Electromagnetic interference or EMI occurs when an electrical circuit experiences a disruption in performance due to induction, electrostatic coupling, or conduction on a PCB. Essentially, electromagnetic interference is caused by an external source and may include natural phenomena as well, like lightning or solar flares. EMI can easily cause WiFi signal disruption in household areas as well as issues in electronic items in commercial buildings. When this happens, EMI can ruin hardware and cause data loss. EMI is also known as RFI (Radio Frequency Interference).
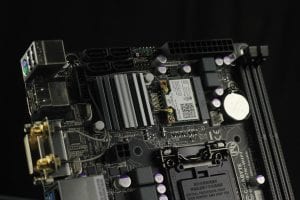
(Pixabay / FuzzyMannerz)
EMI Shielding to the Rescue
To safeguard from the incoming EMI and/to prevent a stronger signal from going out and interfering with nearby electronics, manufacturers use the technique of EMI shielding. This is where they leverage stainless steel fiber, nickel-coated fiber, or carbon fiber in a “thermoplastic matrix” to achieve the desired shielding. EMI shielding can cover active components, IC chips, and some other elements of PCBs. Plus, the compounds can be used in various industries, including energy, healthcare, electronics, and the automotive market.
Keeping in mind that EMI can cause a device to fail or underperform, some safeguarding principles must be followed to avoid this disturbance. The best solution is to create a shield that can save signal disruption and ensure smooth operation. Even if interference is present, the device must be able to perform with this shield’s assistance.
An EMI shielding gasket is a specific solution that caters to this particular need. This gasket consists of metallic or plastic parts (often a conductive silicone cover) which fit into housings or a compartment. When fixed, these items negate all sorts of interference. In commercial environments, window films are a popular option to minimize EMI as much as possible.
Importance of EMI Shielding
In product development, a company’s product is good only if it performs well in the hands of a customer. If the product expires after a few uses, this does not reflect well on the company. Fortunately, EMI shielding allows product developers to prevent their items from getting affected by EMI. Faster electronics means more productivity and happier customers. Failure to deal with the losses of EMI means unhappy customers and loss of potential profit.
EMI can also cause trouble in environments where workers are dealing with sensitive or real-time data. Any interference can lead to a big issue, such as jeopardizing the safety of mediums these people are working on. Thus, EMI is something you must not overlook at any cost. On one hand, stakeholders use gaskets to protect devices, and on the other, they can install items like window films to protect commercial spaces on a broader level.
Material Used for EMI Shielding
There are several kinds of materials available for EMI shielding. The exact materials and techniques are determined after considering the electronic device to be manufactured.
Some examples are:
- A metallic film or foil to protect equipment wires. The coaxial cable has a shield built within the wires and can be found wrapped around under the outermost insulation layer. In other cases, the user could wrap the wire bundle in a foil or a ready-made braid. The end-connections of these wires also require coverage to protect the wiring from all ends.
- When it comes to shielding on PCBs (also known as board-level shielding or BLS), there’s usually a ground plate built into the PCB. Plus, a metal box (also called a shielding can) is placed over every transmitting element on the PCB. Then, all PCB components are encased in a Faraday cage.
- In devices like speakers, an inner casing (metallic) successfully deflects all EMI hitting from nearby devices like microwaves or TVs.
- In spaces where magnetic fields are below the 100kHz range, conductive paint and magnetic materials are ideal.
- Other materials for EMI shielding include sheet metal, metal foam plastics, and mesh-metals.
Note: Customization is required because of the amount of signal blocking required per product material, size, volume, and thickness. Each of these factors plays an important part in the shielding process.
As per the frequency, the shield does not need to be a solid screen and can have a mesh-like look or holes. Therefore, it is essential to see which part of a device needs protection from the frequency spectrum.
PCB Shielding with Metal Cases
Stray electric fields in a PCB can be dealt with by using a metal enclosure. The user simply needs to place the cover on sensitive components to protect them. When various components are guarded with a metal casing on a PCB, there’s less disruption inside and between the components. It’s critical that the shielding provides a low impedance path to external sources to reach the ground point so they can quickly dissipate the stray current.
PCB Shielding with Guard Traces
In an analog trace, signals can induce a current in the trace nearby, a process called crosstalk. Crosstalk is a common issue in parallel traces. Proper spacing is advised as the best design rule to prevent crosstalk. The problem gets even worse in analog traces when the frequencies go higher. As the signals in parallel traces run in the same direction, it creates a lot of noise and negatively affects the signals’ quality.
It’s also worth mentioning that not all PCs have enough space to run two parallel lines with adequate distance. One convenient method of preventing noise between two traces is to run them as differential pairs. If that’s not possible, a grounded trace or guard trace can be put between the two lines. Guard trace helps to lower the signal noise, or crosstalk, to a great degree.
PCB Shielding with Fences
In RF circuits with an antenna, the construction should already separate the ground plane and antenna, so both items do not overlap. Another method to reduce disruption between the ground plane and antenna is by using a via fence. Holes lined up on the border between the antenna and ground plane separate the plane and the antenna into separate blocks.
The usage of via fences is not limited to antennas. Via fences are one secure method that commonly provides effective shielding for stripline transmission as well as circuits. While these are effective to use in PCBs, via fences eat up a lot of space on the board and are not as good as a metal can.
EMC Certification
An EMC (electromagnetic compatibility) certification is required for any product that hits the market. This means that any product with a PCB must be EMC tested first to ensure that it will not affect other devices when in function. Moreover, the product should operate well enough under testing around other systems.
A common problem in product development is that EMC testing is applied at the last level. At this time, electromagnetic designs are well set and frozen. The engineers will have little or no space or time to make the necessary amends. In this scenario, you will need to cap the components without affecting designs, and EMC shielding is the answer.
All circuits emit radiation and receive stray signals. Achieving the certifications that can lessen this noise is the key to a high-performing product. EMI shielding is, therefore, a fundamental part of the product development cycle because it fights all said issues. Electronic device manufacturers without the materials required for EMI shielding can contact an electronic manufacturing services company to do it for their products.