As electronic technology advances, there is a growing need for high-Tg boards. Tg, a key property of epoxy, signifies the temperature range at which the base material undergoes a transition from a solid and rigid state to a rubbery state. Different PCBs possess distinct Tg values based on their substrates.
Exceeding the Tg value during operation can negatively impact PCB fabrication, hence the significance of selecting a suitable PCB. It is crucial to ensure that the Tg value of the chosen PCB is at least 20-25 degrees Celsius higher than the anticipated operating temperature of the device. For example, if a PCB has a Tg value of 130 degrees Celsius, the device’s working temperature should remain below 110 degrees Celsius.
Interested? Here’s a detailed breakdown of high-Tg printed circuit boards.
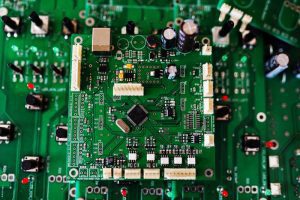
(ASphotofamily/Freepik)
What is High Tg?
Tg, the glass transition temperature, marks the point where the base material shifts from a solid to a rubbery state. No melting occurs; instead, a structural change takes place. Tg measurement is intricate due to factors like molecular structure, resulting in different values for different materials. Even materials with the same Tg can vary in technical characteristics.
High Tg materials have several advantageous properties:
- Long delamination durability: High-Tg materials age more slowly, ensuring enhanced reliability and safety over time.
- Resistance to high temperatures: These materials can endure elevated temperatures without significant degradation.
- Low thermal expansion: High-Tg materials exhibit minimal dimensional changes with temperature variations, enhancing stability and reliability.
Why use High Tg PCBs?
Increasing the Tg of a PCB substrate enhances stability. It improves heat resistance, chemical resistance, moisture resistance, and overall device stability.
For high power density devices with significant heat generation, high-Tg PCBs excel in heat management. They allow for larger printed circuit boards or adjusted design and power requirements, reducing heat generation.
In compact and densely populated multilayer and HDI PCBs, efficient heat dissipation is crucial. High-Tg PCBs are a preferred choice for reliable PCB fabrication, addressing heat-related concerns.
For multilayer and HDI PCBs with compact and dense circuits that limit air circulation, heat generation becomes a concern. High-TG PCBs are the optimal choice for these applications as they address the heat-related challenges and ensure device functionality and hardware integrity.
Where are High-Tg materials used?
High-Tg materials are extensively used in computer systems, communication equipment, and precision instruments. They offer superior heat resistance required for high-functionality, multi-layer PCBs. High-Tg PCB substrates outperform standard FR-4 in mechanical strength, water absorption, adhesion, dimensional stability, thermal expansion and thermal decomposition. Consequently, there is a growing demand for high-Tg PCBs, despite their higher cost compared to regular PCBs.
Additionally, high-Tg materials find favor in LED lighting due to their ability to handle higher heat dissipation. While metal core PCBs like aluminum PCBs are an alternative, they come at a higher price.
Industrial Use of High-Tg PCBs
High-TG PCBs find application in various industries, each with its specific requirements:
- Engine controllers: The efficiency of an engine relies on reliable controllers. High-TG PCBs are crucial to withstand higher temperatures generated during increased RPM and extended running hours.
- Metal industries: In metal processing, which involves cutting, grinding, welding, and melting, temperature fluctuations can destabilize microcontrollers. High-TG PCBs are essential to ensure stability and reliability in these machines.
- Other applications: High-TG PCBs are also used in WiFi boosters, embedded computer systems, low-cost PLC in contract manufacturing services, and RFID gateways. These applications benefit from the enhanced heat resistance and stability provided by high-TG PCBs.
Materials Used in High-Tg PCBs
In most high-Tg printed circuit boards, PCB and EMS providers tend to use the following materials:
- Isola 370HR: Popular material for high-Tg PCBs with excellent thermal performance and reliability.
- Ventec VT47: High-performance material known for exceptional heat resistance and mechanical stability in high-Tg PCBs.
- Panasonic R1755V/R1650V: Trusted material delivering superior thermal and mechanical properties for reliable high-Tg PCB operation.
- IT180: Favored choice with high glass transition temperature, ensuring reliability in demanding applications.
- Kingboard KB6167: Commonly used material providing excellent heat resistance and dimensional stability in high-Tg PCBs.
The Tg value is a critical factor to consider when selecting PCBs. Exceeding the Tg temperature can negatively impact performance and compromise mechanical stability. It is essential to determine the operating temperature early in the design process and choose the appropriate material, especially for high-temperature applications. By prioritizing Tg, PCB manufacturers can couple optimal functionality with long-term reliability.
Infographic
As technology advances, the demand for high-Tg boards increases due to their ability to withstand heat. Tg measures a material’s transition from solid to rubbery with heat. Matching a board’s Tg with the device’s temperature is crucial for reliability. Common high-Tg materials include Isola 370HR and Ventec VT47, ensuring devices work well in tough conditions.
Video
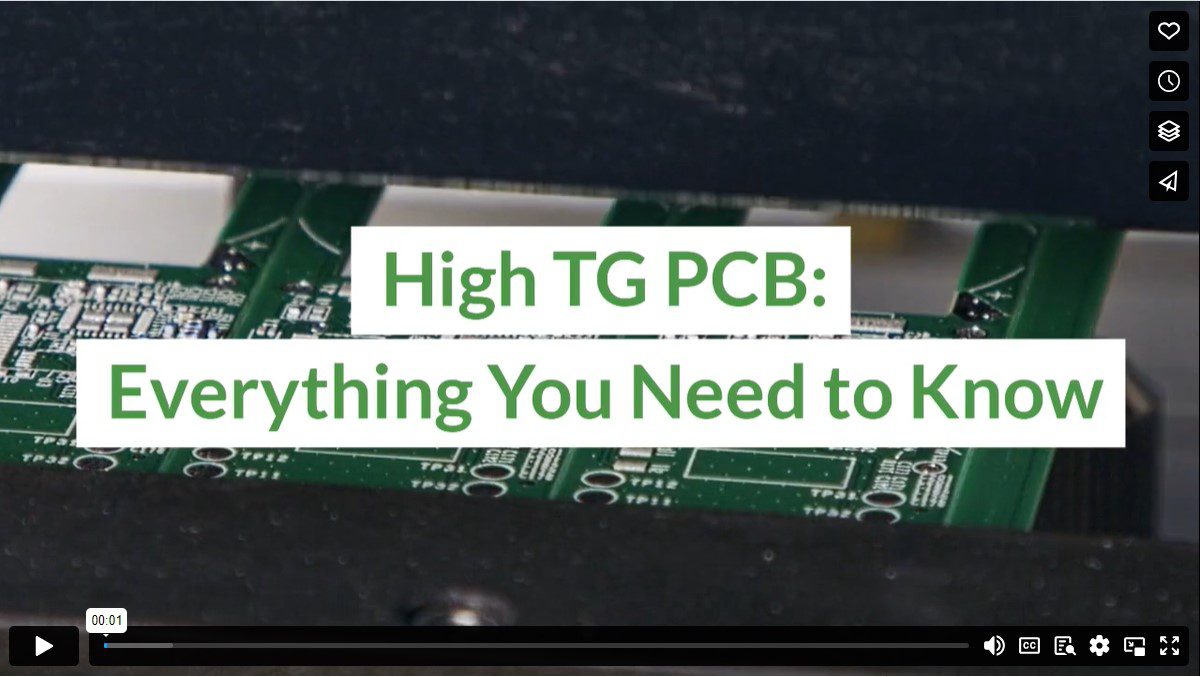