PCB assembly is a delicate art. Throughout the board manufacturing and assembly processes, things can go wrong. Sometimes it’s something as simple as a little cross-chatter between paths. Other times it’s more severe issues like component burnout.
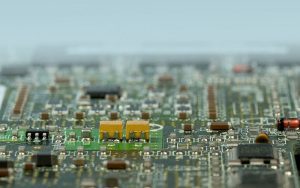
(blickpixel / pixabay)
All of these issues will mean an alteration to your design plan, perhaps even your board layout. Regardless, they mean your board will not work, and you’ll have to start again.
However, another type of issue can occur during the manufacturing process. This issue is called tombstoning. It is not overly common, but it does happen, and it’s something you can plan for.
What is PCB Tombstoning?
The name PCB tombstoning will likely bring a specific image to mind: that of a stone slab standing upright in a cemetery. This image is, surprisingly, an accurate depiction of what is happening. However, you may also hear it referred to as the Drawbridge Effect, the Manhattan Effect, or the Stonehenge Effect.
When a board has experienced tombstoning, it means that one or more of the components within its layout has stood upright. One end of the component’s connectors has failed to set correctly, and the heavier end has freed it. The component will stand upright, unconnected at one end. When this happens, it will be rendered useless.
What Causes Tombstoning?
The most common cause of tombstoning is when there is a difference in the wetting speeds of the solder that connects the component in place. Typically, a component is laid above its connection points, and the solder within them melts simultaneously. The component then drops into place, and the solder dries, forming a completed circuit. On rare occasions, the solder will not wet simultaneously, causing the component to drop on one side and warp until it stands upright. The component has now become tombstoned.
This is not the only way it occurs, but it is the most common. There are many other causes that you should look out for when designing your PCB. These include:
- Improperly placed or inconsistently sized solder pads
- Uneven reflow oven temperature settings
- Inconsistently melting material choices for PCB construction
- Incorrect PCB orientation within a reflow oven
- The presence of nitrogen
Fortunately, developments in PCB construction have helped remove a few older causes of tombstoning. Vapor Phase Reflow (VPR) welding and Infrared Reflow (IR) are two old systems for setting components that often led to Tombstoning. The inconsistent melting techniques they used were a frequent cause of headaches amongst manufacturers. Thankfully, due to the development of new reflow ovens, these issues are now a thing of the past.
How can you Avoid Tombstoning?
Knowing the causes of tombstoning allows us to plan and keep it from happening. There are many ways you can design your PCB production around this issue, so keep the following tips in mind:
1. Double-check all pad dimensions.
As mentioned above, a common cause of tombstoning is when the solder pads are sized incorrectly. Before your design begins production, go back through and check every pad fit within your necessary dimensions. This is always the best place to start, as making sure your plans have correctly sized and shaped solder pads will ensure that components will not slip out as easily.
2. Consider changing your PCB finish.
The industry standard finish for PCBs is Hot Air Solder Leveling (HASL), which is cheap and available. This can cause problems with smaller components (such as those in the 0201 and 0402 categories) and tombstoning. Therefore, you should always carefully consider the finish you choose for your PCB. Other types, such as immersion gold or tin, will be much better suited and prevent you from an uneven surface finish.
3. Be concise with your component layout.
A lot of time goes into planning the ideal placement of components on a board, but not always preventing tombstoning. When designing your routes, be sure to keep all traces of equal width, especially with smaller components. Subtle changes in trace width can alter the size and shape of your pads and increase the risk of your components rising. Moreover, keep all traces connected in the same orientation throughout the board. This will mitigate potential variable heat dissipation, which can build up in traces that run unpredictably.
4. Keep your solder mask thickness down.
For those who don’t know, a solder mask is a thin polymer layer used to protect exposed copper traces and pads from oxidation. When designing your board, you should ensure that your solder mask remains below your land patterns. If it rises too far, it can restrict solder flow as it melts, causing inconsistency in its coverage for component joints. Check with your EMS company to ensure that their solder masks will keep the level low and unobtrusive.
5. Ensure your board’s inner copper layer is even.
Although much harder to see when the board is completed, issues with the inner layer’s copper coverage can also lead to tombstoning. Since the copper inside your board will help spread the heat applied to it, it is vital to make sure the copper coverage is even. If it should appear that the copper does not cover all of your pads, then this will cause an uneven distribution of heat to occur. Edit your design to either keep all pads clear of the copper layer or all of them fully contacted, and this will prevent tombstoning and aid in the setting of the solder.
6. If possible, use a stencil design.
Stencils allow for an even distribution of solder paste, and they can be a great way to avoid tombstoning for mass-production boards with simple layouts. It can be much more effective in ensuring that each component receives an adequate amount of solder to use a stencil since you are manually applying it. Test for the correct amount of paste to be applied before you begin, as too much can lead to beading on the board’s surface, while too little will fail to hold components in place.
Conclusion
Tombstoning, like many issues, can be easily kept in check by thorough planning. It may take a little longer to perfect a new design, but the extra time taken going back over the smaller details can save you a lot of time and money. Keep these suggestions in mind when planning your new boards, and you can help wipe out tombstoning from your future productions.