Along the PCB construction process, engineers face many possible hazards that might damage each board. One of the most troublesome and damaging disasters to befall PCBs is the short circuit. This can occur anywhere along with the framework of a board and have several devastating effects. From overheating circuitry to destroyed components, short circuits are a looming threat to PCB construction and assembly.
Today, we will look at the various ways you can find and correct short circuits with your boards. Many fixes can help salvage your hard work, so keep these points in mind.
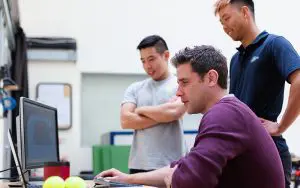
(RAEng_Publications / pixabay)
Signs of a Short Circuit on a PCB
The effects of a short circuit can vary from obvious visual damage to unnoticeable errors that won’t show up until later testing. In simpler cases, you might hear a quiet “pop” or see some arcing as a component short-circuits. As these are obvious visual errors, they are much easier to locate.
Other times, more subtle shorts may occur between input pins or other components, and their damage won’t show up until you run startup tests. Though it may be obvious, it is always important to run tests if you have any reservations about the stability of your PCB.
Test Types
Years of PCB production and development have created numerous tests that you can use to find short circuits. Digital multimeters, ground testing, and thermal cameras are three tests that we will explore.
While many short circuits are difficult to sot, some leave obvious visible damage. Before running any more specific tests, always remember to give your PCB a thorough visual inspection.
● Running a Visual test
Visual tests should be performed using a magnifying glass and a visual aid. Begin by tracing the circuitry from the power source, as it will be easier to keep track of where damage may occur. Keep an eye out for any whiskers around solder joints and pads that could lead to shorts. In some cases, burn marks or scorching may appear if a short has already occurred. These will be noticeable as the browning of a scorch mark will show up against the board’s green.
If you find any soldered joints that are cracked or places where the solder has seeped out of place to touch any other components, these may well cause issues. Also, make sure to check your vias. Ensure there are no plates if your design requires un-plated vias and that the plates are solid if they are meant to be. Poorly plated vias can lead to shorts and further damage throughout the board itself.
● Using a Digital Multimeter
If a visual inspection doesn’t reveal anything about the cause or location of the short circuit, get a multimeter and try to identify the physical location on the PCB. Although it doesn’t pinpoint the short’s exact location, it provides an idea of where to start looking.
Again, starting at the power supply, test each pair of neighboring traces and pads in turn. Neighboring connections should give you a high resistance reading. If you get a low reading, there’s your short. If you find no issues in neighboring joints, begin testing those on other or unconnected circuits, and any readings between unconnected circuits will indicate bridging.
● Using a Thermal Camera
While not an option for every company, if you have the budget to buy one, a thermal camera could help immensely. Since short circuits will lead to excessive heat output, a thermal camera will help you locate what part of the board produces the most heat. Power up the board, and if you find a component or join that is burning hotter than the rest, you will have found your shorts.
● Testing Components Relative to Ground
As multilayer PCBs will contain a grounded via or plane, you can use this to test for any shorts. Placing one multimeter pin to the ground and touching the other on the various components will see if any connections are disrupting the power. Don’t forget that most components will naturally hold a low resistance with the ground via. This can cause some testers to mistake a functional connection with a short if not paying proper attention.
● Testing Components Individually
Much like testing their grounding, use a multimeter to test each of your components in turn. This will help you to ensure that the issue is not in the components themselves. As dysfunctional components will usually look like functional ones, it is hard to predict an issue before installing them. If the connections between each component are fine, then the components themselves are your next stop, as many things can go wrong with them. Your board’s layout may also be a problem, as components whose joints are too close together will lead to shorts.
Measure the resistance readings on the components pads and pins to determine that they are running correctly. If no issues are found here, check the connection between the pads or pins and the ground to see if the issue lies there.
● Destructive Testing
If all the above tests come up blank, carry out the final test by physically dismantling your board. Removing each component and rerunning multimeter tests on the now-exposed pads will allow you to see whether these are the problems. This is an extreme form of testing and should be kept as a last resort. Eventually, you will see what parts of the board have caused a short through their absence. Not all component issues will be obvious through multimeter testing, and this will allow you to remove the problem and replace it later.
Conclusion
Short circuits are a frustrating but common issue. Hopefully, the various available tests mentioned above will help you locate and remove these problems swiftly and effectively. Once you have located the source, all that remains is cleaning up and replacing the damaged part or component. You can either do this yourself or work with a PCB circuit board assembly company.