Businesses are not one-size-fits-all. What works for one company might not make sense for another. Manufacturing can be one of those areas. Should manufacturing of electronics and electronic parts be manufactured in-house or outsourced to other companies? There are a lot of factors to consider. We reached out to some experts to see under what circumstances they recommend outsourcing this manufacturing. Keep reading to see what they have to say.
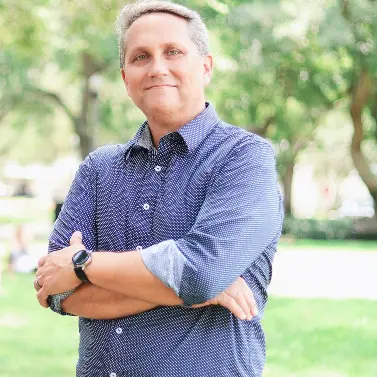
Mike Moninger
Four Benefits of Outsourcing Electronics Manufacturing
- It’s better for the environment. By outsourcing, all hazardous waste management, OSHA regulations, VOC problems, and EPA compliance are placed in the hands of the experts. Compliance with environmental guidelines can be difficult, costly, and time-consuming to implement. Violations are dangerous for employees and the environment, too. If a company is trying to manufacture components in-house, they risk dangerous mistakes and major liabilities.
- No need to invest in expensive equipment. Technology changes constantly, and processes come and go. By the time a company gets set up for a project, they may find that the machines and techniques they’ve acquired have become obsolete.
- It helps everyone involved. By outsourcing the manufacturing of electronics components and processes, both parties can increase their sales base. The original company can take on more jobs, and this bolsters the economy by providing more jobs for more individuals.
- You can see immediate results. Years of experience cannot be learned on the spot. It takes time to learn the proper technique, expert intuition, and the feel of the process. Machines can be difficult to operate, tools require precision, and calibration is vital. Even if a company were highly motivated, all of these things take time to establish. By outsourcing the manufacturing process, the benefits are immediate and no time is wasted.
Three Times Outsourcing Makes Sense
There are three situations where it makes more sense to outsource the manufacturing of electronics. Here they are.
- It costs less to manufacture and supply externally than it does to manufacture internally. Outsourcing the manufacturing of electronics comes with an additional cost to the organization. This cost includes the planning, management, transportation, and potentially the storage of the parts to be used internally. If the total cost of outsourcing is significantly less than manufacturing internally, then it makes sense to outsource.
- Manufacturing of the parts is not the organization’s core capability, and you don’t want it to be. It makes sense to focus on where the organization delivers greater value. If your organization delivers greater value through other activities which could include integrating the manufactured parts in the finished product, then it makes sense to outsource manufacturing of electronics. For some organizations, investing in the equipment, the process, the supplier relationships, and the labor doesn’t support the core competencies of the organization. For these organizations, it makes sense to outsource.
- The organization is at capacity and investing in additional capacity is not part of the long-term strategy. Another scenario is that the organization is manufacturing electronics internally and they are at or over capacity. The process internally is optimized and efficient. An additional investment like equipment or space is needed to process the additional demand. However, if investing in additional capacity is not part of the long-term strategy, then it makes sense to outsource.
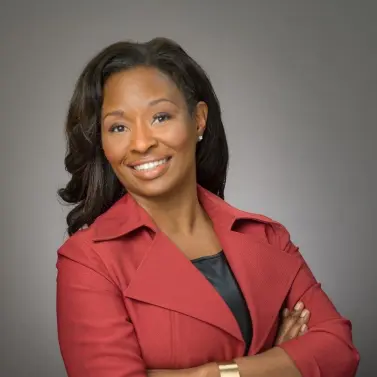
Sabrina Palmer
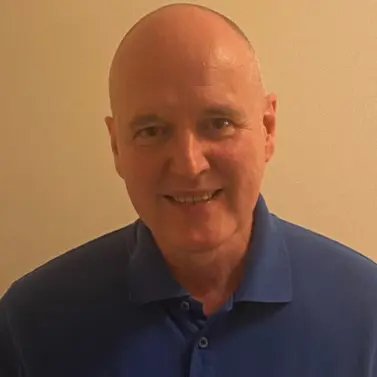
Greg Russel
Reduce Operation Costs
The primary occasion where it makes sense to outsource electronics is the reduction in operation costs. More reasons include the improvement of planning, a response to market conditions and needs, as well as creating working partnerships.
Outsource on a Case-by-Case Basis
Given the current state of the global supply chain, there are unique advantages to outsourcing electrical parts that do not exist in normal market conditions. If a company can more easily procure necessary materials to manufacture a part, either because of geographic or political constraints, it makes sense to outsource your manufacturing to them.
For example, a lot of the large manufacturers we work with are struggling to manufacture sensors needed for industrial equipment because of the semicon shortage. However, smaller Taiwanese manufacturers close to the large semiconductor manufacturing plants have no trouble filling these orders. This is a perfect example of a situation where larger companies with high demand should outsource their electronic part manufacturing.
Freeman Smith
This is a crowdsourced article. Contributors' statements do not necessarily reflect the opinion of this website, other people, businesses, or other contributors.