Buyers new to the PCB (printed circuit board) industry may have questions about how you price a particular project. Raw materials and manufacturing overhead aside, when fabricators sit down to calculate the pricing of a PCB to make a quote, there are multiple cost considerations to consider, such as layer count, the board size, surface finish, and more. This post will highlight the typical factors that fabricators consider when quoting PCBs, so you can better understand how to price and plan your next project.
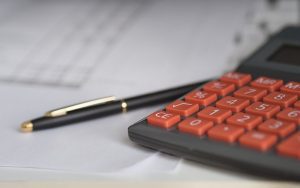
(Edar / pixabay)
PCB Cost Determining Factors
Panel/Board Size
The panel is one of the most important materials required when creating a printed circuit board. The dimensions of your circuit board and how much space it covers on a panel will be crucial in calculating a fair price. Usually, the larger the circuit board, the higher the costs. However, there are cases where a smaller board requiring a specific panel could also be more expensive.
Quantity
Many manufacturers have minimum order requirements. If a project only requires ten pieces, but the minimum order cap for the manufacturer is 20, you’ll need to consider this in your quote. Some manufacturers can offer discounts on higher quantities.
Lead Time
An accelerated lead time often leads to a higher cost. If a customer needs access to their PCB as quickly as possible, applying an additional charge for “express” work is often possible. There are real costs associated with prioritizing new projects more than existing work for any manufacturer, and this expense needs to be featured in the quote.
Layers
The number of layers in a PCB is also a significant determining factor in cost. Double or single-sided PCBs are usually around the same price to create. However, multi-layer PCBs are more expensive due to a more complex manufacturing process and additional materials. The more intricate the multi-layered PCB becomes, the higher the price can be.
Inspection Charges
Before being shipped to clients, the final PCBs must undergo rigorous checks to ensure functionality and quality. Electrical testing, impendence testing, ionic testing, and other strategies are crucial in ensuring the piece’s value. These inspections often add around 10% to 15% to the cost of a project.
Drill Size and Count
The size and number of drill holes in a PCB project will significantly impact the cost. Projects that require very small holes, often under 0.12”, will incur additional costs due to the demand for advanced laser drill techniques and tools. A larger number of holes can also increase the cost due to the manufacturer’s need for more intricate work.
Surface Finish
Boards are usually protected in PCB projects with corrosion-resistant finishes. Highly specialized finishing and coating options are also available to strengthen the longevity of the PCB assembly. Upon request, some manufacturers will be able to finish the PCB project with the coating most suitable for the client’s needs. However, advanced finish options will incur additional costs.
Material Thickness and Types
There are various material types suitable for the construction of a PCB. The most common option is FR-4, a fiberglass material woven with epoxy resin. Various other materials can be involved in manufacturing a PCB, including copper foil, polyimide, and hybrid-capable products. The type of material and the thickness of the substances used will significantly impact price.
Raw Material Type and Size
PCB manufacturing utilizes various materials that have excellent corrosion-resistant properties. Common materials include fiber glass, polyimide, and copper foil. Of course, a fabricator needs to use more raw materials in a multi-layered PCB assembler compared to fabricating a single-layer board. Thinner boards may require smaller PCB components, which are more expensive to source than bulkier products. On top of that, they require high-precision tools, so the size of raw materials can raise the PCB costs in the final assembly.
Trace/Space
Most of today’s projects require very small components. This means the spacing between copper components on a board needs to be as small as possible. To keep board costs low, it’s crucial to leave as much space available as possible. A trace/space dropping below 0.006% may increase the cost of the PCB by 5% to 10%.
Filling Vias
The vias in PCBs generally aren’t completely filled, but this may be required for some specialist projects. When customers require the filling of vias, fabricators need to use special conductive or non-conductive materials to complete the project.
Tooling Charges
Tooling costs may include costs for CAM use, film access, and so on. There are various crucial tooling charges that you must consider depending on the strategy you use to build the PCB.
Specification Standards
IPC Class 2 is the most common standard required for a final printed circuit board inspection and quality check. Class 3 represents an upgrade that requires additional processes like cross-sections being added into the manufacturing process. Customers requiring a higher degree of quality assurance may request a Class 3 process, adding up to 10% to the project.
Add-Ons
Some projects will require additional fabrication on the typical circuit board. When customers have special requirements, like the inclusion of countersinks, counter-bores, complex routing, and controlled-depth drilling, this increases the project’s overall cost. The costs of adding further functionality to a board will depend on the skill and processes required.
Overall, the price of a PCB doesn’t always reflect the true costs incurred in manufacturing. Factors like board failure due to a flawed process and delivery delays can result in a higher manufacturing price. So, when quoting your next project, be sure to factor in all factors, ask the right questions, and design for optimal cost efficiency and performance.
More questions? As leaders in electronic manufacturing services, we can help. Contact our EMS Solutions team at 801-543-9445.
Video
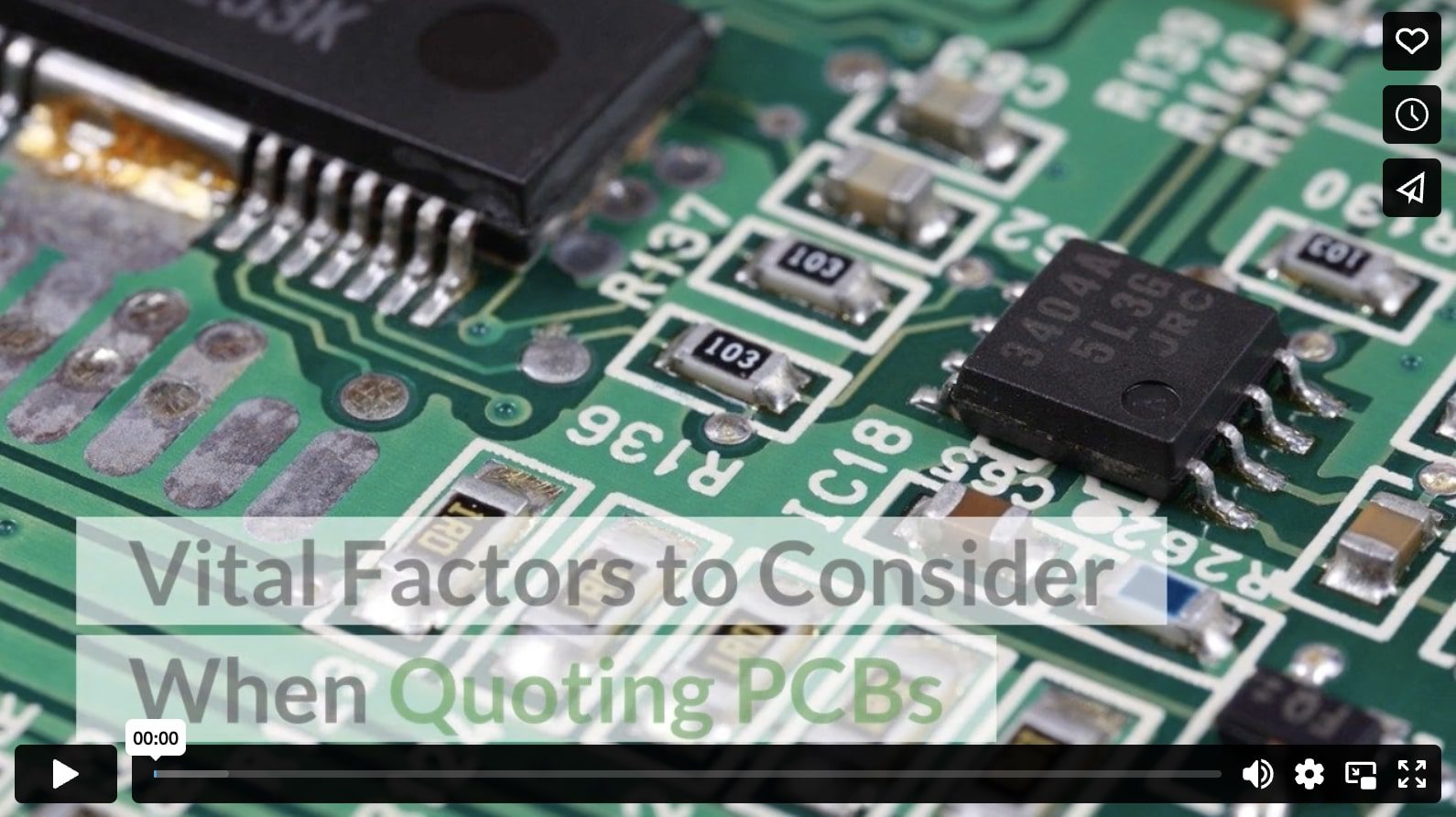