PCBs, or Printed Circuit Boards, are flat boards on which circuits are built. Electronic components that fulfill the actions intended by a board are installed onto their surface by soldered pads. Etched traces are lined with a conductive metal, usually copper, connecting each component to create paths that can pass power and data efficiently.
PCBA manufacturers make the boards from a material known as a substrate, which is intentionally non-conductive so that the signal sent through the circuit does not dissipate or disrupt. This is ideal for keeping the surface components clear of potential issues but limits the board to a single-layer design.
To allow boards to work on multiple levels, designers must employ PTH and NPTH in their plans.
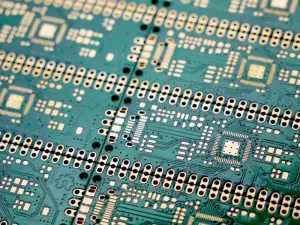
(Vishnu Mohanan/Unsplash)
What are PTH and NPTH?
Both terms refer to holes drilled through a board. TH stands for Through- (or Thru-) Hole, simply describing that the hole reaches from one side to the other. Where they differ is in the first two initials, which stand for the following:
- PTH – Plating Through Hole
- NPTH – Non-Plating Through Hole
While this may seem like a simple distinction, the two terms mean entirely different things for the function and design of a PCB.
Definition and Purposes of a PTH
As the name suggests, a Plating Through Hole (PTH) refers to a hole plated around the inside with the same conductive metal used on the PCB’s surface traces. During a through hole assembly, the technician installs a circular pad onto the top and underside surfaces of the hole, which connects the hole to the traces of the board’s circuit. The inside portion of the hole that connects these two pads is plated with the same conductive metal, connecting the two sides as part of the circuit.
Designers use PTHs to allow a current to pass through components on one side of the board, down through the non-conductive substrate of the board itself, and out to the other side. This technique means that boards can hold components on both sides or connect multiple layers. This is ideal as it allows designers to utilize the space allotted to them much more efficiently.
The more components a board requires, the bigger the circuit will need to be. This is acceptable for a large device or machine, but smaller boards are necessary for smaller devices. By using PTH as a design factor, you can stack the boards vertically, reducing the overall size of the PCB and allowing more components in the smaller space.
But here’s the thing: PTH is, by definition, designed to go entirely through a board. Some board designs use multiple layers as heat sinks to draw heat away from components to conductive layers between the substrates. To access inner layers without going all the way through, designers will need to use vias, as opposed to PTH. Vias are specifically designed to only pierce through one surface, connecting the top layer to an inner layer without breaching the other side of the board. A hole is only considered a through-hole if it goes all the way through a board.
Definition and Purposes of NPTH
Given the description of PTH above, Non-Plating Through Holes follow the similar rules. The primary difference is that the inside surfaces of the holes are not plated in conductive materials. An NPTH does not serve the same purposes as a PTH, as it cannot pass any current through it. The specifications of a board’s design will indicate whether a through-hole will need to be plated or not.
In some cases, an NPTH will still feature pads on either side, but this doesn’t indicate a connection. Pads are used as guides for NPTH placement; most won’t use them at all, instead standing as a simple hole in the circuit board. Whether it’s a manual or automated through hole assembly, designers must make sure they correctly set an NPTH as mistaking one for a PTH may cause issues with the board’s circuit pathing. A PTH set where an NPTH is needed will cause the charge to be misdirected or spread too thinly, weakening the charge or causing bridging that leads to short circuits.
The primary function of an NPTH is to act as a guide for mounting a PCB. Typically, NPTH provides a channel through which bolts or screws can secure the board. In other cases, wires or pins will be threaded through them. In both examples, the components threaded through mustn’t interrupt the board’s circuitry. The non-plated nature of the NPTH will allow that to happen.
Adding PTH/NPTH to a Board Design
The two types of through holes are added to the board at different stages in the manufacturing process. There are a few rules to keep in mind before you start drilling:
1. When to drill the through holes
Always drill a design requiring a Plating Through Hole into the board substrate before the electroless plating process. This way, when the traces are filled and the conductive material is set, it will coat the inside of the holes, creating a solid circuit. For Non-Plating Through Holes, you must drill them after the plating process. This way, the hole will remain clear of plating material.
2. Consider hole width
The standard dimensions of any through hole are:
- 0.005” minimum edge-to-edge clearance from any surface element for NPTH
- 0.006” minimum finished hole size for PTH
- 0.009” minimum edge-to-edge clearance from any surface element for PTH
- 0.006” minimum finished hole size for NPTH
- 0.004” minimum annular ring size for NPTH
These are intended to give each through hole adequate coverage and space from other components to prevent interference. Additionally, consider the size of any plugs or bolts fed through an NPTH to ensure adequate surface clearance.
Through-hole technology is not as simple as just drilling a hole through a PCB. Each hole must serve a purpose or it risks becoming an extraneous cost to the manufacturing process or a danger to the PCB’s structural integrity. When designing through holes, consider their purpose carefully, and ensure manufacturers clearly understand what it is.