Good Manufacturing Practices, or GMP, ensure that cable assemblies are made precisely every time. This system uses strict procedures, rules, and documentation to maintain quality at every step. From selecting materials to final inspections, GMP helps prevent mistakes and keeps the process efficient.
In this article, we’ll look closely at how GMP streamlines the cable assembly process. We’ll discuss specific ways to implement GMP and show how following these practices ensures product quality and customer satisfaction.
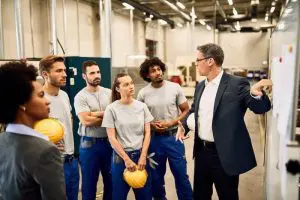
(Drazen Zigic/freepik)
The Five Key Components of Good Manufacturing Practice
GMP is crucial for making sure everything in manufacturing stays consistent and safe. Let’s go through the five key parts of GMP that help keep everything up to standard from start to finish.
1. People
Everyone has to follow the rules and know the process well. Regular GMP training helps everyone understand their job clearly. By setting up a schedule for consistent training and doing regular check-ins with teams and individuals, you can help your people work better and smarter.
2. Products
Before products go out to customers, they need thorough testing to make sure they’re up to par. Manufacturers should check that all the materials used meet quality standards at every step. Everything from how you pack to how you test and send out samples should follow set rules.
3. Processes
You need to write down and share all the steps in your work, making sure they’re clear and performed the same every time. It’s important to keep checking that everyone is doing things the right way.
4. Procedures
A procedure tells you how to do important parts of your work to get consistent results. Everyone needs to know these steps and follow them every time. If something doesn’t go as planned, you need to talk about it right away and figure out why.
5. Premises
Your work areas need to be clean all the time to stop any mix-ups or accidents. All equipment should be put in the right spot and checked often to make sure it works correctly and doesn’t cause problems.
How Does GMP Differ From cGMP?
Good Manufacturing Practices (GMP) and current Good Manufacturing Practices (cGMP) both play a big role in making cable assemblies, but they do have some differences. GMP lays out the basic rules to make sure cable assemblies are made safely and work well, following the guidelines set by regulators like the FDA.
cGMP, or “current Good Manufacturing Practices,” updates and adds to these rules by focusing on keeping up with the latest methods and technologies. In cable assembly, this means always improving how things are done to meet the newest quality standards. The “current” part of cGMP is about making sure manufacturing methods are always the best they can be based on the most recent and effective systems.
How to Implement GMP for Cable Assembly
1. Set Up the Right Environment
First, make sure your workspace is spotless and everything’s in the right place. Arrange your tools and materials so you can reach them easily without any confusion. A tidy area helps avoid any mess that could interfere with the cable assemblies, which is key for maintaining quality.
2. Train Your Team
Everyone in your team needs to know the GMP rules thoroughly. Consider setting aside a few days for training where you explain everything—what’s expected and how everyone’s role fits into the big picture. The end goal is to ensure everyone in your team is on the same page.
3. Document Everything
Write down each step as you make the cables, from when materials arrive to when the final product ships out. Keeping track of this helps you understand what’s happening at each stage and lets you spot where you might need to make changes.
4. Check Quality at Every Step
Check the cables as you go, not just at the end. Look over the insulation and test the connections after you put parts together. Finding issues early can save you from bigger problems down the line.
5. Review and Improve
Keep an eye out for how you can improve things. Every once in a while, review your processes. Look for parts of the process that seem to lag or cause errors. Figuring out how to fix these glitches can make your whole operation smoother and your products more reliable.
Final Verdict
Now that you’ve implemented GMP in your cable assembly production, you’re likely noticing smoother operations and a significant boost in product quality. This rigor is critical for electronic assembly solutions, where precision and reliability are paramount.
With these practices in place, your production line should be a model of efficiency, minimizing errors and downtime. The investment in training your team and maintaining a pristine environment pays off by reducing waste and enhancing the overall quality of your outputs.
Moreover, incorporating state-of-the-art technology helps you stay at the forefront of the industry, enabling you to monitor processes and make adjustments as needed. This proactive approach ensures that you consistently meet, if not exceed, customer expectations.
Moving forward, continue to review and refine these practices to stay ahead of industry standards and maintain your competitive edge.
Video
Infographic
Good Manufacturing Practices (GMP) ensure precise and consistent production of cable assemblies. GMP uses strict procedures, rules, and documentation to maintain quality at every step. Explore the infographic below to learn about the five key components of GMP.