VIP or Via-in-pad technology essentially refers to the process through which vias are fixed directly underneath component contact pads. In terms of PCB design, it refers to a plated hole that supports the linking of copper traces from one layer of the circuit board to subsequent layers. The use of via-in-pad in PCBs is on the rise because of the shift towards sleeker HDI design and form factors. Other benefits include the possibility to reduce inductance, enhance the density and utilize finer pitch packages.
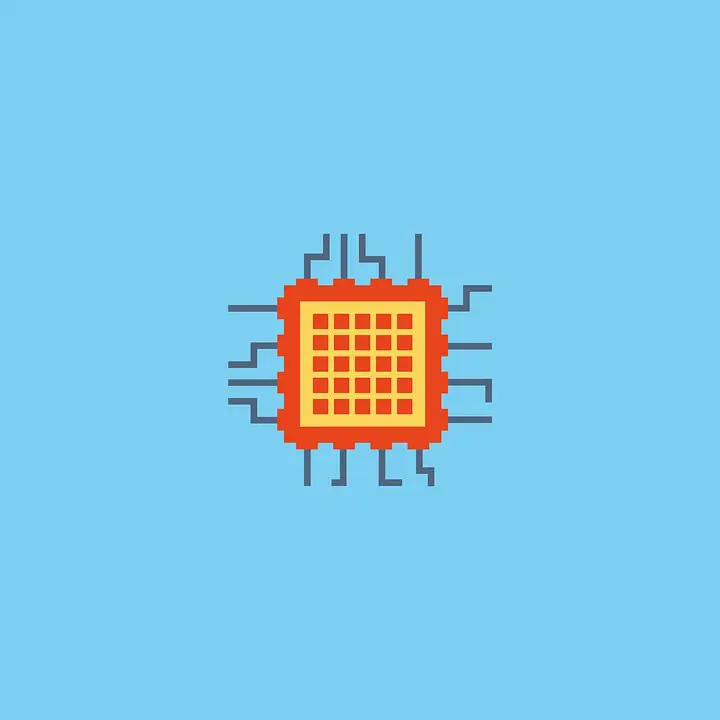
(Pixabay / TakeArtIllustration)
As opposed to buried or blind vias, via-in-pad technologies offer several advantages:
- They are useful for heat dissipation, so they play an essential role in thermal management
- Vias are capable of supporting a flat surface when it comes to component attachment
- Ideal for fine pitch BGAs (Ball Grid Arrays) as they overcome roadblocks like low inductance
- Via-in-pads help make PCB routing efficient and better and footprints smaller
When it comes to via-in-pad routing, the most logical reason to use it is space. In the majority of instances, either the PCB’s surface routing capabilities are restricted, the size of the board is limited, or the design components have very tiny connection pads. In comparison with other choices, VIP allows for easier routing for BGAs (even ones smaller than 0.70 mm).
Additionally, without surfacing routing from SMDs, you can put bypass capacitors near the components, which helps reduce inductance. This is recommended if you’re looking to improve in the area of thermal management. Via-plugging isn’t required in this approach, as the vias are housed directly beneath the component. Also, VIP is supportive of component grounding at high frequencies.
Owing to these benefits, it’s a good idea to familiarize yourself with via-in-pad best practices. For instance, choose the smallest possible diameter for the vias. Manufacturers using laser drills are the best to work with because they can achieve lower aspect ratios. Besides that, follow the guidelines provided by component manufacturers for via filling or capping. Lastly, don’t leave vias exposed unless it’s unavoidable. Doing so exposes the inner copper of the vias to oxidation and elements, which can shorten the lifespan of the circuit board.
Some manufacturers may discourage you from leveraging VIP technology for SMB routing because of the additional work and costs involved. However, if you’re keen to reduce the size, you shouldn’t be afraid of the challenge. Try finding contract manufacturers who are aware of via-in-pad best practices so you can make a PCB size that your clients and design demand. Of course, watch out for the limitations of this approach. As an example, filling extra vias adds complexities like having to use another conductive material or covering the vias with copper. To prevent these complications, make sure your manufacturer can remove the potential surface bumps so there are no issues in optimizing the surface of the board.
Via-in-pad myths to be mindful of
Is via-in-pad a burden on PCB users? Is it a fad that’ll pass away with time? Or is it actually useful? Here are some of the common myths associated with VIP technology.
- Extra solder on BGA pads can accommodate via-in-pad
Not so fast. Via pads in holes will function as capillary straws and remove solder from the pad. In fact, if the vias are exposed, there could be wicking issues that ruin the overall effort. You might end up with a lesser quantity of the solder or a bump beneath the border that could result in shorts. What this implies is that the additional solder in BGA balls will just create issues on the backside of the PCB. Internal bubbles may also come up and cause voids in the joint.
- Vias on sides don’t create any problems
Wrong. Placing the via right beside the pad leaves a metal path between them, which may lead to similar issues as with via in the BGA pad. Therefore, the best practice is to place the vias a ‘hair’ away from the pad and place a solder mask dam in the space. The mask dam will prevent the solder from getting into the via and the assembled PCB will thank you for ages.
To sum things up, the use of via-in-pads in small-scale PCBs will only continue to grow. Although buried and blind vias are important for PCB real estate efficiency and density enhancement, via-in-pads are the best option as far as high-speed design elements and heat dissipation is concerned. Use them correctly, and you should able to get the most out of them without issues.