As an electronics manufacturing services provider, one of the most common questions we get asked is, “Why does this product cost that much?” It’s a valid question, and we understand that cost is an important consideration for our customers.
The truth is there are many factors that contribute to the price of an electronic product. From the cost of raw materials to the complexity of the manufacturing process, every aspect of production plays a role in determining the final price.
In this article, we’ll explore some of the key drivers that impact the cost of electronics products, so that you can better understand what goes into making the gadgets you use every day.
So, if you’re curious about what drives up the price of an electronics product, read on.
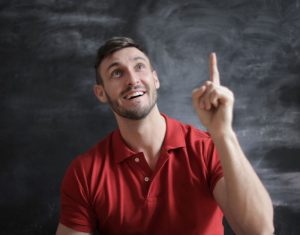
(Andrea Piacquadio/Pexels)
Raw materials
Raw materials are a crucial component of electronics manufacturing, and they significantly impact the final cost of the product. Choosing the right materials can help manufacturers keep costs down and improve profit margins, whereas selecting the wrong materials can lead to over-inflated invoices and wasted resources.
One way that raw materials affect manufacturing costs is through their availability and cost. Some materials, like rare earth metals, are difficult to source and can be very expensive, driving up the cost of the final product. Manufacturers need to consider the cost of raw materials when choosing suppliers, and they may need to adjust their production processes to account for fluctuating prices.
Additionally, manufacturers must stay up-to-date with the developments of new materials to take advantage of potential cost savings. For example, newer plastic resins and metal alloys offer similar properties to more expensive materials, allowing you to achieve the same performance at a lower cost.
Ultimately, understanding the properties and costs of different materials is crucial for keeping electronics manufacturing costs under control.
Labor
Labor costs play a significant role in determining the price of a product. If the labor costs are high, the production costs will be high as well. In some cases, basic or automated tasks may not require highly skilled labor, enabling you to save on costs without compromising product quality.
However, it’s important to avoid prioritizing the lowest labor costs as this can lead to poor quality and manufacturing shortcuts, creating liabilities for the customer. Instead, a better investment is to work with suppliers who combine lean manufacturing with skilled workers to achieve high quality and minimal waste.
Volume
The cost of manufacturing electronics products is also closely linked to the volume of items. Generally, the higher the number of items purchased, the less each item will cost. This principle is why customers often pay more upfront to gain savings over time.
Additionally, the manufacturing process you adopt also influences the cost per item. For instance, the die-casting process for aluminum components requires a heavy capital investment, including purchasing casting equipment and making the metal die. In cases where the product is being manufactured in low volumes, die-casting is not a cost-effective option. However, for higher volumes, the tooling and equipment costs can be distributed over time, resulting in cost savings per item.
As a result, manufacturers need to carefully consider the product volume and the most appropriate manufacturing process to use for each product. By taking advantage of economies of scale and using the most efficient processes, manufacturers can keep costs down and offer competitively priced products to their customers.
Manufacturing techniques
When manufacturing electronic products, choosing the right manufacturing process is critical to ensure the product’s quality and durability and minimize costs. Depending on the product and its application, different processes can be used, such as compression molding, extrusion molding, or plastic injection molding.
For instance, if you want to make a plastic part, extrusion molding, and compression can be more cost-effective than injection molding, which is more suitable for complex items and requires an injection tool to be constructed. However, keep in mind that the tooling process and design can significantly impact the initial cost. It’s essential to consider both the application and cost when selecting a manufacturing process, as changing the process later may not be feasible.
Part complexity
Part complexity can also play a significant role in determining an electronics product’s cost. While complex designs seem to improve the look or performance of a product, they can actually be more expensive to make and hinder the product’s utility and performance. The more complex a part, the more time-consuming it is to measure its various features. And this can result in additional manufacturing expenses.
To keep costs down, it’s best to design parts to be only as complex as they need to be and no more. This approach will ensure that you are not sacrificing performance or utility for a more complex design while keeping costs under control.
Certification and testing
Electronic products often require federal approval or certifications before they can be released to the market. For instance, medical devices must receive approval from the FDA, while devices that come into contact with food require a UL/ETL safety certification.
If products are released without these approvals, it can lead to costly consequences such as recalls, fines, and damage to reputation. Therefore, the testing and approval methods have a direct impact on manufacturing costs.
Furthermore, the review process can extend the time to market, which can result in increased manufacturing costs due to required product revisions and refreshes. Therefore, manufacturers must take all these factors into account when planning the production of electronics products.
Final verdict
To conclude, all these factors make it difficult for electronic product manufacturers to give a direct quote without a detailed understanding of the product and its application.
As a result, it’s crucial to work closely with an experienced electronic assembly solutions provider who can help navigate these complexities and provide customized solutions to meet specific needs and budgets.
The best providers will assess your product’s design, create an efficient manufacturing process, and manage the supply chain to ensure cost-effectiveness while delivering quality products.
Infographic
Electronic prices depend on various factors, such as material selection, labor costs, production volume, manufacturing methods, product complexity, and testing expenses. Skilled manufacturers balancing cost and quality are crucial. Materials, labor, and production volume affect pricing, with manufacturing methods and complex designs impacting costs. Efficiently managing testing and certification is essential to avoid extra expenses and delays.