What makes printed circuit boards (PCBs) so reliable? Although many processes are involved, one that caught our attention is PCB baking.
PCB baking helps eliminate potential defects and ensure optimal performance. It also protects small and delicate printed circuit boards from delamination. Curious about how it works? This post provides a closer look at PCB baking and its role in creating top-quality electronic assembly solutions.
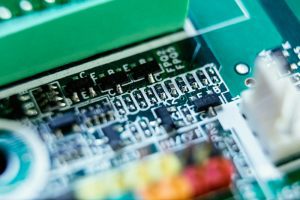
(freepik/Freepik)
What is PCB Baking?
PCB baking is a method for removing moisture from printed circuit boards. When the PCB’s surface gets cooler than its surrounding air, it attracts moisture. This moisture can become trapped inside the board, and if not addressed, will transform into steam during PCB processing. Steam may damage the board or disrupt its circuits.
Different composite materials in the PCB dictate its moisture retention. For example, Polyimide flex and rigid materials absorb more moisture than FR4 panels. Fortunately, PCB baking can help extract moisture from these materials, improving the performance of the overall board.
How does PCB baking work?
In the baking phase, an oven heats the PCB to a range of 100°C to 130°C. This heat evaporates the board’s moisture. But it’s crucial to monitor the temperature. Overheating or extended baking can also damage the PCB.
Measuring the board’s weight helps confirm moisture removal. One primary goal of PCB baking is to stop delamination. This issue arises when moisture escapes through copper via holes. On some multi-layer panels, moisture gathers in holes or at epoxy-composite junctions. This accumulation can cause delamination or “measling.”
Why are PCBs baked?
Baking circuit boards serves several purposes. One key reason is to stop condensation from exiting through gaps coated with copper. Another is to limit outgassing. These problems can create blowholes or pinholes. They can also impact soldering quality during both manual and machine processes. Moreover, baking helps to guard against delamination or measling during solder adjustments.
During drilling or mechanical actions, damage can occur. This damage affects the bond between the glass fabric and epoxy. However, modern surface treatments and copper layers usually ensure a strong bond.
Is baking necessary for all printed circuit boards?
PCB assembly companies must remove the moisture from their circuit boards. Baking can help in this regard. A moist board, when used in equipment, might not work properly.
That said, not all PCBs need baking. A better strategy is to avoid moisture from the outset by using preventative measures during PCB design and production. The board’s design can dictate the need for baking. Checking PCB lamination in a temperature-regulated setting often does the trick, effectively drying the board.
Conditions for Effective PCB Baking
As you can see, PCB baking represents an effective tool in combating moisture. The process has specific steps you should follow to ensure optimal results. Here are essential conditions to remember, particularly when using OSP surface finish:
- Short-term storage (up to 2 months): Bake the PCB at 120°C for one hour.
- Medium-term storage (up to 12 months): A two-hour bake at 120°C is recommended.
- Extended storage (6-12 months post-production): Producers should bake their PCBs for four hours.
- Long storage (exceeding 12 months): A six-hour bake at 120°C is advisable. However, prolonged storage might compromise PCB layers. Such PCBs might not be ideal for use because of potential layer damage, leading to reduced performance. Expired PCBs can have weak soldering, instability, and issues with solder paste. PCB parts will likely detach, so surface finish alterations might be necessary. Switching to ENIG can extend PCB longevity to 12 months while safeguarding layers and reducing contamination risks.
- Post-Baking storage: After baking, producers should store PCBs for no more than five days. They should then either list them online or deliver them. If delays occur, rebaking before online listing becomes essential.
For best results, make sure to position the PCB about midway between the top (furnace) and the bottom (detector).
Rigid PCB Process for Different Surface Finishes: ENIG, HASL, Lead-Free HASL
All PCBs, regardless of thickness, undergo baking for a minimum of 2 hours at 120°C. The duration between baking and soldering varies based on storage conditions. Specifically, at a relative humidity of 50%, the recommended maximum hold time stands at 8 hours. However, if boards are maintained in an oven at 35°C, this hold time can extend beyond the standard duration.
Purpose of the Baking Process for Components
The primary aim of the baking process lies in eliminating the moisture content present in specific electronic devices, especially those termed as moisture-sensitive parts.
Moisture-sensitive plastic packaging surrounding a part can pose a significant risk. When preparing to assemble a circuit board, this packaging can absorb water. During the reflow soldering phase, the absorbed moisture can lead to catastrophic outcomes due to the elevated temperatures of the process. This intense heat causes the trapped moisture to form water bubbles within the plastic packaging. The expansion from these bubbles can deform the part, often resulting in damage to its internal components.
One of the evident repercussions of moisture sensitivity is the reduced shelf life of components. If you aim to prolong a component’s shelf life, it’s essential to understand that this lifespan largely depends on its moisture sensitivity level. Components with a higher sensitivity level will absorb water more quickly, thus diminishing their longevity.
The PCB baking process helps keep electronic components working well. It removes unwanted elements by heating between 100°C to 125°C, thus preventing issues. To get the best results, it’s good to work with a skilled PCBA manufacturer. Such experts bring unmatched precision to the forefront, ensuring that PCBs consistently meet industry standards.
Infographic
Printed circuit boards (PCBs) rely on various processes for reliability, with PCB baking standing out for its role in eliminating defects and enhancing performance. This process safeguards delicate PCBs from delamination, ensuring top-quality electronic assembly solutions. Delve into the mechanics of PCB baking to understand its significance in ensuring optimal PCB functionality.
Video
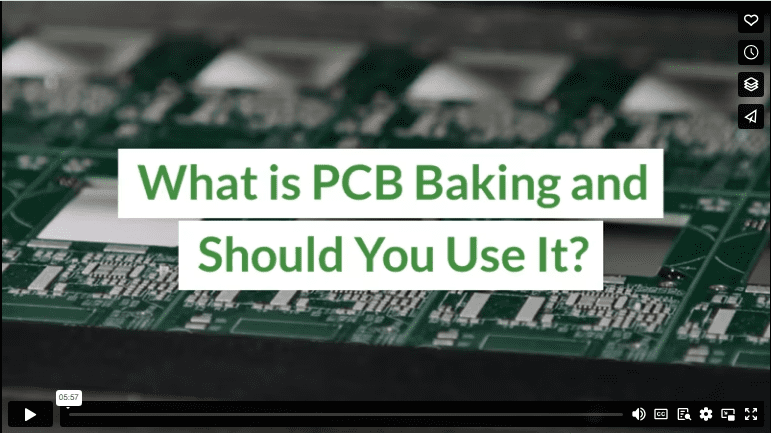