it at one end and a head that consists of either a plunger or a bulb-shaped object on the other end.
In the event of an incorrectly placed or insufficiently connected component, you can use a desoldering pump to suck up and remove the solder. You can do this all the way down to the microscopic scale. The pen-shaped design of the pump allows a PCB assembler to accurately isolate and remove the solder without affecting any of the surrounding board surface or components.
As the solder melts at a lower temperature than any components used in EMS PCB assembly, it can be safely melted and sucked away without causing damage to the board or its components.
Why Use a Desoldering pump?
Desoldering pumps have a particular purpose: to remove components. In the past, if you found an error during production, the manufacturer would have to scrap the current design. But with a desoldering pump, you can remove the problematic components without hassle.
If a part is found faulty after removal, you can safely dispose of it. The parts left undamaged after desoldering can go back into production.
Desoldering also allows a designer to test out a circuit layout without committing to it. They can remove and replace parts with zero damage to the board, allowing a more comprehensive range of design options to be tested in a real-world environment.
Benefits of a Desoldering pump
Desoldering is a great way to quickly and efficiently troubleshoot a PCB mid-construction. The pump’s size and shape are designed to be easily manageable. It can also work in almost any position or location across a board. Some of the benefits of using a desoldering pump include:
- Correcting issues and easing the process of troubleshooting connection and component errors during production. When an error is detected, it will be in a single component, which can be easily removed, replaced, or reoriented thanks to desoldering.
- A desoldering pump’s design includes a built-in heat gun for melting solder. At the same time, the pump extracts the melted solder and stores it away. This design choice keeps the tool shape and size small, giving the user complete control and eliminating the need for secondary tools.
- The point of the desolder pump can shrink down to microscopic sizes. This makes it easy to work with boards of all shapes and sizes.
- Desoldering components is much more time-efficient than removing a whole board’s soldering. You can remove individual components without damaging the overall board or circuit. This eliminates the need for replacing expensive or limited parts, saves money, and reduces production waste.
- You can redesign components removed during the production process to install future prints in the same way, preventing further errors.
- Removed components will remain undamaged and reusable, meaning you’ll waste fewer parts during the production cycle, save money and lessen waste.
Disadvantages of a Desoldering pump
Fortunately, the only downside to using a desoldering pump is that the bulb-head design is far less adaptable. The larger structure of the head makes it less viable for use with smaller boards and components. You’ll need to access smaller areas with a tinier plunger end.
How to Use a Desoldering pump
Desoldering a component is relatively easy, and anyone with the correct tools can do it. When you discover an error, take the following steps:
- Secure the PCB in place using a board holder. It must be tightly held, as you will need the board to be still during the desoldering process. However, it must not be too tight, as excess pressure will cause damage to the board’s substrate.
- Heat the Desoldering pump’s element. You can do this using the simple switch on the device.
- Locate the component that you need to remove. Gently press the end of the heating element to each of the solder pads in turn. For a plunger-style pump, the tip closes over the top of the pad around the solder. With the bulb design, the pump presses down on the solder for a bulb-style pump.
- The heat generated by the element melts the solder back into a liquid form. The pump is then released, and the sucker is activated using the side release button, drawing the liquefied solder out of the pad.
- The melted solder will be stored in the pump’s cylinder. You can remove this after use, but larger jobs require multiple cylinders to hold all the solder.
- After removing the solder, clear the component from the board to either be tested or disposed of as necessary.
- Clean out the Desoldering pump by dismantling the pump cylinder and tapping the cooling solder out. You must then swab out the cylinder and piston to remove any excess solder to prevent damage.
- You can then reassemble the pump and prepare it for future use.
Desoldering represents an essential part of PCB assembly. It offers many great benefits for designers to test and alter their designs without causing any damage to the currently laid components. With the development of much smaller desoldering pumps, component removal has become simple and easy, with only a single tool needed. When errors arise during production, consider desoldering before scrapping the current project during EMS PCB assembly.
Video
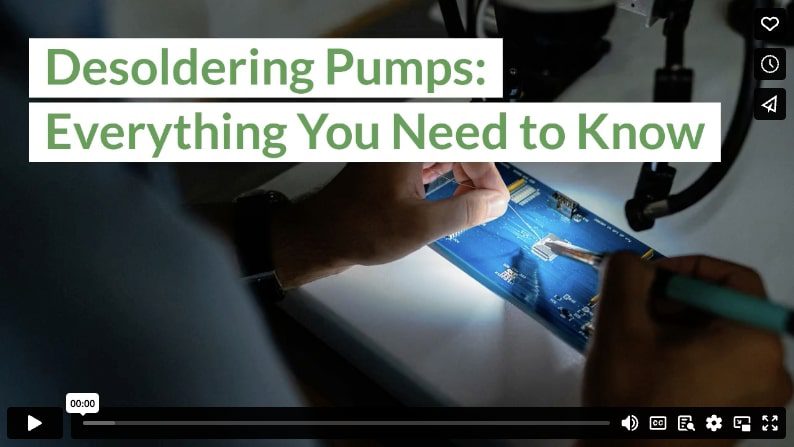