The box-build assembly process, also known as “system integration,” is the process of building a device which includes the printed circuit board, the enclosure, with the installation of wires and cables, as well as other components. It can range in size from a small box with a PCB assembly inside, to a cabinet of equipment complete with robotic arms, pneumatics, and other electronic parts.
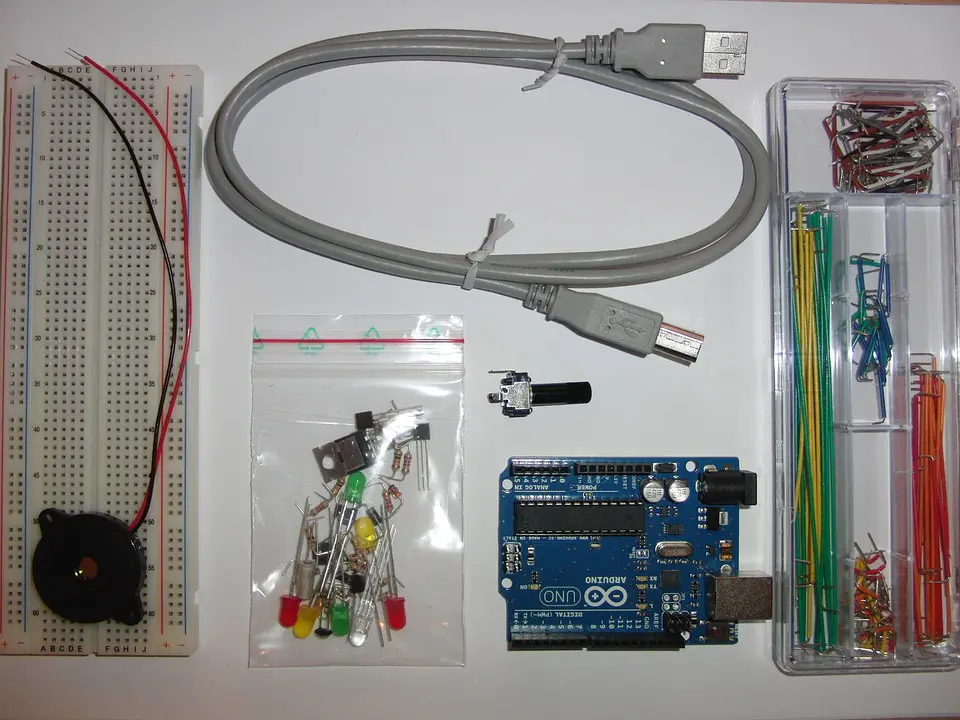
(Pixabay / redcctshirt)
System Integration
The assembly process includes system level assembly, product assembly, and packaging. During these processes, there are other intermediate or repetitive tasks, including sub-level product assembly, testing, and software loading. Post-assembly processes include aftermarket service, depot repair, warehousing, order fulfillment, and tracking. The system integration starts with requirements, models, and a shopping list of materials. It ends with a working, finished product, packaged, labeled, and ready for shipping to the end user.
Requirements
Box build depends on certain processes and materials. Prior to manufacturing, there should be a complete bill of materials (BOM). If the needed supplies are not available, these should be sourced out prior to the start of manufacturing, and any difference in assembly should be ironed out. Major items like the PCB can be sourced out by the owner. Smaller items can be sourced by the PCB assembler. These include consumables like ties, washers, screws, nuts, and bolts. The BOM is also necessary to forecast the supply requirements. Delays due to shortages or lack of parts can be avoided with a careful study of the BOM prior to assembly.
A 3D CAD model and a sample unit aid the assembly process. The assembly makes use of the 3D CAD model in designing the process flow. Part of the CAD model is the tagged parts. These parts are supplied to the assembly line where needed. If there is a need for clarification, the sample unit would come in handy as it shows the actual placement of parts and can be deconstructed if necessary.
Although the dimensions and the weight of the finished product are in the specifications, it is still critical to relay this information to the assembler. This will allow them to prepare for handling, storage, and shipping of the finished goods. Packaging is also usually dependent on the size and weight of the product.
Testing
Product testing should be considered as a project in itself. This includes random testing and electrical safety testing. It has to be tested between the time the product is finished on the assembly line and the time the end user receives it. Not all products need to be tested, but it is still necessary to have an inspection for the individual items.
Software testing is a separate activity with multiple levels. The software should at least be tested on the component alone. With electromechanical devices, it might be necessary to test the whole assembled product to see if it meets the system requirements. It is necessary to capture any software issues before the full volume assembly. This may lead to changes in the components or the software, resulting in delays. However, it is less costly than returns and product recalls.
Outsourcing Assembly
Sourcing out box build to an assembler is a common practice for plenty of manufacturers. They rely on the experience and expertise of these third-party assemblers to ensure that their products are made to standards and specifications. It also leapfrogs the need to build self-owned manufacturing plants and recruit people for the job. However, remember that you must communicate well with the assembler so that they fully understand the product and requirements necessary for successful production.