A PCB is a core aspect of any electronic used in a household or industrial setting. Good-quality PCB boards require PCB milling, which is the process of removing copper tracts from a sheet of PCB material to recreate the indication tracks, pads, and configurations based on the provided diagram on a PCB design.
PCB milling is subtractive, just like the popular and commonly used chemical PCB etch process. However, PCB milling is chemical-free, making it ideal for use in a typical home or office without exposure to hazardous chemicals. Because the device gets discarded to create electronic seclusion, PCB milling is much safer than chemical carving. Moreover, the process can fabricate the circuit board to its best possible state.
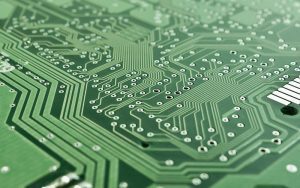
(blickpixel / pixabay)
Advantages of PCB Milling
PCB milling is beneficial for PCB prototyping and making special PCB designs. Its biggest advantage is that it doesn’t fabricate a circuit board with chemicals. Also, if you decide to skip outsourcing and make your own PCB at home, PCB milling can assist you with the process.
Some issues will arise in in-house manufacturing, like disposing of the chemicals and using the wet process for in-house production. Using the wet process, it is not easy to fabricate high-resolution boards, but you still have to drill to cut out the circuit board from its base material.
On the other hand, prototyping with a CNC machine can help you create faster, eliminating the need for wet processing. If you’re already using the CNC machine for drilling, it can take care of both parts of the process (milling and cutting). This is because a CNC machine is useful for three things: drilling, milling, and cutting.
Without modern machines, the production process becomes challenging with wet etching and manual drilling afterward. This is because only a few boards can withstand manual drilling in a lab without experiencing wear and tear. Even if the production unit was designed to perform that work, it would cost several times more than some decent CNC machines.
PCB Milling Processes: Some Facts
- You can complete the milling process in 30 minutes, but some factors affect this time, like the thickness of the bit, the dimension of your circuit board, the number of components, and the alignments it can accommodate.
- PCB fraying is a process in which you remove the redundant copper from a circuit board to create traces and paths based on the specified design.
- A PCB manufacturer can offer you software for PCB milling.
- You can do PCB framing in a lab environment without the risk of hazardous chemicals because it is a non-chemical process. It also has a quick lead time because of the number of circuit boards.
- The accuracy and sharpness of milling bits directly impact the quality of a PCB.
- Milling has little to no effect on the quality or precision of a circuit board for the rotational speed of bits.
- If you’ve never used a milling machine before, you have to learn this technique of manufacturing PCB and practice first.
- There are two categories included in the software: Vector and Raster.
- Software that utilizes raster comes with a lower processing resolution than vector because it is dependent on raster info.
Parameters of Milling
The lowest tool diameter is 0.8 mm, normal diameter is 2.0 mm and custom diameter is >=0.8 mm <2.0 mm. However, the internal and external contours of the board are milled as per the client’s requirement. The outside contour may be 90 degrees if the client has that requirement, while the internal nook of the PCB design features the trivial radius of the milling edge. Normally, the edges of the rectangular shape are circular to balance a comprehensive rectangular compartment. Moreover, the milled area is pierced at every intersection.
The contours and breakaways of PCB are normally machined, and some rules are set in order, like:
- There is no additional price for frying
- The danger of harm or accident must be avoided considering the copper endurance of a circuit board.
- The inner and outer contours of the board should be marked with a channel length of 1 μm to avoid measurement errors.
Etching vs. Milling
Generally, chemical grafting demands direct or film laser imaging, although the grafting itself is typical and costs less in the global production of PCB systems. While isolation milling doesn’t require film art, it results in high tooling costs and issues with the program. This is why isolation milling is more suitable for PCB prototyping.
In etching, there is no difficulty as the FR4 carrier isn’t etched. However, the chemical-laden process can only be performed in a factory setting.
Conclusion
PCB milling is now a common practice in the mass manufacturing of PCBs. Every leading electronic prototyping company uses PCB milling for low-cost, quick-turn prototypes that improve the customer experience. Find a company that utilizes advanced PCB milling machines to fabricate your board and employ the drilling procedure effortlessly.
Video
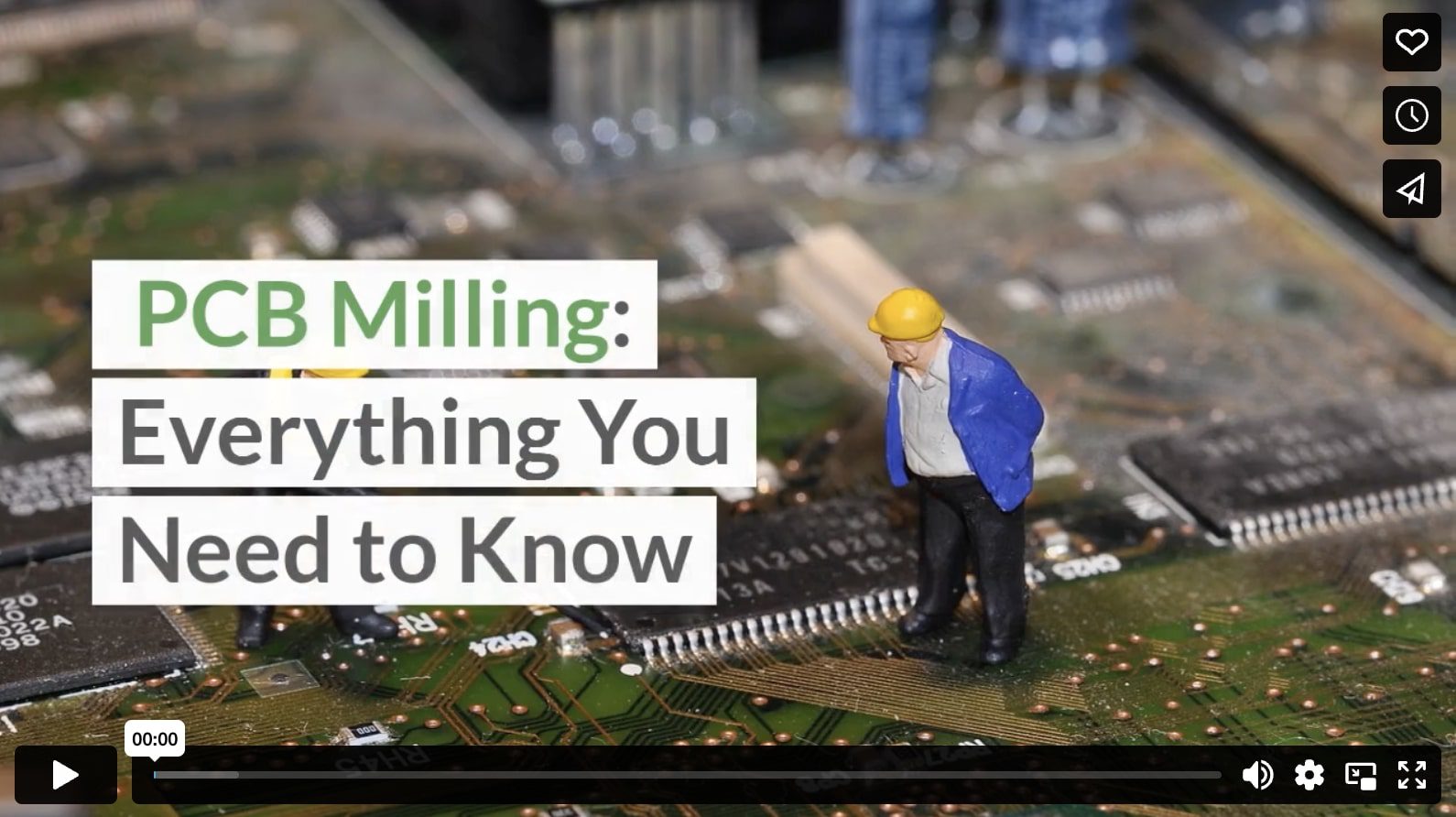