The core of every electronic device of the modern age is the printed circuit board (PCB). It forms the basis upon which every aspect of technology runs. PCBs are responsible for everything from the basic functionality of light switches to the complex network of a supercomputer. If any one part of these tiny, fragile components should fail or be even slightly incorrect, the whole system breaks down.
Protecting the components built into a printed circuit board is one of the biggest challenges for a PCB assembly company. While some designs, such as multilayer PCBs, inherently protect the components within them, many require other clever approaches. One such approach is conformal coating.
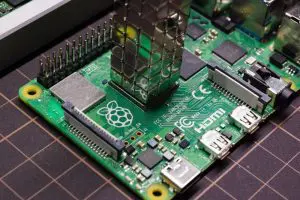
(Karminski/Unsplash)
What is PCB Conformal Coating?
Conformal coatings on a PCB are a thin layer of polymer film applied over the board’s surface and its components. It protects the components and board’s surface from contaminants such as dirt and grime. It also acts as an insulation layer for some boards that provides the added advantage of allowing components to be spaced closer together.
Other benefits of conformal coating include the following:
- Negligible additional weight to the overall board’s mass
- Elimination of performance degradation caused by environmental hazards
- Minimizes environmental stresses during use on a PCB
- Eliminates the need for complicated or sophisticated PCB enclosures
The Types of Conformal Coating
There are five main types of conformal coats currently in use. These are urethane resin, acrylic resin, epoxy resin, silicone resin, and parylene. Each one has its specific uses.
Urethane Resin (UR)
This is a type of liquid plastic, one of the most common forms of resin used in industrial and hobbyist projects. It is used as either a single- or double-part substance and is great for resisting chemical and humidity erosion. It can also be tinted if soldering occurs on or near it. However, it is difficult to remove urethane once applied and risks peeling after a time.
Acrylic Resin (AR)
Derived from acrylic acid, acrylic resin is a thermoplastic substance produced in either a hydrocarbon solvent or an emulsion. It is easy to apply and remove to any PCB assembly and causes no difficulty during rework or repair processes. In contrast, it has a low resistance to abrasions, making it bad for harsh or high-temperature environments. It is also one of the more affordable coating options.
Epoxy Resin (ER)
Epoxy is a type of reactive prepolymer that reacts with a range of co-reactants to form a hardened surface. It is often chosen for its high thermal, chemical, abrasion, and moisture resistance, making it ideal for harsh environments. Its downsides are that it is difficult to remove once applied, and the coating may shrink during the curing process. Plus, you’ll need to remove the surface layer to make any repairs or alterations to any coated components.
Silicone Resin (SR)
Silicone resins have a low molecular weight which is useful in pressure-sensitive coatings. This gives it a strong and reliable surface that offers great resistance to corrosion, humidity, and extreme temperatures. It also protects against chemical corrosion but can be removed using strong chemical strippers. Despite being the hardest to remove, it is one of the easiest to apply, adhering well to most PCB materials and components. It will also interfere with any attempts at repairs and modifications, requiring complete removal to allow them.
Parylene (XY)
Parylene provides the best-known extreme temperature and solvent resistance of all types of coating. Makers apply it through chemical vapor deposition, which involves heating it into a gas and putting it into a vacuum chamber. The film that forms is then applied to PCBs and other electronics, creating a colorless, transparent film. Despite these advantages, parylene can only be removed by scouring it off and is not ideal for long-term outdoor exposure. It also requires specialized equipment to perform the vapor deposition, making it more expensive in the short term.
Manufacturers apply the coatings using one of four techniques:
- Brush method – The coating is applied by hand using specialized brushes. As a result, the coating will be thicker and less appealing, but it is the most accessible option for the application. This method is best for low-volume production or repair work.
- Spray method – The chosen coating must be in aerosol form and is then sprayed upon the surface of the PCB. This is one of the slowest methods due to areas of the board needing to be masked beforehand. However, it provides an even clean finish and is a cost-effective application method.
- Dipping method – The board is submerged in the coating solution, ensuring the board is appropriately coated when withdrawn. This is the quickest coating application method and offers complete coverage, especially for high-volume orders. However, it poses an issue for boards that require areas masked off beforehand.
- Selective coating method – Robotic spray nozzles apply the coating only to specific areas of a PCB according to a pre-programmed command. This is another quick method and is great for high-volume orders without needing component masking to protect areas. Its biggest drawback is that the board must be designed with this method in mind to ensure that the spray areas are accessible.
What to Consider While Choosing a Conformal Coating
When a board needs to be coated, some considerations must be made to determine what coating is needed. Consider the required coating consistency across all boards, as some resins are not easily repeatable. Large orders will need to be done by machine, requiring consistent coverage by spray or dipping. Smaller orders or repairs are best done by hand, spray, or brushing and require a resin to match. However, if the costs and design allow it, a selective coating is better for large orders.
The intended use of the board will also determine the type of resin. For standard indoor electronics, urethane or acrylic are fine, as the devices will not face many environmental issues. For larger outdoor machinery, much tougher resins are necessary to help protect the boards from extreme environmental stressors such as temperature and moisture. The same is true for any machinery that faces high temperatures or extended uses, such as computers or vehicle technology.
The last consideration is cost: commercial electronic devices usually choose cheaper coating options to keep costs down. However, it’s best to balance costs for much larger projects, especially those requiring high reliability.
Protecting a PCB’s components is a simple task with conformal coating. These easily applied resins are ideal for giving each board an additional layer of protection and reliability. The main concern is ensuring the correct coating is used according to the board’s requirements.
Infographic
Electronic devices rely on PCBs to perform their essential functions. However, they are vulnerable to environmental harm like dust, moisture, and chemical exposure. To safeguard them from such problems, it is necessary to coat the PCBs with a conformal coating material, providing extra protection against these external factors. This infographic will help you comprehend PCB conformal coating in detail, its various types, and what criteria to consider when making this decision.
Video
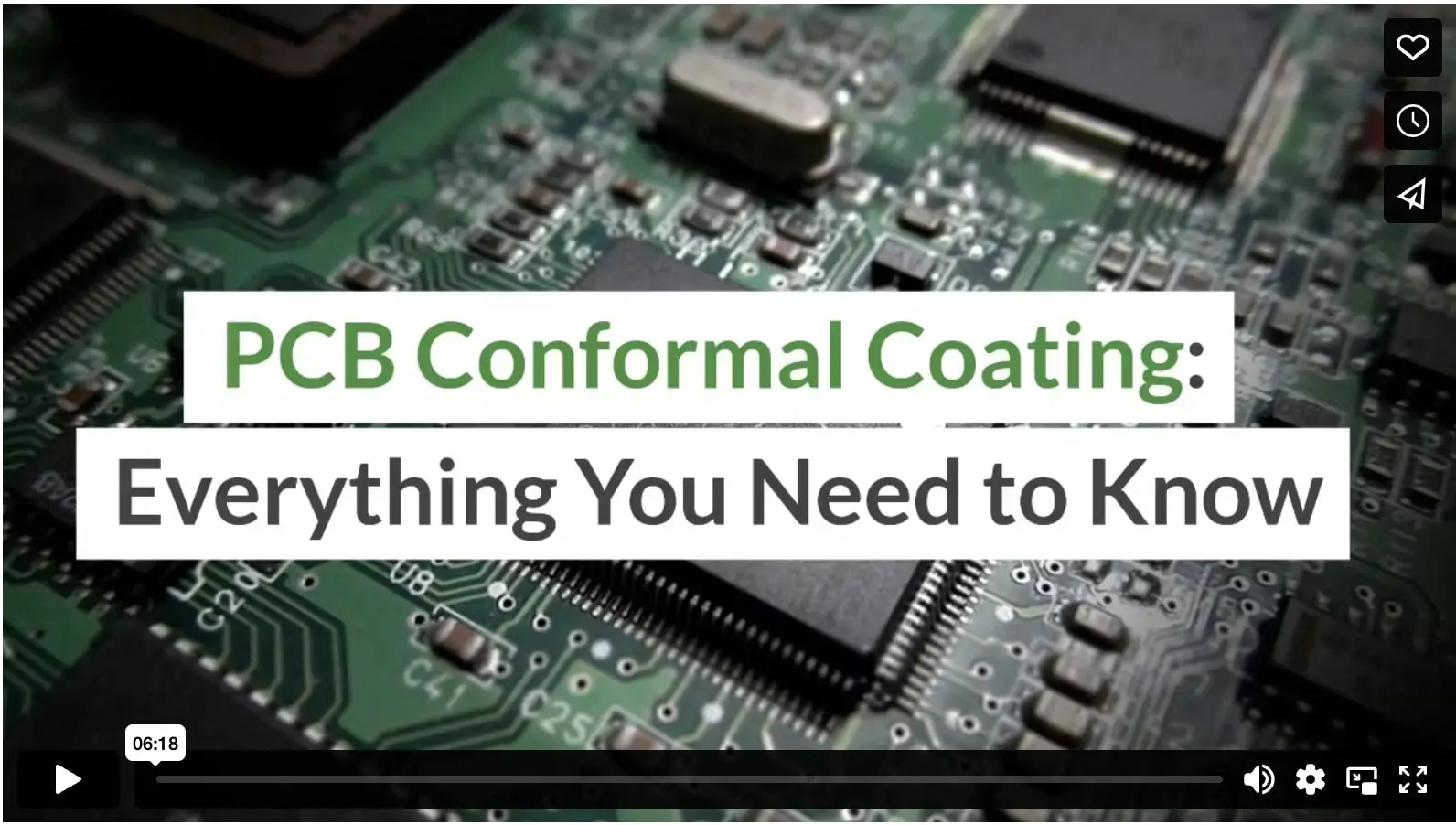