Can I save money by purchasing printed circuit boards with an odd number of layers?
This article provides an answer and goes deep to explain why choosing an odd-layered board is a bad move. In fact, investing in an odd-layered unit may actually raise the expense as well as lead time and may leave the customer with a warped PCB that won’t meet their expectations. Let’s explore odd-layered PCBs in greater detail.
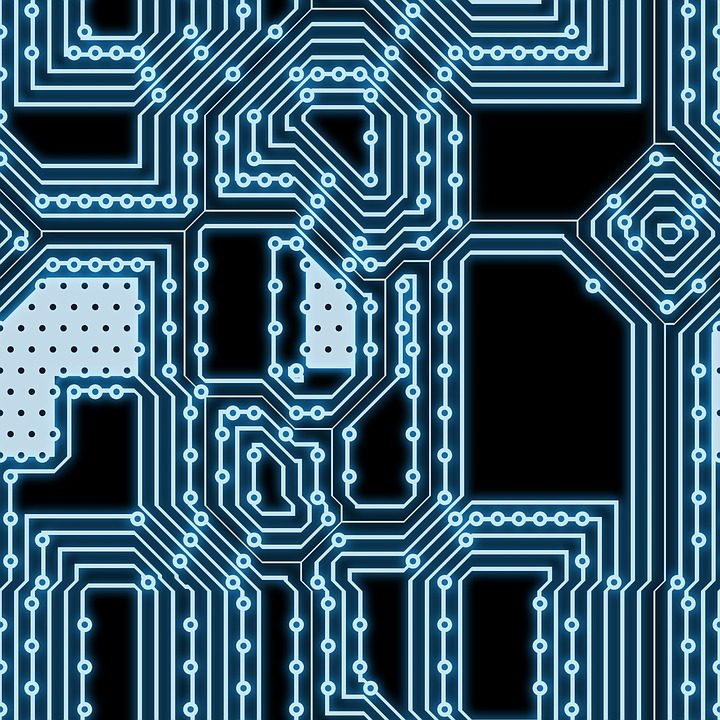
(Pixabay / dawnydawny)
The Problem with Odd-Layered PCBs
Various two-layer boards are laminated together into one stack to create a multilayer board. They’ll be pressed together for several hours at a high temperature inside a “PCB press” that delivers heat and pressure. After the curing process, the boards are cooled and then taken from the press. Odd-layered PCBs require a standard symmetrical housing in the process, and one of the copper layers is etched away.
But etching away copper from one side of the board causes warping, which is where the problem arises. Restricting warpage in any multiplayer circuit board demands a balanced setup of pre-peg and base layers, and this gets challenging with an odd number. Even if the warpage is brought under control, things can get worse after reflow or wave soldering when housing the PCB with components.
Also, the odd-layer design can cause problems in copper plating processes as the etching away of copper exposes the finer elements on the reverse design. It can even cause the two sides to have uneven weight, increasing the risk of over-plating or under-plating during the plating process.
Another important reason to avoid odd-layered PCBs is related to bending. When the multilayer PCB is left to cool after lamination bonding, the various laminating tensions may cause the printed circuit board to bond. With the increase in the thickness of the multilayer PCB, the risk of bending with two varying structures increases.
Why Even-Layered PCBs Are Better
Because odd-layered PCBs require a “non-standard” stacked core process for layer bonding, they may reduce the quality of the PCB manufacturing process. Even-layered PCBs, in contrast, don’t require additional processing on the outer core, which reduces manufacturing costs. The cost of processing the foil/core structure as well as the inner layer is almost the same in the case of an even-layered PCB.
Even-layered units also come with an even stack-up. While an unbalanced stack is sometimes permitted, odd-layered PCBs subsequently decrease processing efficiency. Even-layered PCBs, on the other hand, require no special processes and equipment, so there’s no risk of quality being damaged by pick-and-place offsets.
Additionally, the warpage of 4-layered PCBs can be managed below IPC600 (0.7%), but the warpage will cross this standard when a PCB with 3 layers has a large dimension, affecting the reliability of SMT along with the whole product. Hence, it’s better to use an even-layered PCB and convert 3-layered PCBs into 4-layered models. Because multilayered PCBs are known for their compactness and reliability, it’s always best to go with an even layered board if you want to avoid issues in PCB manufacturing.
What to Do If an Odd-Layered PCB Is a Necessity?
There will be instances where you won’t have the option to buy an even-layered PCB. For example, the need for a greater dielectric space or a certain signal routing requirement may cause you to invest in an odd-layered variant. In that case, make sure to do the following:
Integrate an extra power layer
A simple way to insert an extra power layer is to add a GND in the stack-up’s center without modifying any settings. The first step is to lay the configuration out as an odd-layered board, then insert a GND in the middle. Finally, you should label the other layers. This tactic can be used when the power planes of the design are odd while the signal layers are even.
Break the layer into two
This tactic works well when the signal layers are odd and the power planes of the PCB design are even. The division won’t result in higher costs, but it may improve the quality and shorten the delivery time of the multilayer PCB.
Integrate an empty signal layer in the middle of the stack-up
If you’re looking to increase the PCB’s quality and minimize the stacking imbalance, insert a blank layer in the stack-up’s center while marking the remaining layers. This approach is typically used for mixed media circuits.
Remember that multilayer PCBs can be faster and more powerful than single-layered units, so it’s important to avoid anything that may cause their performance to decline. Unless a greater dielectric space is really necessary, it’s best to go with an even-layered PCB.