More powerful technology requires more powerful circuitry. As our devices and machines grow smarter, so must the circuit boards that run them. All circuits are systems by which signals are transmitted through a series of components to produce a specific result. These circuits are constructed from copper traces, each providing a certain degree of speed, resistance, and power to the signal.
Transmission lines are an answer to the question of increasing board performance. They improve signal speed and maintain integrity within a PCB layout. Here we will explore what transmission lines are and a PCB assembly company can use them to improve the power of PCBs.
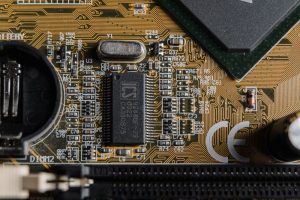
(Tima Miroshnichenko/Pexels)
What Is a PCB Transmission Line?
A PCB transmission line is an interconnection that allows signals to travel from a transmitter through receivers along a printed circuit board. They consist of two main conductors: the signal trace and the return path. Typically, a PCB designer will integrate the return path into a ground plane to help disperse current and maintain a steady circuit.
PCB designers should also consider the length of each trace in a circuit, as they are typically short. This allows the signal to travel quickly without losing much integrity, as it does not have time for the waveform to dissipate.
However, longer traces will alter how the signal moves, resulting in a gradual degradation in its waveform. This means that longer traces will see the signal degrade or become unstable the farther it must travel. For high-speed devices, this can be problematic as it means the signal needs to maintain its appropriate strength to function correctly.
These longer interconnections are considered transmission lines, as opposed to regular traces, due to the alteration of the signal. Unfortunately, there are no set rules regarding the exact length a trace needs to be when it becomes one, as signals will degrade at different rates due to several factors.
Generally, designers will plan transmission lines to the signal’s impedance requirements rather than the trace’s length. This is the next best thing to predicting whether a signal will degrade, as it simply assumes it will occur and plans an alternative.
Types of Transmission Lines
The two conductors of a transmission line (the trace and the return path) are separated using a dielectric material. The width of the trace is determined based on the copper’s weight and the depth between the two conductors. This balance ensures the traces have the same impedance throughout their length. This is known as controlled impedance routing.
There are three main types of transmission lines in use for PCB designs. These are:
Microstrip
A microstrip requires that a routed trace has a single adjacent reference plane. The reference plane is where the return path runs, which is usually set into the outer layers of the board. It is possible to run a microstrip through the inside of a board, embedding the routed trace under its surface.
Stripline
A stripline occurs when a routed trace is run between two reference planes for the return paths, usually within the board’s substrate. You can configure striplines in different ways, such as running the routed trace somewhere closer to one plane than the other or running multiple traces in parallel. This allows for a greater signal while providing a bigger return plane.
Coplanar
Used more rarely than microstrip or stripline traces, coplanar transmission lines consist of an external signal trace running between two ground or reference planes on either side. This allows the transmission line to have three conductors on the same PCB layer with a dielectric board material beneath. However, to function properly, coplanar lines require exact spacing between the traces along the length of the route.
When does an Interconnection Become a Transmission Line?
As mentioned previously, there are no hard and fast rules for determining whether an interconnection will be a transmission line. There are, however, rules for determining it after laying the trace.
As the signal transfer from two points on a board must be quick, you must address any deviations from this speed. The transfer speed will be fast for any circuit transmitting data at under 50 MHz (for an analog signal) or 20 Mbps (for a digital signal). Less than 10% of one-fourth of a wavelength, or equal to the fastest rise time of a digital pulse, is typical of a short trace.
However, these measurements no longer apply for signals of higher frequencies or data transfer rates. The signal will take longer than one-fourth of a wavelength to pass along the interconnection. In these cases, the connection will be considered a transmission line.
Transmission Line Layout Techniques
The most important thing to consider when laying transmission lines is controlling impedance. If you fail to control the impedance, the signal will face reflections and disruptions from the data’s high-speed movement. This will lead to corruption of the data, rendering the board useless. To prevent this, the impedance must be kept even along the entire length of the trace, meaning designers must calculate the physical dimensions of the trace. This is done by tailoring the trace width accordingly.
Fortunately, you can do this in a few simple ways, such as:
- Use one of the many transmission line design calculators that can be found online.
- Use the calculators included in the PCB CAD system being used. Many different PCB CAD systems include these calculators precisely for this reason.
- Discuss the possibility of transmission line usage with a chosen PCB manufacturer. As this is a frequent issue in PCB production, it’s safe to assume that most manufacturers will have experience handling them. As such, the IPC-2581 format exists to aid them in these productions and to help plan accurate impedance in PCB designs.
Once the specifications are in place, there are a few more rules to keep in mind while designing the actual layout of a printed circuit board assembly. These are:
- Do not run transmission lines through congested areas of the board – avoid splits or breaks that will otherwise interrupt the return path.
- Try to keep all transmission lines on a single layer.
- Use a ground via next to the trace as the transmission line must transfer between layers to maintain a clear return path.
- Do not break up differential signals on different areas of the board – avoid running them through vias and other components.
Transmission lines are a tricky aspect of electronics manufacturing that can mean the difference between a functional or corrupted board. It takes a great deal of planning and preparation to ensure that signals are correctly transmitted along the length of the longer traces. Use every tool at your disposal to ensure accuracy and plan for the ideal layout.