Electromagnetic interference (EMI) has been plaguing PCB designers since forever. EMI is electromagnetic energy that disrupts an electronic device’s signaling via induction or radiation. Too much EMI can result in a damaged or defective item.
EMI radiations from a device may also interfere with other devices in the vicinity. Imagine how annoying it would be if your neighbor’s cellphone caused interference in your audio device. PCB designers must ensure that EMI is kept to a minimum and the signals left off are compatible so as not to cause any interference.
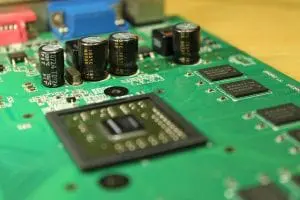
(Pixabay / CompileIdeas)
Although it might not be possible to eliminate EMI completely, there are some techniques you can apply to reduce the electromagnetic interference in your PCB design.
1. Ground Plane Tips
The ground plane is your first weapon against EMI since every circuit needs a ground to function. Randomly connecting the circuit board’s components to ground points is never a good idea. To reduce EMI using ground design, follow these steps:
Utilize solid planes
A solid plane is a perfect choice, especially in a multi-layered PCB. They provide lower impedance levels that are impossible to achieve with hashed and copper-thieving ground planes.
Adopt caution with split planes
Planning to split ground planes? Make sure to do it carefully and for a good reason, such as to separate the digital and analog grounds to prevent noise coupling (as ground planes can serve as slot antennas and radiate).
Aim for shorter return paths
According to Faraday’s law, when a signal takes a longer path to return through the system ground, it develops a loop that creates a radiating antenna. Hence, long return paths often contribute to mutual coupling leading to crosstalk. Keeping return paths as short as possible is the key to minimizing the loop area and achieving better electromagnetic compatibility.
Leverage decoupling or bypass capacitors
If the design calls for decoupling or bypass capacitors, make sure to connect them to the ground plane to reduce the size of the loop, which, in turn, would help minimize the return current.
2. Shielding
Shielding the PCB’s switching-mode power supply (SMPS) with metal can help lessen EMI’s effects. Designers can do this by placing noise-generating sources in the SMPS inside a grounded metal/conductive housing. As you do this, make sure the only interface to external circuits is via in-line filters. The alternative is to encase the whole PCB to secure against EMI from external sources.
Some PCB models can also include low pass filters to prevent high-frequency sound from components. The aim is to suppress the noise and enable the current to flow on the return path without distortion. Additionally, you can consider shielding the cables that carry digital and analog currents to the ground at the back and front to suppress EMI interference.
3. Trace layout
Traces are those conductive paths on a PCB that contain flowing electrons as the circuit is active. This means they are only a cross or bend away from causing a radiating antenna. Various issues could arise if the designer doesn’t arrange the traces properly. One best practice is to avoid 45-to-90-degree angles for traces, vias, and other components. That’s because capacitance rises when traces span over 45 degrees. This causes the characteristic impedance to change, resulting in reflection transmits EMI. The solution is to round out traces that have to switch a corner or route them through a couple of angles of 45 degrees or less. Another important measure is to separate high-speed traces from low-speed signals because close proximity could lead to interference. This should also be done for digital traces and analog signals.
When it comes to vias (important for taking advantage of multiple layers while routing), it’s crucial to understand that they will add their own capacitance effects and inductance to the mix, potentially causing reflections because of characteristic impedance changes. Plus, they also enhance trace length that has to be equal. So, where possible, avoid utilizing vias for differential traces. If vias are a must, you can use an ‘oval anti-pad’ shared by the two vias to minimize parasitic capacitance. Using them in both traces can also help compensate for the delay.
Lastly, consider keeping the minimum spacing between traces. Normally, two high-speed signals flowing in parallel generate EMI via crosstalk, where one trace is the victim while the other is the aggressor. The latter influences the former trace through capacitive and inductive coupling, developing backward and forward current in the victim trace. Using mind spacing between the traces can help reduce the crosstalk. Ideally, you should separate traces by 2x the trace width to create enough distance between the two parallels.
Conclusion
The above steps should help you minimize the EMI in your printed circuit board. Besides these measures, you can explore the option of using a PCBA company like EMS Solutions to help minimize electromagnetic interference. We know how to arrange electronic components in a way that minimizes each piece’s EMI impact. Plus, we segregate sensitive components based on the signals they are functioning on, such as digital, analog, low-speed, high-speed, power supply signals, etc.
Moreover, when you use a well-rated electronics services company like EMS, you will be dealing with professionals who are aware of the measures required to reduce noise generated by ICs switching current at high frequency. The technique of decoupling capacitors near the IC power pins will enable them to reduce power rail noise. And once all of that is done, they will test the PCB and the device for radiated and conducted emissions plus radiated and conducted susceptibility based on the CISPR standards. Low EMI is only possible with good PCB design techniques, where a designer can minimize noise while securing the circuit against its adverse effects.