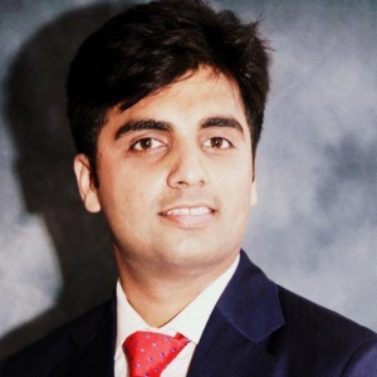
Shalabh Singhal
Curbing the Impact of Logistical Issues
With the imposition of trade restrictions in the wake of the COVID-19 pandemic, manufacturers across the U.S. have and are still facing numerous challenges. Some manufacturers have temporarily or permanently shut down their production houses to prevent risking the lives of their workforce and even control the spread of the dreadful virus. Many others engaged in manufacturing essential goods such as medical equipment, chemicals, medicines, food items, daily necessities, etc., finding ways to overcome the challenges to provide basics to the general public amidst the havoc.
Of the many challenges that these manufacturers are facing, supply chain and logistics top the list. To curb these challenges, here are viable responses from the manufacturers.
o Excessive Shipping or Transportation Time
Since goods took longer than usual to reach the market and have a short lifespan, they were either expired or reached their expiry date. Hence, to reduce their losses, manufacturers decided to either limit their supply to the market or close the production of goods with shorter shelf-life products until things normalized.
o Product Hold-ups at the Warehouses
With high demand for numerous goods amidst low production volume and even fewer buyers to take the products to the market, many manufacturers tied up with either the government or large distributors to ensure zero wastage and no hold-ups in the warehouses.
o Increase in Demand vs. Decrease in Supply
With limited production and a disrupted supply chain versus an increase in demand for many essential goods, manufacturers carefully planned their production cycles to ensure that they could meet the demand to the extent possible.
o Delayed Arrival or No Raw Materials
This was one of the biggest challenges for procurement officers. To ensure the manufacturing units received an uninterrupted supply of raw materials, they switched to local providers to fulfill their demands.
o Higher Shipping and Transportation Prices
Shipping and logistics companies were bound to increase the cost of transportation due to the limited availability of [employees], which, in turn, led to an increase in the cost of final goods, which consumers had to bear.
Diversifying Their Supply Base
The coronavirus pandemic has completely changed the world, and even after it subsides, there will be a distinct difference in how the world will operate. The areas that were affected first were regions at the heart of numerous global supply chains exposing major weaknesses in the production strategies and logistics network of firms all around the globe.
In the U.S. especially, where domestic production is low, and their dependence on various supply chains that are far from them highlighted the vulnerabilities that can arise from the lean manufacturing that is practiced on the continent. U.S. manufacturers had to come up with ways of dealing with supply chain issues, and one of these was by diversifying their supply base. For many, it proved to be a monumental task because managers were tasked with establishing strategies that somehow localize or at least bring a substantial amount of the production of key goods closer home.
However, reducing the dependency on the supply chains of certain goods can often be tricky since some goods require sophisticated machinery that is not available everywhere. Manufacturers had to create transparency on multitier supply chains, establish a list of critical components, identify alternative sources, and be flexible on transportation, where required. It also led to many of them having to manage capital by running stress tests to reduce the risk of financial impact.
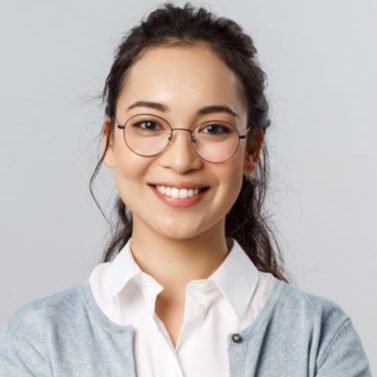
Eden Cheng
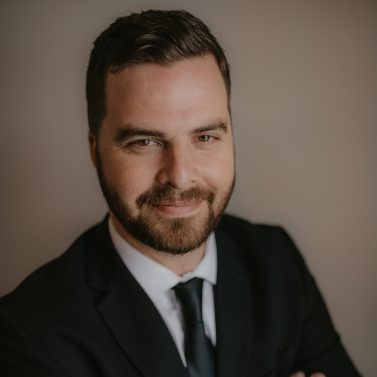
Alex Meyers
Finding New Ways to Ship Products
The highest levels of financial impact were directly related to logistics disruptions. The essential business that operated during Covid-19 with the ability to digest their operational analytics, could predict where issues were arising and react quickly with solutions that could hedge their potential losses.
Leaning on direct carriers and finding new and innovative ways to ship products were the only ways to avoid unsurmountable costs and disruptions. In 2020 if you were relying on too many touchpoints in-between your inventory and your end-user, then the unreliability and cost would have been unsustainable and ultimately destroyed your bottom line or the business itself.
Source Materials from Different Countries
We are in the multimedia industry, so we have been affected by the unavailability of raw materials for our products. A good workaround that we did was to outsource from other Asian countries, which were able to send products immediately. We were able to outsource raw materials from China and Indonesia, so our production was able to continue with just a bit of delay.
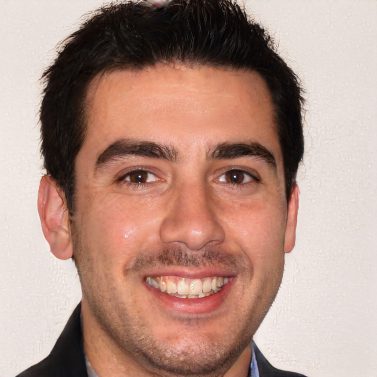
Willie Greer
This is a crowdsourced article. Contributors' statements do not necessarily reflect the opinion of this website, other people, businesses, or other contributors.