Printed Circuit Board failures can have dire consequences for consumers and manufacturers alike. If a PCB fails in a home computer, it will frustrate and annoy the owner, requiring at least a replacement part or maybe even a new computer. If a PCB fails in a piece of crucial life-saving technology in a hospital, the consequences are far more severe.
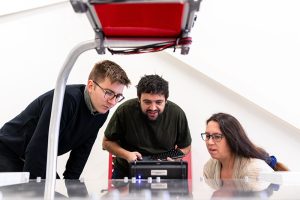
(ThisisEngineering RAEng / unsplash)
This is why every PCBA manufacturer must do everything possible to provide boards of the highest quality and reliability. To achieve this, engineers perform a whole host of tests during and after the manufacturing process to ensure the boards meet industry standards for efficiency. Among the many issues and errors, “burn-in” demands a closer look.
Let’s go through burn-in and how manufacturers can test for it.
What is Burn-in Testing?
Burn-in testing helps PCB manufacturers analyze how well a new board can handle excessive use and heat and whether these factors will lead to functional errors. Each board works within specific current and internal and external temperature parameters. Burn-in testing pushes these boards to the point where they usually fail to see whether these issues arise.
During burn-in testing, technicians run a current through a prototype board, operating the board’s firmware while it is held in a high-temperature environment. This typically happens for between 48 and 168 hours. The manufacturer then examines the board’s functionality to see what issues arose and whether any components or firmware failed. If defects occur during a device’s earliest days of use, you’ll get ample time to examine and rectify them.
What Does Burn-In Testing Examine?
The point of the test is to simulate what the printed circuit board would endure when used for an extended period, similar to what crash-testing does for vehicles. Burn-in tests are sometimes referred to as Accelerated Lifetime Tests.
Electronic devices generally have two significant periods in their life cycle at which they are most likely to fail: At the beginning and the end of their use. Burn-in testing helps to locate any defects that might affect a board’s infant mortality rate – that is, its likelihood to break down during the first weeks or months of use. Once it clears this period, a device will run with minimal naturally occurring errors until it begins to near the end of its life.
Benefits of Burn-In Testing
Beyond just ensuring that new boards will not break down during early use, burn-in testing offers several benefits to PCB manufacturers. Some of these include:
- Cheaper and easier repairs – Catching a catastrophic defect during the earliest days of production will make the issue much easier to fix.
- Reduced post-production failures – With the blueprints of the board, you drastically reduce the chances of losses occurring once complete assembly begins.
- Greater ability to meet customer needs – Knowing the extremes at which a board can function allows manufacturers to plan for the potential uses of their boards accurately. They can market boards capable of withstanding higher temperatures for heat-intensive machines, leaving other board designs free for less-resistant devices.
- Fewer returns and replacement costs – The less a board design fails, the fewer replacements a manufacturer will need to send out. This increases customer approval while reducing replacement costs that eat into profits.
- Preliminary component testing – Dynamic burn-in testing allows the PCBA manufacturer to monitor potential component issues early in the developmental cycle. Components operating at lower capacities during testing are much easier to replace early on.
Types of Burn-In Testing
Manufacturers use two main types of burn-in testing: Static and dynamic. They each provide different stressors and are necessary depending on the board’s intended uses.
Static Burn-In Testing
Static burn-in is the cheaper and quicker option that tests the board against a single criterion, typically heat or voltage. Testers run probes across the board from component to component in a temperature-controlled environment. Once the test chamber is up to the required temperature, the probes run a steady current through each component at a chosen voltage.
The point of this test is to examine the results of constant exposure to, or stage within, extreme temperatures. Static testing is ideal for boards stored in warm climates or machinery that runs at a steady high temperature. Each component is tested to determine the effects of this exposure, allowing them to be replaced should an error or defect arise.
Dynamic Burn-In Testing
Like static burn-in testing, dynamic trials involve setting a testing chamber at the desired temperature and running a current through each component. The main difference with dynamic testing is that the components also run input signals into each element. This tests the components against voltage and temperature resistance and allows the tester to see the effects these have on the components’ functionality.
Dynamic testing is best for boards operating in extreme environments or under heavy strain. These trials find malfunctioning components that need to be removed before later testing, cutting down on other errors. They also allow testers to see how much the firmware is affected.
Regardless of the test type, ideally, you want to perform burn-in testing multiple times to ensure reliable results. As these examinations examine the possibilities of errors over time, you’ll get the best results from the most prolonged time frames.
Infographic
Burn-in testing is essential for ensuring the quality and reliability of printed circuit board assemblies (PCBAs). Engineers conduct tests during and after the manufacturing process, including elevated temperatures and voltage stresses, to identify potential issues and errors. This rigorous assessment improves overall performance and ensures optimal performance under demanding conditions.
Video
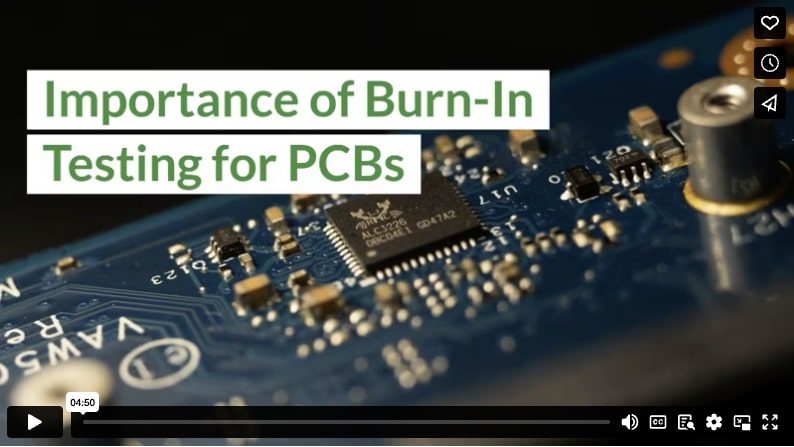