Ever wondered why most of the printed circuit boards that you see are green? The core of the board is actually a drab yellow color, but they are coated in a layer of resin known as a solder mask. The solder mask performs a couple of important functions. First, it protects the electronic traces on the boards from humidity and dust. Second, it makes it easier to manage the molten solder that will be applied to the board.
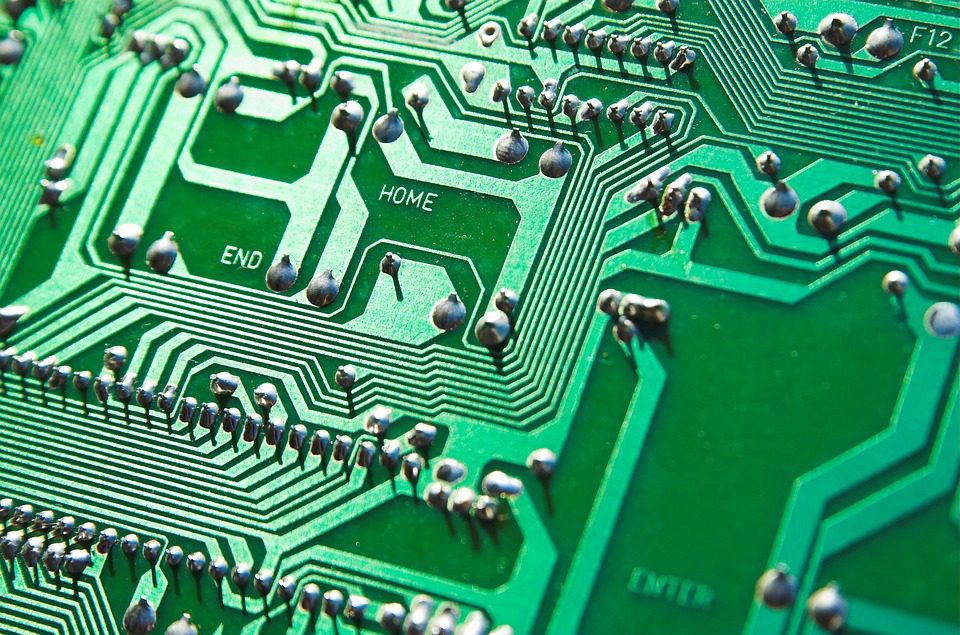
(Pixabay / axonite)
Solder masks are available in a rainbow of solid colors. You could even coat a board in multiple colors. Still, green is the shade we see most often on printed circuit boards.
It’s no accident that green is most commonly used for coating PCBs. Here are the most compelling reasons for going green:
- Easy on the eyes. Scientists agree that the wavelengths of green light are particularly easy to look at—even for long periods of time. Though automated inspection of printed circuit boards is common now, manual inspection used to be the review method of choice. In an effort to spare the eyes of people who spent their days scrutinizing the minutia of printed circuit board assemblies, green became the color of choice. Though the eye-relief may not be necessary due to today’s automatic optical inspection (AOI) technologies, old traditions die hard. Green boards live on.
- Provides contrast. Looking for defects on printed circuit boards requires the ability to see contrasts between the board itself and the silkscreen printing, circuit traces, pads and other errors. Research shows that a green background helps to illuminate these contrasts much better than many other background shades do.
- Cheaper. It costs factories more money to make circuit boards in varying colors. This is because the solder mask is applied through a silk screening process. Every time you change colors, you have to wash the silk screening equipment and start fresh. If one company orders red boards and another company orders pink boards, they will drive up production costs and, in most cases, have to pay the difference.
- Allows for bulk production. Factories can save time and resources by creating as many circuit boards from one panel as possible. Most have figured out how to group boards with similar requirements together to eliminate panel waste. That is why many manufacturers won’t even let you order different colors of certain types of PCBs. To stay profitable, companies must do more with less. So for some boards, it’s green or nothing.
- Performs better. The chemical pigments used in the solder mask affect the quality of the board. Scientists have worked for years to improve these chemicals, and most of their work has focused on green pigments. As a result, green solder masks edge out the competition. For example, no other pigment color can produce a solder mask dam that is as good as those made by green materials. Dams matter because they prevent the formation of soldering bridges, which can hinder PCB performance.
It may not be easy for Kermit the Frog to be green, but, as you can see, it carries a host of advantages for printed circuit boards.
Contact EMS Solutions to find out about our top-quality PCBA assembly and AOI inspection.