Actuators and sensors are two vital components of embedded and electronic systems. Actuators form a link with the output ports while sensors connect to the input ports of a given system. These components are used to facilitate efficient output in many real-life applications such as process control systems in nuclear reactors, home automation and security systems, and aircraft flight control systems. Both actuators and sensors play a significant role in condition-based maintenance. Plus, they serve as a mediator between the electronic system where they are embedded and the physical environment.
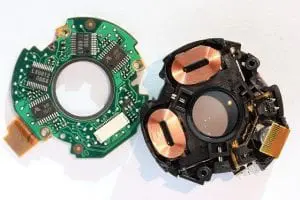
(Pixabay / 2427999)
Although they frequently work together, actuators and sensors differ from each other in function and purpose. Below is an in-depth definition of each component and a list of areas where they act differently.
What Is an Actuator?
An actuator is a device that takes an electrical signal (control input) and blends it with an energy source to create movement. Typically, actuators receive control input in the form of electric current or voltage, but they can also accommodate hydraulic fluid, hydraulic or pneumatic pressure. The device then uses the control signal to generate a change in the physical system via generating motion, heat, or force. Popular examples of actuators include hydraulic cylinders, comb drives, and electric motors. A stepper motor where an electrical pulse drives a motor is also a common example of an actuator.
Of course, electric actuators receive their power from an electronics circuit. Some examples of this actuator type are servo motors, stepper motors, and AC motors. Then there are hybrid actuators that have electric controls integrated in addition to the current elements. You’ll find these actuators in advanced applications like robots and IoT devices.
What Is A Sensor?
A sensor is an electronic instrument that translates real-world parameters into electrical signals. It can take the shape of a basic switch or be a more complicated sensor depending on the application. Sensors are integrated in a way that they can interact with the surrounding environment to sense the input energy. A transduction element is used to convert this sensed energy into a more consistent form.
To understand their function, let’s say you need to adjust the altitude of an aircraft, and for this purpose, you need to develop a control system for it. Just fixing the fuel throttle won’t get the job done – you need to adjust it for each touchpoint when there’s a variance in speed, such as when the airplane goes down or up. Using a sensor can help you measure the speed and convert it into a readable form for the control system. Based on the measured speed, the connected electronic device will adjust the throttle.
Sensors exist in various forms and shapes. Here are some of the common ones:
- Biosensors – are typically used in electronical technology. Medical devices use them to analyze proteins, cells, and more.
- IR sensor – helps measure distance by estimating the depth of IR reflection.
- Temperature sensor – converts temperature changes into electrical signals with the help of the thermodynamic principle.
- Image sensor – leverages CMOS (Complementary Metal Oxide Sensor) technology to identify and transfer the details used to create images. You’ll find these sensors in surveillance and consumer electronics devices.
- Motion detectors – are based on radar, microwave, and ultrasonic technologies. They generate waves and use echo to determine nearby motion and obstacles in their pathways.
Key Differences Between Actuators and Sensors
Here are the main differences between the two components:
- Sensors identify events or alternations in the environment and transmit this information to other devices, while actuators are machine components that control the moving mechanism.
- Sensors are placed at the input port, while actuators are fixed at the output port.
- Sensors measure both continuous process and discrete variables. In contrast, actuators help impel the parameters of these two processes.
- A sensor will convert any physical attribute to a control signal, while an actuator does the opposite, changing the control signal to physical action.
- Actuators’ industrial applications include valves, couplings, and operating dampers. On the other hand, sensors are used to analyze asset vibration, fluid level, or pressure.
- Some non-industrial devices that utilize sensors include cameras, microphones, and home security systems. Other devices like motor controllers, LED, and lasers use actuators.
- Actuators and sensors often depend on each other to perform certain tasks. Where both are present, the actuator relies on the sensor to power its function. If one or the other fails to work correctly, the system will malfunction. In most instances, either the actuator triggers the action, and the sensor transmits the signal, or actuator movements help the sensor send out alerts.
PCB Design Considerations with Actuator and Sensors
When designing apps involving the two components, you may need to consider design coloration with project engineers or an electronic services company. Although you have restricted control over the physical characteristics of the parts, you’ll need to be cautious with the electrical traits of actuators and sensors. For instance, temperature sensors may return a serial communication interface or raw analog signals. And both will require different design strategies for software and hardware. Plus, the option of driving an AC or stepper motor means integrating various types of driver circuits. Hence, it’s important to be attentive and choose the correct parts from the initial step.
It’s also crucial to factor in the system’s fail-state condition when working with moving components. For instance, an industrial HVAC system requires that the application designer leaves only specific valves open at a single time. An error in judgment could result in a catastrophe because of the high-pressure air movement. Therefore, a PCB designer needs to gain a thorough and clear understanding of the system’s workings and the fail-safe condition of the mechanisms. To help maintain the system when the system power malfunctions, a designer can consider choosing a NO (normally open) or NC (normally closed) to control the airflow valves.
Although actuators and sensors often coordinate with each other, they have very different characteristics. Understanding the similarities and differences between them will help you mitigate the risk that comes with designing with these components.