Many things go into constructing a printed circuit board (PCB). Without components, copper traces, or heat sinks, we could not build or run a circuit board how we want within a device. But regardless of what exists on a board, one thing it can’t do without is the core. Whether multilayered or single-layered, large or small, the board will not make a rigid or usable base without a core.
Two types of material act as a base for a board: core and prepreg. Today we will take a closer look at a core or prepreg, what makes them similar, and what makes them different.
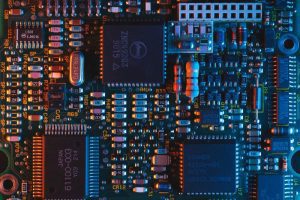
(Umberto/Unsplash)
Core and Prepreg at a Glance
You will often hear core and prepreg discussed together, giving the impression that they are the same. This is not strictly true. While they both have vital purposes that make them similar, they are inherently different and have separate uses.
Put simply, prepreg and core are the insulating materials upon which a circuit is built. You can also label them as components that make up the base layers of a PCB. Most boards contain prepreg and core, each serving a different purpose.
Prepreg in PCBs
Prepreg’s main purpose in PCB construction is to provide insulation. It is a building material layered between a board’s copper surface and inner Core. Its purpose is as a dielectric material between these layers that prevents current from passing between them. Due to how it is bonded between these layers, it is often called a binding material and used to help strengthen a board. A client can customize a prepreg layer in many ways, including to increase insulation or to be made conductive by including catalytic substances and additives.
Prepreg is easy to apply to core material as it is composed of a fiberglass fabric coated with a resin reserve. Its glass strands are knitted in such a way as to form a glass tissue, which is then allowed to dry partially. In this state, it is pasted over the core material and gains an adhesive quality. Before adhesion, designers track the volume friction of this material, as this will determine the final qualities of the prepreg layer. This is when manufacturers alter it to match the specifications of the customer.
Fortunately, this adaptability means various prepreg materials are available to meet almost any need. Its application is also simple and easy to master, making it a great additional skill. What’s more, using a prepreg layer helps reduce the weight of a board, thus facilitating miniaturization in board design.
Core in PCBs
A core is used in the construction of single-sided and double-sided PCBs. The core material is the foundation upon which we construct the whole board. It is a solid plate you can coat on one or both sides with copper (and Prepreg as insulation).
A core consists of an FR-4 (Flame Retardant) mix of elements, including titanium epoxy laminates and traces of copper. It is woven with fiberglass cloth to create a fire-resistant, solid surface. It is then coated on either side with copper to form the base material of a PCB.
On its own, it creates a firm and malleable surface on which components are assembled. With a prepreg layer, its strength greatly increases without too much extra weight. Most electronic manufacturing services combine the two to create multilayer PCBs.
Prepreg and Core: What Are the Differences and Similarities?
In essence, the prepreg and core layers are the same. They both have the same basic elements to form a rigid board and work together to strengthen what already exists. For this reason, many people confuse the two. However, the biggest difference between them can be summed up simply:
The core is a central layer of a PCB that is later laminated using prepreg.
What makes the two notably different is the way PCBs implement them. As a laminating layer, prepreg can provide a greater source of insulation to the layers of a board. It will prevent the heat gathered by the inner and outer layers of a PCB from interfering with those around it.
Due to its adhesive properties, many manufacturing companies will use prepreg as a form of adhesive to secure solid layers of core and copper together. When applied, the heat passed through the core material allows the prepreg to seal between the layers and cure over time. This gradually gives the prepreg the properties of a core.
The other difference between core and prepreg is how its creation affects the final result. A core is created and cured as a single solid mass with rigid properties and a single purpose. So long as it is hard, it will make a solid foundation for the PCB assembly. On the other hand, prepreg can be altered at various points during production to change the overall properties it holds.
Three aspects of prepreg’s composition affect the degree of dielectric constants:
- The glass fiber weave
- The type of resin
- The content level of resin
Unfortunately, it is difficult to determine the exact measurements needed to match the impedance between the prepreg and the core. This means that some mixes of prepreg will be incompatible with the core. This can be down to the prepreg not offering enough or offering too much resistance for the board, which you cannot predict accurately.
When designing a PCB with prepreg in mind, manufacturers must consider the eventual certainty of voltage creep. While you can apply additional prepreg layers to increase a board’s thickness, an increase or loss of resistance will accompany it. In some rare cases, avoiding prepreg or completely redesigning the board’s intended conductivity may be preferable.
Prepreg and core are both made of the same substances at their center. However, the two offer enough differences and complex dynamics that designers must consider the pairing before application. What matters most is that prepreg complements the core, providing rigidity, insulation, and the ability to create multilayer boards.
Infographic
Core and prepreg are essential in creating any printed circuit board. Even though they both have a primary purpose, their roles vary and should be utilized suitably for the best outcomes. This infographic offers an up-close exploration of core and prepreg to understand how these elements are similar but uniquely distinct.
Video
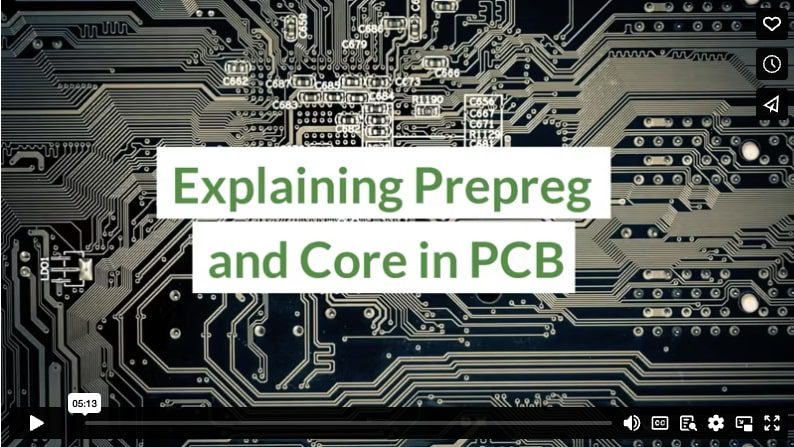