Flex board designs are not just a luxury, but a requirement for several applications. Multiple sectors, including medicine and aerospace, utilize flex PCBs to accommodate elaborately or tightly shaped form factors. However, before choosing a particular class type from the several available flex PCB boards, consider empowering yourself with a better understanding of their manufacturing process.
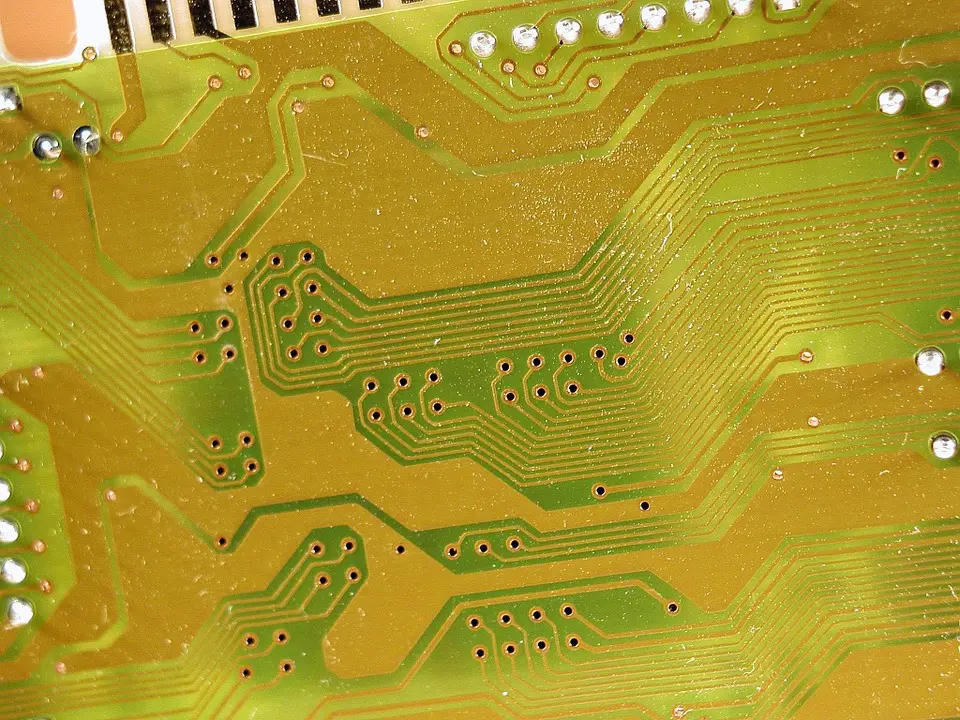
(Pixabay / PublicDomainImages)
Using flex manufacturing allows for:
• More compact boards:
The process’s bendability offers a wide array of mounting probabilities, along with the possibility to condense the board surface.
• Reduced complexity:
Manufacturing flexible PCBs often removes the need for additional wires, connectors, and even other printed circuit boards. This will usually minimize the complications of PCB assembly, as well as the required quantity and incurred expense of sourcing the main components.
• Greater tolerance of extreme temperatures:
Flex PCBs come with the enhanced capability to function in extreme temperatures, which means they can provide improved resistance to radiation problems and leverage more connector and component types. The polymer or polyimide material variation of the board allows it to withstand extreme temperatures without adversely impacting the board’s performance.
What Goes into The Flex Board Manufacturing Process?
Depending on the need of the application, an organization can get several types of flex boards manufactured. Chief among them are rigid-flex and flex PCBs.
The first of these is a combination of flex and rigid, providing the possibility of both designs. For instance, the standard rigid-flex board would be a chain of rigid PCBs connected through flex PCBs. By incorporating the flexible parts with rigid areas, manufacturers can significantly enhance their circuit’s outlook.
Flex PCBs, on the other hand, refer to the design where the whole board is flexible. They come with unique capabilities like vibration resistance, repeatability, and flexibility. The major benefit of using these boards is that flex PCBs allow the manufacturer to imagine 3-D configurations.
Whether you go with a flex PCB or a rigid-flex design, the manufacturing process for the board part is almost the same as for the board portion of rigid PCBs. The critical distinctions between the two are discussed below.
Flex circuit coverlay
Coverlays perform the same function as the solder masks do for rigid printed circuit boards. Simply put, it is the lamination that shields the board from various contaminations, just like a soldering mask protects a rigid PCB. However, coverlays are generally flexible and thin, with some varieties having a 0.005-inch thickness.
Fixture use
For ensuring the “planarity” of SMDs (surface mount devices), you may have to buy fixtures to maintain the shape of the board until the parts are completely attached. There’s a risk that the components may come off if the board bends. Hence, the vulnerable components may raise the need for additional adhesives. The investment in adhesives and fixtures is offset by the fact that flex boards are ideal for various types of devices, including sensors, handheld consumer electronics, implants and medical devices where space is limited.
Material choice
Another vital consideration for flex PCBs is their composition materials. When it comes to flex boards, polyester and polyimide films featuring “copper clad” laminates are typically utilized. The absence of standard material provides manufacturers with a variety of material choices. A rule of thumb is to use the following parameters and base your choice on the application of the board: volume resistance, loss angle tangent, dielectric strength, limit elongation, size change after etching, limit tension, and relative dielectric constant. Moreover, the board should meet certain performance and qualification standards.
Flex Board Usage
Flex boards are commonly used in places where it’s challenging to fit any other type of circuit board. You can consider them to be a “hybrid” of round wires and the standard PCB while showcasing their separate advantages. Those who use flex boards can benefit from the retention of the density, repeatability and precision of PCBs, while still having the ability to package geometry at their will.
Another use case of flex PCBs involves the replacement of wiring joints, which enables flex circuits to supplant multiple hardboards, cables, and connectors in a single operation. The result is a faster assembly process, which eliminates the requirement to wrap wires in bundles or color-code them. Installation overheads go down, and volume levels go up, while odds of rejection during in-service and assembly failures dip.
Industrial Applications of Flex Boards
Flex boards have come a long way in the past few years, enabling them to be applied in a variety of industries. Discussed below are a few of their sector-specific use cases.
Automotive
The majority of the electronic hardware used in the automobile industry utilizes flex PCBs. Examples of applications include airbag controllers, engine management units, anti-lock braking systems and more. Their circuits can also be used to sync up with additional electronics without the need to integrate bulky connectors and cable ties. Moreover, flex PCBs can be constructed to fit into smaller spaces with inconsistent shapes, which provides engineers with greater flexibility.
Pharmaceutical
Flex boards are also critical for medical and pharmaceutical hardware where circuits need to survive extreme temperatures. Swallowable pill cameras, for instance, utilize a durable and non-toxic flex circuit for optimal function. Newer circuits are even more flexible than the typical PCBs, enabling them to travel naturally without undergoing any damage.
Smartphones
Smartphone hardware is lightweight and portable, so a thin-layer PCB is required to sync up and connect all the main components. Standard circuit boards aren’t flexible enough to fit inside those hardware components. Because mobile handsets can be carried around with ease, the hardware inside should survive various types of environments. That’s where flex boards excel.
Computer electronics
Many computer electronic components also rely on flex PCBs to function. Hard drives, for instance, have to be flexible because of the need to work at a high speed to write data. They get hot and have to bear high temperatures frequently. As a result, hard drive manufacturers often use flexible PCBs to ensure the hardware lasts.
To conclude, flex boards enhance the potential applications of your PCB design, especially for devices where bendable and smaller circuits are required. Educating yourself on their manufacturing process will allow you to utilize their advantages to the maximum.