Printed circuit boards of various sizes can be found in every type of electronic device, from your television and iPad to your computer and mobile device. Their main purpose is to form a connection between different components. Whether you realize it or not, your devices would be completely useless if their PCBs’ design and fabrication were not executed correctly.
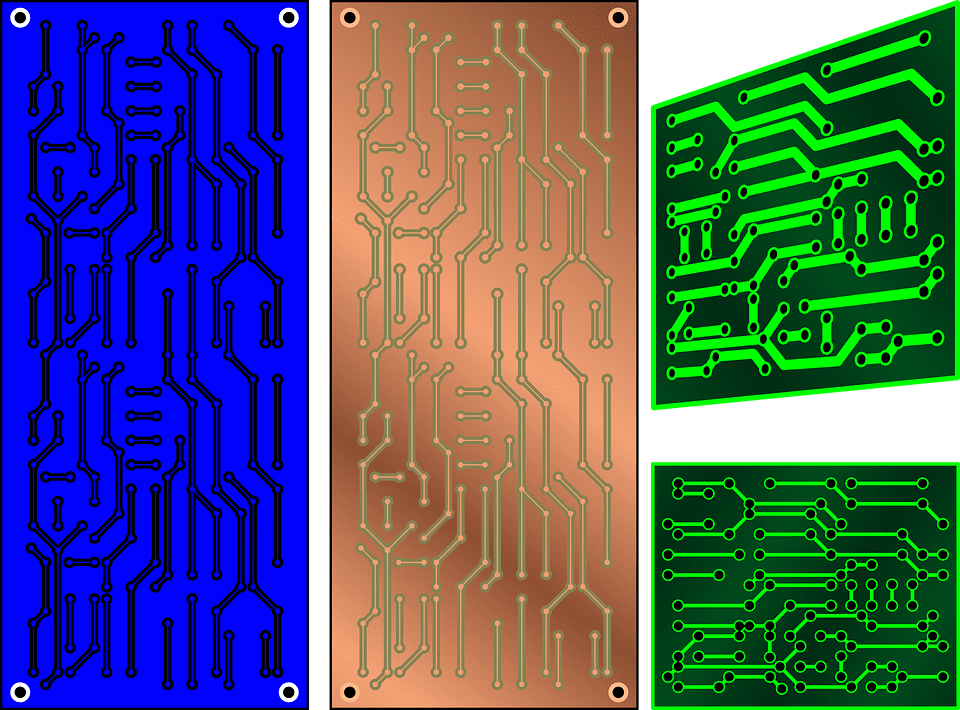
(Pixabay / OpenClipart-Vectors)
But even as commonplace as they are, PCBs are still something of a mystery to many people. For one, they’re buried inside electronic devices and equipment where few people actually see them and the amazing work that they carry out on a daily basis. Perhaps this is why there are a number of myths floating around about PCBs that need to be dispelled. Unless you create printed circuit boards yourself, you might give in to the popular misconceptions. With that in mind, let’s look at some of the top PCB myths so that you can get your facts straight and gain new perspectives on these little electronic wonders.
1. The Same Design Rules Apply to Every PCB Assembly
Though the majority of multi-player boards comply with the most common amount of layers, i.e. 4, 6, 8, or 10, it doesn’t mean that the same design rules apply to every printed circuit board. Some boards require the maker to keep base material stability in mind, while others need to account for the reduction of stress. To prevent design-related pitfalls, it’s a good idea to work with reliable PCB assembly providers from the get-go.
2. Components Can Be Fixed Anywhere On the Board
This is false, as each PCB component needs to be housed in a certain area to ensure it functions with the electrical scheme of the board. A common layout error is to neglect the height of the component and its placement in comparison with the board case or neighboring circuit boards. Components near the schematic should also be in close proximity when it comes to the layout. Overall, every component needs to be strategically placed on the board for them to work at maximum efficiency.
3. Grouping Similar Parts in a PCB is a Smart Use of Space
On paper, it may seem like grouping similar PCB parts in a common space is the best use of that area, but as we’ve previously discussed, the parts should be placed in relative proximity to their space in the schematic. This is to limit the distance that the signal should travel and eliminate unwanted routing on the board. This is also applicable to microcontrollers and the accompanying caps. Reducing the trace lengths between the controller and the cap decouples the power supply’s noise, producing a better outcome. Therefore, it’s essential to take a logical approach when it comes to the grouping of your PCB parts.
4. Every Part Published in a Library Is Suitable to Be Placed On a Layout
Unfortunately, not all parts published in the library are alike. It’s common to find discrepancies between the technical datasheet and the footprint of PCB components. It could be a matter of orientation, pin assignments, or even the size. While everything may look good at the layout phase, the physical part may not fit into the component’s footprint, resulting in spin revisions and delays. The best way to address this is to match the parts with the datasheet. This is critical, as it only takes one bad part to demolish the work.
5. Copper Tracks Always Need to Be Routed at a 45-Degree Angle
While many PCB engineers ensure that every corner in their design is 45° before they send the layout for fabrication, this doesn’t have to be the case. Advancements in PCB design and routing tools have made it possible to use whatever angle is necessary for your circuit board’s needs. This means the copper tracks can even be routed at a 90-degree angle to prevent acid traps and other design flaws (except in special circumstances, where the tracks need to be precisely routed at a 45-degree angle).
6. Minimum Trace Widths Can Accommodate All Traces in a PCB Design
Not true. High-speed lines often have impedance needs that will govern the widths of such traces. These requirements need to be taken into account before the routing happens. In addition, pay attention to the existing load of power nets before you proceed with the routing. Traces with a huge current load need to be sized right (large enough) so that they can transfer the current without heating up. Fortunately, calculations like these can be simplified with the help of a trace width calculator.
7. There’s No Difference Between the Layouts for Production and Prototyping
Based on the goal of your design, you may opt to incorporate various types of components in the layout. For a show-of-concept or a prototype, for instance, you may go with through-hole parts for as many components as possible. Why? Because they’re affordable and simple to solder to the printed circuit board. However, you may need to choose surface-mount parts for production design. That’s because through-hole parts are expensive to source and assemble in value and could significantly increase the overall expense (due to availability delays, the large board size, etc.). Additionally, the production cost can be minimized through the downsizing of unique parts on the BOM (bill of materials).
8. PCBs Cause Harm to the Environment
Some individuals think that manufacturing PCBs and working with printed circuit board assembly providers is not environmentally sound. While a lot of circuit boards do end up in landfills after faulty gadgets are thrown away, this doesn’t have to be the case. Many stakeholders have begun to recycle device components. They’re telling consumers to send in the electronics they don’t need any more rather than throwing them in the garbage. Also, printed circuit board engineers are actually in the process of producing biodegradable boards. All of that means PCBs aren’t as bad for the environment as you might think.
With that, we’ve debunked the top PCB myths that continue to mislead PCB users. The best printed circuit board assembly companies know the industry in and out and will embrace the highest standards in manufacturing to churn out the most reliable boards, with each one verified by rigorous testing. Contact us at EMS Solutions to learn more.