Reflow soldering—originating from the drive towards miniaturization and reliability in electronics—transforms the assembly of components on PCBs. Using heat to forge durable connections, this technique has become a cornerstone in manufacturing modern electronic devices. This guide breaks down the steps, advantages, and key phases of the solder reflow process.
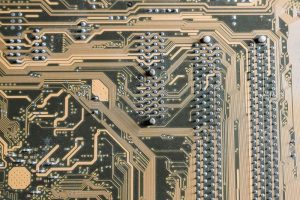
(Tima Miroshnichenko/Pexels)
Overview of Reflow Soldering
In reflow soldering, EMS companies use an infrared lamp to heat up and melt the solder. They only put solder paste on the spots where components need to go on a PCB. Then, the board goes through an oven that heats it just right.
This way, the solder paste melts, sticking the components firmly to the board. Because the heat is controlled, there’s no thermal shock—this means the connections stay strong and don’t get damaged.
What’s Good About Reflow Soldering
- It’s perfect for sticking tiny parts on boards, especially in big numbers.
- It’s a trusted way to solder, making sure parts stay put.
- You can solder just where you need to, no extra.
- It doesn’t shock the parts with sudden heat, so everything stays in good shape.
- It doesn’t need much watching over, making things simpler.
- You end up using just the right amount of solder, no waste.
Four Stages of Reflow Soldering
Reflow soldering involves four key steps:
1. Initial Heating / Preheat
The process kicks off with the board and its components being gradually heated. This step, called ramp to soak, ensures everything reaches the right temperature without heating too quickly, which could cause solder splatter or damage the components. The goal is to hit a specific temperature at a controlled rate, usually not exceeding 2ºC per second, as recommended by the solder paste’s datasheet.
2. Thermal Soak
After initial heating, the board undergoes a thermal soak for 1 to 2 minutes. This step brings all components to the exact temperature needed for the reflow phase. Proper execution of the thermal soak is crucial; it prepares the flux in the solder paste for the next stage, avoiding defects like graping or head-in-pillow.
3. Reflow
In the reflow stage, the temperature climbs to its peak, melting the solder paste to create the solder joints. It’s vital to set the maximum temperature just right—high enough to melt the solder but below the tolerance of the most heat-sensitive component. This balance ensures the solder forms good connections without causing thermal damage.
4. Cooling
The final step is cooling, which must be controlled to solidify the solder joints properly. Cooling too quickly can shock the components, while too slow a rate might not form the ideal metal structure within the solder. Typically, the cooling rate should be between 2 to 4°C per second to optimize the strength of the solder joints and minimize thermal shock.
Reflow Ovens
Reflow soldering is key in building printed circuit boards (known as PCB assembly), especially when you’re dealing with a high volume of PCBs. At the heart of this process are reflow ovens. These ovens have a conveyor belt that moves the PCB through different zones, each with a specific heat setting.
Types of Reflow Ovens:
- Infrared Ovens: These use ceramic heaters to warm up the PCB directly.
- Convection Ovens: These are used to circulate hot air around the PCB. Manufacturers typically use them to heat things up evenly, which is highly crucial for soldering boards on both sides without messing anything up.
Once the soldering is done, the PCBs come out of the oven. Then, they’re ready for the next steps, like adding more parts or checking the final quality.
Adjustable Features for Different PCBs
Some of the newer ovens let you adjust the width of the supports. This means you can simultaneously fit PCBs of different sizes and shapes on several boards. Plus, certain ovens come with fancy fans and systems that keep the temperature just right.
Special Oven Tech
- Nitrogen Atmosphere Ovens: Some ovens use nitrogen to keep oxygen out. This helps reduce oxidation, which can mess with the soldering.
- Vapor Phase Soldering Ovens: These ovens use a special liquid to transfer heat. They’re efficient, lower the chance of overheating, and don’t let oxygen in, which is a big plus.
Common Challenges in Reflow Soldering
Reflow soldering is a sophisticated process, but it comes with its own set of challenges. Addressing these issues effectively is crucial for maintaining the quality and reliability of printed circuit boards.
Solder Balling
Solder balling, the creation of unwanted solder spheres, can cause short circuits. It’s often due to excessive flux activity or rapid heating. Preventing solder balling requires careful control of solder paste application, appropriate reflow profiles, and ensuring the PCB and components are free from contaminants that could affect solder behavior.
Tombstoning
Tombstoning occurs when a component lifts on one end during reflow, causing an open circuit. This issue often results from uneven heating or wetting, which can pull the component upright. Solutions include ensuring uniform temperature across the PCB, optimizing solder paste application, and aligning components accurately to avoid misplacement.
Voids
Voids are air pockets trapped within solder joints, affecting electrical and thermal conductivity. They can form from outgassing of solder paste or components and oxidation. Reducing voids involves fine-tuning the reflow process to allow gases to escape, selecting solder pastes designed to minimize voids, and ensuring components and PCB surfaces are clean and well-prepared.
Quality Control through Inspection
Addressing these challenges involves rigorous inspection, typically through manual checks or Automated Optical Inspection (AOI) systems. Manual inspection allows for detailed examination but can be time-consuming, while AOI provides speed and repeatability. After identifying defects, rework may be necessary to correct issues, ensuring the final PCB meets quality standards.
Conclusion
Overall, reflow soldering is ideal for achieving precise and reliable solder joints in SMT assembly. With its efficiency and effectiveness, it’s the preferred method for ensuring the integrity and functionality of electronic devices in mass production environments.