Technology has been the driving force behind advancements in almost every aspect of humanity. Every year brings hundreds of new improvements in technology and new products to help make everyday life easier and more convenient. And with these advancements, we also see improvements in the components used to build them, the most important of which is the PCB.
Since PCBs are used in almost everything made these days, they must be made to suit a wide range of sizes, scales, and devices. Fortunately, there are as many ways to build a PCB as there are uses for them. This article will explore one of these methods, referred to as SMT assembly, and how it can be improved to prevent quality issues and improve overall design stability.
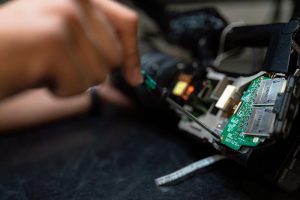
(RAEng_Publications / pixabay)
What is SMT Circuit Board Assembly?
Surface Mount Technology is one of the more popular forms of PCB construction. As the name implies, it uses methods of attaching component pieces to the surfaces of conductive material to form circuits. All components remain visible, and all the circuit traces are built into the board’s surface. This form of PCB assembly is utilized every day in almost every industry, including medical, military, and consumer technology.
Benefits of SMT Assembly
Compared to other methods of assembly, such as through-hole assembly, SMT offers a variety of benefits to PCB designers, such as:
- Better surface area utilization
- Lower production costs
- Potential for smaller boards
- Ease of customizability after construction
- High degree of design complexity
- Easier quality assurance testing methods and design modification
However, as is the case for anything, SMT assembly does come with its share of potential issues during production. But unlike more permanent or less-accessible board construction methods, SMT assembly allows the designer many more options for solving these issues.
Potential SMT Circuit Board Assembly Issues and How to Solve them
Here we will look at many common issues that can occur during SMT manufacturing and how designers can prevent or rectify them during the assembly stages.
Chip Mounting Issues
The process of affixing computer chips and other components onto a board is known as chip mounting, and it is in this step many quality issues can arise. If any chips are mounted in the wrong orientation or location, this will cause defects in the circuit.
Sometimes this is down to an error in circuit design, leading to chips being too closely placed or not close enough. Other times it can be a mistake of the assembler, who may misplace components on the board. Regardless of the cause, these problems can be easily corrected before any permanent steps render the board useless.
Ensure that all designs are checked thoroughly, with specific attention given to the board size and chip arrangement. If any components are not correctly measured before design, they will cause issues with the overall layout, but this can be easily fixed beforehand.
When the boards are being assembled, make sure all component orientations are marked. A resistor or logic gate will not function correctly if it is placed against the flow of the board’s current. If the board is being assembled by machine, go through the program’s chip recognition settings so that it will be able to identify every component and its orientation correctly. After placement, give each board a look over before the soldering begins, as incorrectly placed components can still be moved at this stage.
Soldering Process Issues
The soldering stage of assembly involves the application of liquid metal that will hold each component in its place on the board’s surface. The solder, when dried, is conductive and will allow the components to connect with the traces that connect each one. Several issues can occur during the soldering process that cause problems with the board’s components or the circuit’s layout. Since solder is integral to the formation of the circuit, these issues must be corrected before mass production begins.
If the board’s surface is not appropriately clear of debris or the temperature used during solder reflow is too high, it can lead to solder balling. Balls of solder in connective ports for components can lead to bridging, where an unwanted connection is formed that disrupts the flow of the circuit’s current.
Bridging can also occur if the wrong type of, or too much, solder is used at each port. The amount of solder used must be exact only to fill and not overflow each port. This will also cause issues such as bridging, but other problems can occur if the amount of solder is uneven. If the solder does not dry equally or is not evenly distributed, this can lead to tombstoning – an issue where one side of a component is pulled upright due to a lack of solder holding it in place.
The majority of these soldering issues can be prevented by using the correct solder type for the job you have planned. Ensuring that the solder will be solid enough to hold every component where it should be will prevent issues of component movement. Before use, solder paste should be kept in the correct environment – no more than 20 degrees centigrade with between 30-50% humidity – and not exposed to water.
Each connection port should contain the same amount of solder paste and only enough to secure the component in place without overflow. When using a stencil, always ensure it is properly aligned to prevent any unwanted solder from being left on other board surfaces. So long as the board is kept clear and there is enough space between each component, there should be no fear of bridging or beading causing short circuits.
During the application process, it is vital that all temperature settings are appropriate for the solder being used and that any fluctuations are prevented during the process. When using a reflow oven, special care must be given to the speed of the component conveyer belt and the pressure being applied by the scrapers. If a test board comes through with any of the above issues, recheck the parameters before mass production begins.
Conclusion
A well-designed PCB will form the core of many important and popular devices, but not if it suffers shorts or other issues. SMT boards’ design and application process is the most critical part of creating these devices, so special care should be taken at every stage. So long as the above issues are anticipated by your in-house assembly team or EMS partner, there should be no quality issues.