Traceability has a crucial role in the life cycle of printed circuit board (PCB) manufacturing. Each PCB carries essential data: its origin, batch, and production date. This information forms the PCB’s identity.
In demanding production environments, these details are invaluable. They keep each PCB’s story intact — from the earliest stages of production to its final destination. Manufacturers rely on this level of detail for efficient quality control and absolute accountability in an industry where errors have no place.
In this post, we focus on the importance of traceability for PCB assemblies. We’ll look at how it’s essential for managing the complexity of modern PCBs, especially as they become smaller and their assembly more intricate.
Benefits of PCB Traceability
PCB traceability offers a raft of benefits, making it a must-have in a PCB assembly company. First off, it simplifies identifying each board’s origins and journey. With traceability, manufacturers can quickly trace a PCB back to its production batch. This pinpoint accuracy is crucial when a single part fails. They can swiftly investigate if similar issues might affect other parts from the same batch.
Then there’s the safeguarding of performance. Traceability acts as an early warning system. It flags defects before they escalate into bigger problems. This proactive approach prevents potential failures that could disrupt entire systems.
Quality control also gets a major boost from traceability. It allows manufacturers to trace faults back to their source. With this information, they can fine-tune their processes. The result is a consistently higher-quality product rolling off the production lines.
Maintenance becomes more efficient, too. Technicians can quickly identify and replace problematic components thanks to traceability. This cuts downtime and keeps production humming along.
Moreover, products become more reliable. Manufacturers gain the insight to refine their PCB designs and processes. They base these improvements on the production history of each board, leading to sturdier, more dependable products.
Popular Solutions for PCB Traceability
PCB traceability relies on several different methods. Each one has unique features:
Barcodes
Barcodes are a straightforward solution. Manufacturers print them on PCBs or packaging. They store crucial information like serial numbers and production dates. Scanning these barcodes quickly reveals all the necessary details.
QR Codes
QR codes add another layer of detail. Printed on the PCB or its packaging, they can contain a wealth of information, including the PCB’s serial number and manufacturing date. Scanning these codes gives instant access to this data.
Radio-Frequency Identification (RFID)
RFID tags bring advanced tracking. They’re inserted in PCBs or their packaging. Using radio waves, these tags allow for automatic, fast identification, simplifying the tracking process.
Laser Marking
Laser marking is all about permanence. It etches identification data directly onto the PCB or components. This method ensures the markings last throughout the PCB’s life.
Unique Identifiers
Giving each PCB a unique identifier, like a serial or component number, simplifies tracking. It makes it easy to follow and identify them through the production and supply chain.
Data Matrix Codes
Data matrix codes are great for small spaces. They store more information in a smaller area than QR codes. This makes them ideal for compact PCB traceability.
Choosing the right method depends on specific needs. It varies based on industry requirements, PCB size, and budget. Each approach has strengths that enhance PCB traceability.
Streamlining PCB Assembly with Integrated Traceability
In PCB manufacturing, integrating traceability into the assembly line proves beneficial. Tracking labels, which blend into Surface Mount Technology (SMT) lines, function like core components. These labels, akin to resistors or capacitors, merge with the system. This isn’t an add-on; it’s part of the process.
Here, precision takes center stage. Pick & place machines manage these labels with high accuracy. They ensure each PCB is distinct and traceable, a necessity for later production stages.
Choosing Polyimide for Durable PCB Labels
Polyimide often tops the list of durable PCB labels because of its ability to thrive under tough conditions. Its resilience to high heat and aggressive chemicals keeps labels clear and readable through processes like soldering and cleaning. Here are some of its properties:
- Chemical toughness: Polyimide stands up to harsh cleaning agents.
- Heat resistance: It endures extreme temperatures, essential in high-heat processes.
- Readability: Polyimide keeps labels legible from start to finish.
Polyimide Labels: Changing the Landscape in High-Stakes Industries
Polyimide labels are revolutionizing PCB assembly, especially in critical industries like aerospace and medical devices. These labels excel in handling high temperatures, ensuring traceability throughout the manufacturing journey. In sectors where mistakes can have major consequences, the precision and reliability polyimide brings are invaluable.
Precision and Safety: The New Norm in PCB Manufacturing
In environments where precision is paramount, opting for polyimide labels speaks volumes. This choice goes beyond compliance; it reflects a dedication to exactness and safety. It’s a commitment to excellence in high-tech manufacturing, focusing on producing products that are not just functional but also safe and reliable. This approach highlights the importance of detail-oriented, traceable manufacturing.
Traceability is key to enhancing PCB production. Manufacturers that diligently track every aspect, from tests to certifications, gain comprehensive process knowledge. This insight fosters ongoing improvements in both quality and functionality of their PCB products.
Video
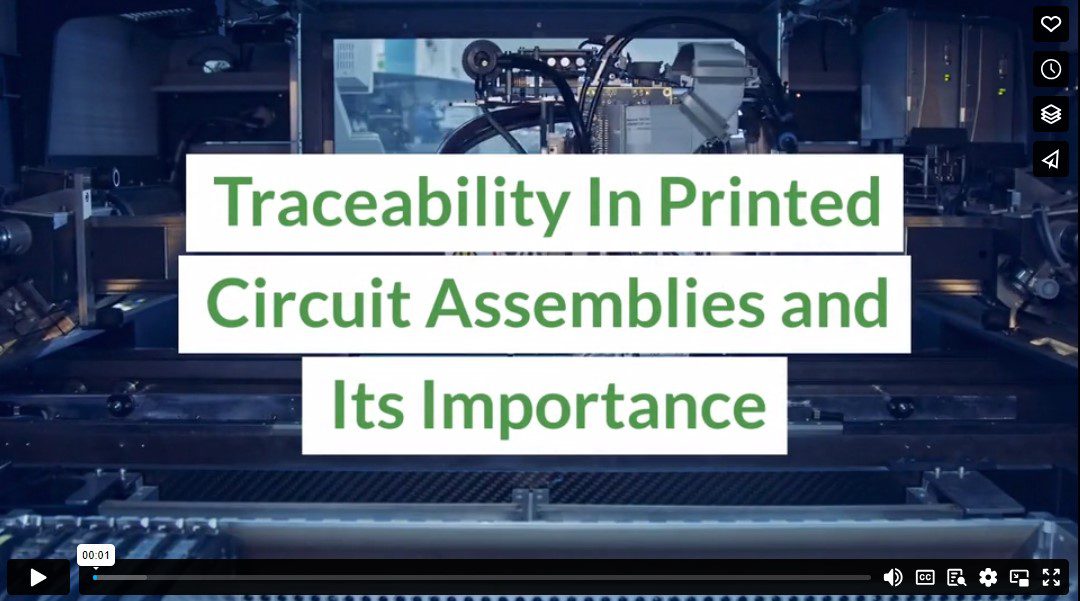
Infographic
PCB traceability is vital in its manufacturing. Each PCB has its identity through its origin, batch, and production date. There are various traceability methods, each with unique features. Find out more in this infographic.