Since that early development, PCBs have changed dramatically with many milestones, including double-sided, multi-layer versions with surface mount parts. Then came micro-via technology, markedly reduced trace and space, and flex PCBs.
Today, the evolution continues as demand drives innovation for exciting new possibilities. What’s next for PCBs? We asked industry experts to weigh in. Here’s what they said:
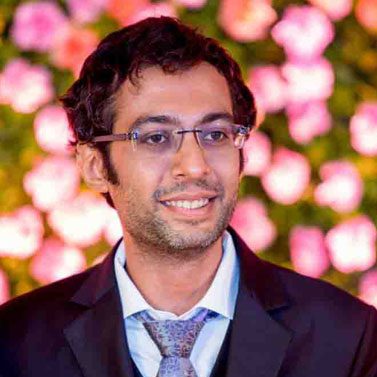
Rohit Dewani
Inbuilt Passives: Right now, companies have to buy lots of passives such as capacitors, resistors and inductors. The passives [constitute] the highest number of components in a typical Bill of Material (BOM).
With the technology improving exponentially, we will be able to highly control the dielectric layers and copper tracks within extremely tight tolerances. Hence, within 10 years we might see passives built into the circuit board. This will drastically reduce the cost.
Aluminium PCBs: Aluminium PCBs will be easy to manufacture. This will lead to a paradigm shift in PCB manufacturing as aluminum is cheaper and has better heat sinking capabilities than copper.
In-house flexible PCB: With PCBs becoming thinner every passing year, in the future, we well have PCB sheets as thin as paper. We will have a PCB printer, which will print out PCBs in our offices within no time.
Additive manufacturing, or 3D printing, has been a growing technological advancement. Now government agencies such as NASA and the Department of Defense are investing heavily in the utilization of 3D printing to produce electronic circuitry. Why? Besides the notion of convenience, there are notions such as adaptability and resource management. Suppose you could design and fabricate any circuit you needed on-demand from only a base set of raw materials, and even recycle it once done? Suppose active devices could be created in space or on a mission? How powerful of a concept would that be?
The majority of electronic circuitry is produced by the intelligent combination of materials connected together. These materials are (1) conductive, (2) insulating, (3) resistive, (4) capacitive, (5) N-type semi-conductive, and (6) P-type semi-conductive. Individual elements are produced by calculated geometries from these materials. While there has been [progress toward] 3D print circuit boards, and even other 2-dimensional planar circuitry, fully 3-dimensional electronics devices have not been successfully developed. Until now.
The Electronic Alchemy eForge is a fused deposition modeling-based 3D printer. It utilizes up to eight different extruders that deposit the material from proprietary filaments that have the electrical properties of the six stated above. EA was funded by NASA to develop this technology for their use and for commercialization. Its developers are collaborating with Autodesk for the use of their CAD packages such as Tinkercad and Fusion 360 for layout and design. Currently, Electronic Alchemy is in the midst of a Kickstarter campaign, preparing for product release in the third quarter of 2020.
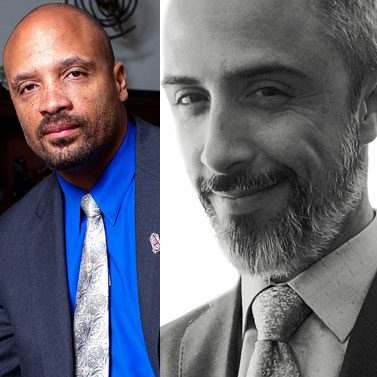
Chance Glenn & Jason Burr
Shayne Sherman
Perhaps they will evolve so that they aren’t the middle-man of electronics, but the active component of tech systems. The circuit would be transmitting information and instructions for itself, instead of an outside system.
This is a crowdsourced article. Contributors' statements do not necessarily reflect the opinion of this website, other people, businesses, or other contributors.