Inspecting PCBs is a tedious but necessary process. All electronic boards have to be inspected for quality assurance purposes. Manual inspection can be a lengthy process. In fact, it’s faster to manufacture a board than to manually inspect it for errors. For this reason, using automated optical inspection (AOI) machines is a popular choice for many companies. They can inspect products thoroughly without the heavy amount of time required for manual inspection.
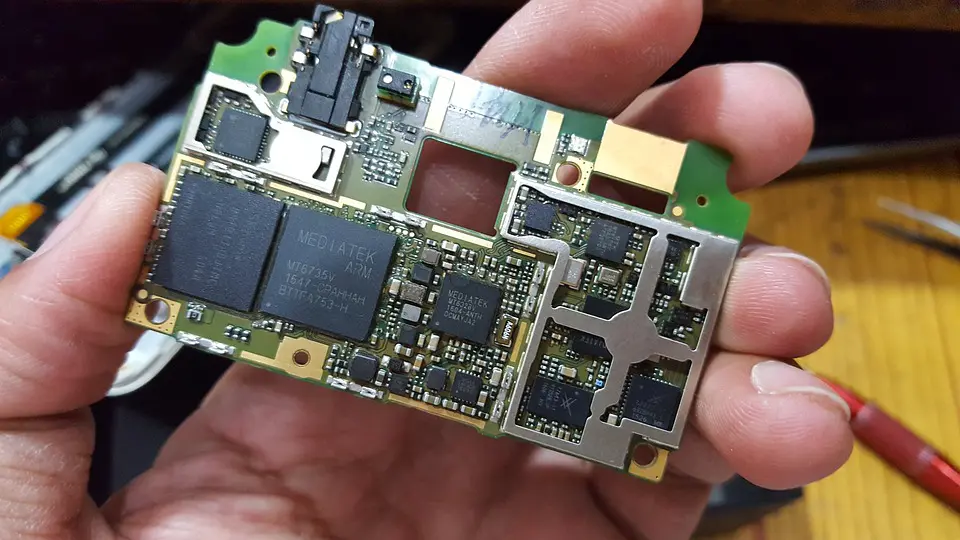
(Pixabay / pakfones)
Saves time
An AOI machine uses a high-resolution camera connected to a computer, which tells the operator what errors it finds. Visual inspection would normally take an extensive amount of time per board, while AOI can do the job in just a few minutes. Even though the operator validation requires a few extra minutes, this is still a quicker method than the manual alternative. Rapid inspection and verification means that the assembly line can move at a faster clip.
Early and thorough error detection
AOI is high-precision and can be fine-tuned to catch smaller defects. The operator can stop the whole assembly process when the errors are too numerous or significant. New technologies integrate the AOI with the Surface Mount Technology (SMT) assembly line. With these technologies, the operator can alert the assembly line when an error occurs, and the error can be fixed immediately. Catching defects early leads to less time spent on reworking the line.
Greater accuracy
In today’s manufacturing assembly, the PCBs are more complex, and the errors are smaller in terms of size. Human operators may not be able to catch these errors due to their small size. With the larger volume of inspections and the smaller sizes of possible errors, fatigue sets in much quicker. In comparison, an AOI does not get tired and can run 24 hours straight, if needed.
More consistency
The automated process yields more consistency for the inspection process. With hundreds of thousands of assembled boards passing through the line during a production run, inspection has to be consistent. The AOI process assures this consistency because the board is placed for inspection at the same place every time and all components and parts are systematically inspected without omissions. This helps lessen the strain on the operator as well as the whole production process.
Frees up workers for other duties
Catching errors early leads to less rework for the whole construction process. Products can pass through the facility more efficiently and move to the next step much faster. Because the AOI machine is handling a lot of the heavy lifting with routine inspections, human operators can focus on fixing the errors discovered by the AOI. With less work strain, they are free to repair flagged boards and enhance overall quality assurance.
The AOI system is not foolproof, and it won’t detect all defects. Proper programming makes all the difference, and it’s also important to fine-tune the process over time. Even with its high degree of accuracy, an AOI system was not meant to replace visual inspection. However, with the combination of an SMT assembly line, an AOI system, and an experienced operator, the chances of catching and resolving defects quickly and efficiently are very high.