Vias are an important aspect of PCB assembly and design. Essentially, they are specially created holes lined with a conductive material and act as bridges between the layers of a board. Vias are used to bridge gaps when a board requires multiple layers, whether to allow for more components or for better heat displacement.
However, installing vias into a board is not as simple as drilling through the substrate and calling it a day. How you plan a via is based on how the board needs to use them. Some boards will require standard vias, while others will require you to perform via tenting.
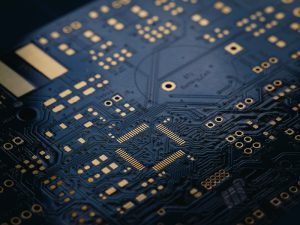
(Vishnu Mohanan/unsplash)
What is Via Tenting?
A standard via is a hole drilled into the surface of a board. A coating applies to the hole in the conductive copper that makes up the circuit traces on the board’s surface. The underside of the via will connect with another set of traces or a solid material layer. This structure means a current can pass through the circuit through the board, then down through the via. It resumes its journey on the next layer. Vias allow a multi-layered board to form a seamless circuit without using leads or other connective materials.
For a standard via, the surfaces of the drilled holes are left exposed, which is where tenting comes in. Tenting a via means to cover the surface hole of the via after drilling it. A solder mask covers the annular ring (the copper ring around a via) and the via itself, safely sealing the copper.
In the early days of PCB assembly, technicians rarely used tenting vias. This is due to the material used to cover the vias – a substance known as a Liquid photoimageable (LPI) solder mask. More recently, manufacturers have begun using Dry-Film solder masks instead, making the process of via tenting much easier.
The Benefits of Tenting Vias
Vias are typically exposed on the surface of a PCB. It may seem that this state is important to the function of a completed circuit, but tented vias also provide a few benefits for PCB design.
The most common issue that arises from exposed vias is oxidation and rust. Exposed traces are always at risk of eventual oxidation caused by ambient moisture, which will interrupt the flow of a current through the traces. Tenting vias are not exposed to this ambient moisture and therefore are less likely to suffer from oxidation and rusting.
Since you can’t remove the board for regular cleaning, keeping them covered is the most effective protection method. The breakdown of exposed copper also will lead to current disruption and physical damage to the board itself. This damage can lead to further unfixable issues, such as warping in the board substrate, rendering the PCB useless.
Tenting vias are protected from corrosion. Moreover, they are covered in case loose components or other debris gets into the through holes. These issues can cause shorts in the circuits and other physical damage.
Some boards will require you to plug exposed vias – have a non-conductive material inserted in the via hole – to prevent these issues, but tenting is a much cheaper option. Since tenting only requires a thin layer of solder mask over the hole, it uses fewer materials than a whole plug. This makes it a money-saving option in PCB assembly.
When Should you use Tenting Vias?
Some PCB designs require tenting vias to comply with DFA of reliability requirements, making it necessary for the manufacturing process. In cases when it is not a requirement, tenting is a good addition for many reasons, such as:
Environmental Protection
You should consider Via tenting for cases where the PCB is installed into machines or locations likely to suffer environmental damage. This is most common for industries exposed to moisture or corrosive atmospheres. Pool, dock, boat machinery, drilling, mining equipment, or scientific/medical equipment should all incorporate tenting.
Whether or not it is possible to include via tenting depends on the size of the vias in the board. Typically, you use tenting with boards that have hole diameters less than 12mm. This is because bigger holes require more solder mask solution to cover, the strength of which will diminish as the hole increases in size. Consulting a PCBA manufacturer can help you determine which type of mask solution is ideal for the job at hand.
Stop Solder Wicking
Solder wicking happens when beads or drops of solder move out from solder pads, usually by drying or heating. When this happens, beads of solder will dry on parts of the board they should not, which can cause shorts and weakness in the current flow. In the case of vias, wicking solder can become lodged into the through hole, shorting it or blocking it from working.
While some designs allow for vias and through holes to be spaced farther away from solder pads, this is not an option when working with smaller PCBs. In these cases, tenting vias is the best way to prevent solder wicking from disrupting the circuit. When working with smaller boards or machinery, via tenting is a great way to minimize onboard space usage.
Tenting Both Sides of a Via
Typically, it pays to do it on both sides when it’s necessary to tent a via. However, it’s not always necessary, or even possible, to tent both sides of a via.
Some via uses – such as via-in-pad designs or vias in a ground pad – will require you to uncover the hole, at least on one end. In these cases, tenting will not be an option on both ends. As with most design choices, it is best to discuss with the chosen manufacturer whether tenting is required on only one or both sides of the design.
There are many ways circuits can short or become disrupted, and vias represent a particularly troublesome weak point; fortunately, via tenting offers an inexpensive and effective way of protecting exposed and weak areas of a printed circuit board assembly. Sometimes, a thin layer of epoxy is all it takes to prevent a myriad of future problems.