Recall the 1964 James Bond spy thriller “Goldfinger”? It turns out PCBs have gold fingers, too, although they don’t smuggle any components (get it?). What PCB gold fingers do is play a critical role in the inner workings of circuit board technology. Interested? Read on to learn everything about gold fingers and the functions they perform for a printed circuit board.
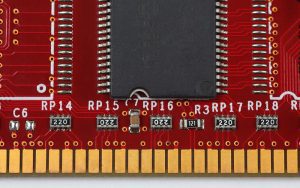
(nanoslavic / pixabay)
What Are Gold Fingers?
Various complex parts make up a circuit board, and the parts that connect its components are called gold fingers. Basically, gold fingers refer to the gold-plated connectors placed around the edges of a printed circuit board prototype. Their purpose is to connect a secondary circuit board and a motherboard into one cohesive system.
Gold fingers are versatile and used in many technology products. Everything from tablet computers to games consoles uses them. The reason is that gold is highly conductive and easily malleable. Currently, there are two types of gold being used in this manner:
- ENIG – Electroless Nickel Immersion Gold: This type of gold is softer and thinner (usually between 2u and 5u), making it easier to solder and manipulate into place. It is the cheaper option of the two. However, it is also weaker and so not ideal for frequent insertion or removal.
- Electroplated Hard Gold: Much harder and thicker than ENIG (typically 30u), Electroplated Hard Gold is ideal for the abrasive effects of frequent circuit board use. However, it is much more costly than ENIG.
First, the copper of the wiring is coated in nickel to help boost conductivity between the gold and the copper. Between 3 and 6 microns of nickel are plated to the finger connector edges.
Then, electric currents are passed through the nickel to attract the gold plating. Cobalt is occasionally used to help improve the surface resistance of the connectors. This process must be done under strict observation, as the surface needs to be as smooth as possible. Any defects must be found during the plating process, or else connections will not form properly.
How Are Gold Fingers Used?
Acting as connectors, gold fingers aim to connect two PCBs by a strong, interlocking hand-in-glove system. The choice of gold is made to enhance the conductivity of the connection. Gold is highly conductive and so will allow power to be passed through the connectors quickly. Further, the use of hard gold serves to protect the fingers themselves from damage. Its thickness means that very little damage and wear will occur to the fingers over time. Generally, hard gold allows for the fingers to disconnect and connect up to 1,000 times.
PCB designers may use gold fingers in different ways during the production of personal computers. Typically, they’ll use them for interconnection points, special adapters, and external connections.
- Interconnected points are the parts of a PCB that connect it to other boards within the computer, such as the motherboard. This helps to build the basic structure of a computer and allows it to function quickly and effectively.
- Special adapters are used to connect additional components to the PC’s structure. Peripherals such as sound cards, graphics cards, and extra RAM space are connected by gold fingers. This is where the gold fingers’ thickness helps to protect the hardware during multiple disconnections and reconnections.
- External connections are peripherals such as monitors, speakers, and printers. These also require the ability to withstand multiple disconnections, as well as the ability to process data. Gold fingers’ conductivity allows for high fidelity data transfer when using these peripherals.
Most importantly of all is the gold finger’s ability to transfer and hold electrical current. Without this vital power, none of the above functions would be able to run. The gold used in gold fingers is conducive enough to maintain the connections necessary for frequent use. It also helps ensure that little to no damage is incurred through power use and surges.
Gold Finger Specifications You Should Know
Several important specifications must be adhered to in the construction of gold fingers. Since even minor imperfections can lead to damage or misconnection, they must be built specifically. All plating must be as smooth and equal as possible. As such, any beveling is angled precisely to allow excellent connectivity along connective surfaces.
Further, the following three steps must be followed when assembling gold fingers:
- Gold fingers must always be directed away from the center of the PCB
- Plated through-holes must be kept as far away from gold fingers as possible
- Gold fingers must not have any contact with any screen printing or solder mask found on the PCB
Failure to follow these rules could disrupt the gold finger’s ability to form solid connections. This disruption will lead to errors and miscommunication between the motherboard and any connected devices.
These production standards were first put in place in 2002 and later amended in 2012 and 2015. Currently, these rules are known as ICP A-600 and ICP-2020 and cover the following standards:
- The gold plating along the edges of PCB contacts must consist of between 5-10% cobalt.
- Gold finger plating thickness for finished boards should be in the range of 2 to 50 microinches.
- The edges should have a smooth finish with no exposed nickel visible to a visual test conducted with a magnifying lens.
- A piece of tape should be applied to the edge of the gold finger. When it is removed, no traces of gold should be found stuck to it.
Further changes will always be made as industry standards and techniques improve. These standards can be found freely online and are adhered to by all professional electronic assembly solutions.
PCB Gold Finger Beveling
Beveling is the process by which squared corners are shaved to become sloped. This is integral as it helps to create a stronger, interlacing pattern for the gold fingers. This specific pattern of bevels ensures that the fingers remain firmly in place within the socket. This type of fitting is known as hand-and-glove.
After you apply gold plating to the finger connectors, the edges are then beveled. Using a pre-planned pattern allows the edges to be cut to angles between 30 and 40 degrees. The pattern ensures that the angles correspond to the opposite slopes in the insert slot.
Depending on the size and shape of the board, the gold fingers will be designed to have different lengths. Again, corresponding to the shape of the insert slot, some fingers will vary in length. They help guide the fingers into place when inserted, keeping all connection points lined up correctly. This allows for a more precise form of connection, with longer fingers snapping into place and holding the rest firmly.
The shapes and lengths of the fingers also prevent the user from inserting the connector with the wrong orientation. This helps to prevent any undue wear and tear or other damage that might occur to the fingers.
As a leading PCB assembly company, we are happy to answer any questions about circuit board technology. Contact us today to speak to one of our electronic manufacturing service specialists.