You’ve got your soldering iron, your components, and a PCB layout that’s just waiting to come to life. You start soldering, but the solder just doesn’t flow the way you’d like—it forms a blob instead of a clean joint.
Enter solder flux. Far from a luxury, this component is a staple for anyone serious about creating robust, reliable PCBs. In this guide, we’ll demystify solder flux and explain the role it plays in streamlining PCB soldering. You’ll also learn about the issues you could encounter should you decide to neglect this critical element.
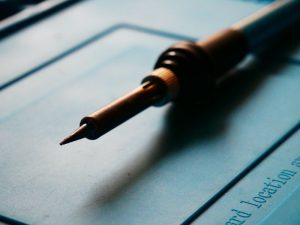
(Vishnu Mohanan/unsplash)
What is solder flux?
Solder flux is a chemical cleaning agent specifically designed to enhance the soldering process. Its primary role is to remove oxidation and other surface contaminants from the metal components involved, thereby ensuring that the solder adheres well.
While solder paste combines solder alloy particles with flux, solder flux itself acts to break down the oxidation barrier that can otherwise prevent a strong, reliable bond between the solder and the metal. Without the use of flux, the risk of forming weak and unreliable solder joints significantly increases.
What is the difference between solder flux and solder paste?
Solder flux and solder paste are two distinct but often confused materials. Soldering flux serves as a general-purpose agent that facilitates soldering tasks like oxide removal, heat transfer, and metal surface tension reduction. It exists in solid, liquid, and gaseous forms.
On the other hand, solder paste is a specialized type of flux. It combines solder powder, flux, and additional ingredients like surfactants. This mixture is typically used in the Surface Mount Technology (SMT) industry for attaching components such as resistors and capacitors to the PCB assembly.
Types of Solder Flux
There are three main types of fluxes:
1. Inorganic Acid Flux
This flux type works exceptionally well with stronger metals like brass, copper, and stainless steel. Thorough cleaning is mandatory after using inorganic acid flux. Any corrosive residues left on the surface can compromise the solder joint. When cleaned properly, the result is a flawless connection.
2. Organic Acid Flux
Also known as water-soluble flux, this type is made from organic acids such as citric, lactic, and stearic, combined with solvents like isopropyl alcohol and water. Organic acid flux excels in removing oxides quickly, outperforming rosin flux in that regard. It also ensures excellent soldering with high flux activity. However, you must remove the residual flux after soldering; otherwise, it can impair the PCB’s performance due to its conductivity.
3. Rosin Flux
Rosin flux stands as one of the oldest types, primarily composed of natural resin from pine trees. Modern formulations mix natural rosin with other fluxes to optimize its performance. Rosin flux is versatile—great at removing oxides and foreign particles from metal surfaces. While liquid rosin flux is acidic, it becomes inert when cooled, meaning it won’t harm your circuit board unless heated to a liquid state again. For added safety, it’s advisable to clean off the rosin flux residue, particularly if you intend to apply a conformal coating or are concerned about the aesthetics of your PCB.
How to Use Solder Flux
Integrating solder flux into your PCB assembly isn’t just a best practice—it’s essential for robust, reliable connections. Here’s how to do it right:
Step 1: Pick Your Flux
First, examine your PCB. Is it single-sided, double-sided, or multilayer? What soldering method will you use: Wave Soldering, Hand Soldering, or SMT? Your answers guide your choice of flux, helping you nail down the one that works best for your project.
Step 2: Clean Up
Before you even think about soldering, get rid of all surface impurities. Swipe a suitable solvent over your PCB pads and component terminals to remove unwanted particles and oxides.
Step 3: Apply the Flux
With a clean surface, the next step is applying the flux. Use a steady hand to spread a uniform layer over the areas you’ll solder.
Step 4: Heat Things Up
Time to power on your soldering iron. Let it reach its optimal operating temperature. Then touch the tip to the flux-covered pads. This step activates the flux and clears the area of remaining oxidation, setting the stage for soldering.
Step 5: Execute the Solder
With an activated flux layer, it’s go-time. Introduce the solder wire to your joint and make sure it flows smoothly to cover both the PCB pad and the component leg. The goal? A solid, unshakeable connection.
Step 6: Clean the Scene
Soldering is messy. Leftover flux residue can undermine the performance of your PCB. For non-“no-clean” fluxes, this cleanup is non-negotiable. Use an appropriate solvent to remove all residue, ensuring a clean and functional PCB.
As we wrap up, let’s underscore the indispensable role of solder flux in PCB assembly. It’s not just a cleaner—it’s a performance enhancer. By removing oxides from electrical contacts and prepping the PCB surface, solder flux sets the stage for a robust metal-to-metal bond.
When coordinating with an EMS provider, remember that the right flux can make all the difference. Your choice will impact everything from material compatibility to long-term reliability. Choose wisely to ensure your soldering creates a durable and high-performing PCB.