No matter how perfect your manufacturing plant, it is bound to hit some roadblocks during its lifetime. Some of these roadblocks are caused by nature, whereas others occur due to manufacturing errors. Surface Mount Technology (SMT) is one of those processes that experiences such errors, but the vast majority of these errors are avoidable.
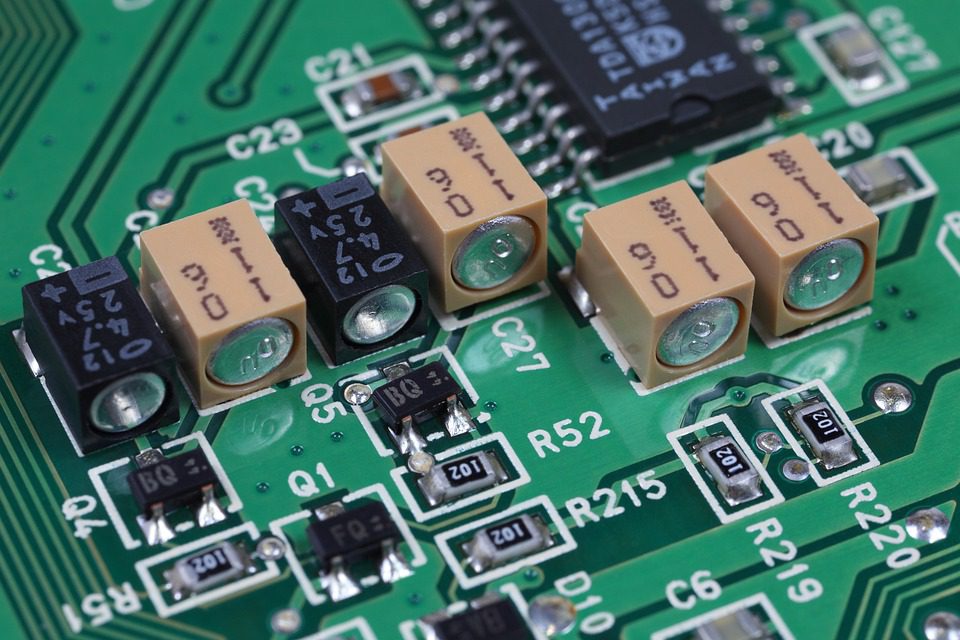
(Pixabay / nanoslavic)
Today, almost all commercially manufactured electronic equipment relies on SMT, and for good reason. The use of SMT allows a lot more to be installed in a much smaller space. However, errors in SMT can produce faulty boards that might not deliver the desired result. This makes it critical to manage each step of the process.
With proper management, you can overcome all these issues and operate at maximum capacity. Here are some common SMT errors and ways to fix them:
Solder Bridging
Soldering that causes bridging across two electrical conductors that should not otherwise be connected results in electrical shorts. The main issue arises in the solder paste printing process where it generates excess solder. Print or stencil arrangements can get off sometimes and cause wrong soldering on the PCB pad.
High temperatures, moisture and cold slump also build the bridge on the pad. Solder paste in the pre-heat stage can cause bridging as well. Therefore, incorrect positioning of stencils, component placement pressure and an extra moist environment must be avoided. The solution to this is to reduce stencil aperture dimensions by 10-15%. You could also try reducing the thickness of the stencil to see if it makes any difference.
Solder Balling
Solder balling is the development of tiny ball-like particles on the board. These particles isolate from the main solder body and may cause electrical disruptions. Big-sized solder balls can make a bridge between two components and lead to functional issues in the circuit. Moisture is the biggest culprit in this case because it saturates during the reflow process and creates these solder balls.
The first step to prevent this issue is to create a coarse powder rather than fine powder because the latter can slump easily. Any humidity and moisture in the facility should also be reduced so that the manufacturing process yields maximum quantity and quality. Once these factors are in check, clean the bottom of the stencil as the smear may also build solder balls.
Tombstoning
This error is also known as the “Manhattan Effect.” Tombstoning happens when the component rises from one end as if it’s rising from the dead. This typically occurs when the chip is partially or completely off the board. Only one end of the chip is soldered, which causes vertical or horizontal lift.
Uneven heat distribution is one of the causes behind the lift as the solder melts at different rates. One side reflows quicker while the other takes longer to melt. Temperature and humidity differences in the solder paste can also cause component misalignment. Improper placement of components before heat reflow can also cause unbalanced soldering.
Ideally, the component must touch 50% of both sides to avoid imbalance. Minimizing exposure to heat and humidity should also help.
Insufficient Solder
When the amount of solder paste is less than operating design, it creates a fillet on the component leads. Also, stencil apertures sometimes accumulate dried solder paste which blocks the aperture. All of this leads to insufficient pressure being applied during the printing process. It may also result in the scooping of the paste on the pads. The low viscosity of solder paste is another cause of this issue.
If there is a large stencil aperture, consider dividing it into smaller apertures and keep tabs on it to avoid pressure buildup. Clean the stencils at intervals and ensure that there’s adequate support on the board.
De-Wetting and Poor Wetting
De-wetting is a solder joint condition where the “fluid solder” is not properly adhered with one of the available components. One of the reasons for this is a lengthy soaking time in the reflow process. Reducing the overall profiling time before the reflow process can help prevent de-wetting.
Some solder materials can also cause poor wettability when placed on copper. This is why surface finishes mostly go on conductors. Silver, tin and ENIG surfaces respond the best and help avoid wettability. When peak soldering temperature is in the right range, wettability further decreases. The temperature must be checked with a test sample before full-scale production kicks off.
Circuit Board Damage
The movement of nozzles might build electrostatic charges on their tips, which can damage the circuit board. It is a common error that damages the components when they’re being placed. Manufacturers have to take caution when using these nozzles and during the pick-and-place step.
Choosing the right nozzle supplier can put an end to this mess and enable smooth manufacturing. However, with so many manufacturers out there, it can be challenging to choose the right one. Ask about the materials they use and how they react with electrostatic charges. Check reviews from past customers. Consider other factors like warranty, exchanges and production capacity as well. If your supplier is not stocked ahead of a big order, it might be best to contact another company.
Have more questions about SMT or surface mount assembly issues? Contact us today.